Injection Molding Threads - Free Molding Design Supports
It's common to see injection molding threads everywhere, a soda bottle cap, a nut that attaches to the drainpipe underside of the kitchen sink, cool-looking screws used to assemble a child's toy, etc. These are some examples of the injection molding threaded parts we encounter daily. Injection molding threads are used widely in our life. How to make your injection molding parts in specific threads? These need full consideration not only with part design but also from the manufacturing perspective. Contact our experts to get free support now!
Injection Molding Threads Types
1. Injection mold external threads
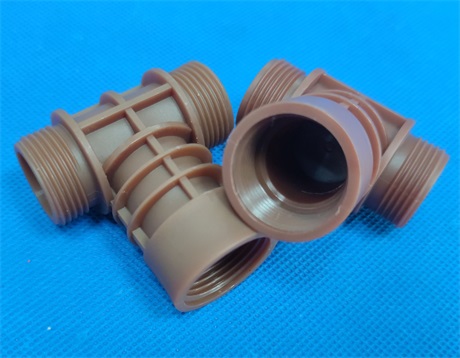
Making half of the threads each on the cavity and core side on the thread mold. This way, the thread can be made by injection molding with no other post-machining. It solves the undercutting problem for tooling and raises production efficiency. The only concern is the tiny parting lines on the thread. These lines are fine for thread attachment but not kind for precise transmission, especially for gear components. Depending on the part's size and geometries, TEAM Rapid always makes the parting lines on injection mold external threads as small as possible!
2. Injection molding internal threads
Injection molding internal threads or thread that does not allow having parting lines on, for these moldings, the thread needed to make on thread mold tool completely without division. We need a third component named thread core/cavity; it has the completed geometries of threads. The tooling structure for these moldings is more complicated than injection mold external threads. The molding cycle's time can vary depending on the thread-released methods.
Injection Molding Threads Released Methods
The mold structure for the external thread is not complicated. The simple open-and-close mold is good for releasing undercuts. But for injection mold, internal and external threads that can't have parting lines undercuts need to be released before opening the mold. Typically, we have the following three injection molding threads released methods:
Force Release Manual Insert Fully Automatic
1. Force Release Molding Internal Threads
- Thread size, pitch, and depth should be small enough to force out.
- Injection material should be flexible enough to avoid the crack issue.
- Wall thickness is consistent; it can't be too thick without sharp corners.
- Draft and radii on the thread are necessary.
2. Manual Insert Release Injection Molding Threads
The thread core/cavity is placed into the mold and ejected out together with the molded part, then released molding internal threads are by hand. The method of the manual insert is suitable for low-volume production. To raise production efficiency and achieve rapid manufacturing, we usually make 2 or even more thread cores/cavities for interchanging.
3. Fully Automatic Release Injection Molding Threads
Fully automatic unscrew molding is a unique injection molding process that includes movement and rotation to produce injection molding internal threads parts. First of all, we need to build automatic unscrew molds. These injection molds' unscrewing action is accomplished with a hydraulic or electric motor, making the thread core/cavity precisely have threads ground on them. The cycle time for automatic unscrew molding can be much shorter than manual unscrewing, but the cost of automatic unscrew mold is expensive. Depending on your production amount, such as large volume production, the automatic unscrew molding cuts down the unit part price, even if by several cents per part, the all-in cost can be reduced quite a lot!
PP, ABS, POM, and PA are commonly used in thread molding. To keep production rolling along smoothly, contact our team at [email protected] to get more support for injection molding thread parts.
External vs Internal Threading
Externally vs. internally threaded? Threading in the injection molding process aims to create a thread or screw system for injection molding products. For instance, plastic bottles will need a kind of threading to allow you to fasten the plastic bottles with their caps. This threading process is common for injection molding products, not limited to plastic bottles. External vs. internal threading? Internal and external threaded are the two types of threading you can apply on the injection products.
Internal Threaded
Injection products with internal threaded, such as those found in bottle caps, internally threaded rods, internal thread tubes, etc., will require you to create the thread inside the product's surface. The challenge in this process is that you will need to maintain the shape of the molded products during the internal threading process. Any wrong steps can cause the internal threads not to form correctly, which might misshape or deform the injection products.
External Thread
External threading means applying external threads or a screw system on the neck area of the injection products. This process will apply the threads on the surface area of the product, which you can perform after completing the primary injection molding process of the product. Internally threaded vs. externally threaded? Compared to internal threading, external threading is much simpler to do.
Threading is an important part of the injection molding process. You will need to use this process to produce injection products with certain fastening or sealing mechanisms. Internally vs. externally threaded? Both external and internal threading will go hand in hand to create the entire product. For instance, with plastic bottle production, you will need to create the plastic bottle body, which uses external threads, and the bottle cap, which uses internal threads. It would be best if you combined the external and internal threading processes to create the complete product. There are some rules for the internally threaded rod and internally thread bolts.
However, during the application, when externally threaded vs. internally threaded, internal threading is much more complex to do than external threading. It requires a more precise internal threading tool, the right material choice, and the trial-and-error process to ensure that the internal threading application won't damage the surface structure of the injection product. Meanwhile, you can apply external threads in simpler ways without going through a complicated process.
FAQ about Injection Molding Threads
1. What are the different types of threads in thread mold?
American Standard 60 sharp thread, tapered pipe thread, and buttress threads are the most frequently specified thread profiles used for plastic molded parts. Among these 3 types, the American Standard or machine screw is the most common. For some special threads, we can consider post-machining threads.
2. Can helicoids be used in plastic molded parts?
Heli-Coils are placed onto the plastic molded parts to enhance the strength and holding power of the screws. They are usually made in hard plastic, steel, or aluminum and installed onto the parts after molding.