Overmolding - Full Technologies to Meet Your Needs
What is Overmolding?
Overmolding, a unique marvel in production and rapid manufacturing, involves the fusion of two or more distinct materials to craft a singular, multifaceted component. This intricate process typically unfolds by molding a robust plastic part, followed by the application of a supple material, resulting in a seamless final product.
Development of Overmolding
Delving into the annals of manufacturing history, the concept of overmolding has traversed several decades, undergoing a metamorphosis spurred by advancements in both materials and technology. In its nascent stages, overmolding found its footing in the fabrication of rigid rubber articles and the soles of footwear. However, the transformative arrival of thermoplastic elastomers in the 1960s bestowed newfound versatility and cost-effectiveness upon the process.
In the contemporary landscape, overmolding has transcended its origins, finding applications across diverse industries such as automotive, medical, electronics, and consumer goods. It has become the linchpin for crafting products endowed with intricate geometries and elevated performance attributes. The evolution of over-molding points towards a promising future as relentless research and development continues to push the boundaries of materials and plastic molding technologies. As we navigate the intricate world of overmolding, we uncover not just a manufacturing technique but a narrative of innovation, adaptability, and boundless possibilities.
The Overmolding Process: How Does Overmolding Work
Overmolding, a groundbreaking technique in manufacturing, choreographs the seamless integration of diverse materials into a singular masterpiece. The process begins with precision injection molding, shaping a robust plastic entity. It sets the stage for the subsequent dance, where a complementary, pliant material gracefully over-molds onto the initial structure.
Heat and pressure act as virtuoso conductors. Elevated temperatures render the primary plastic entity pliable, setting the stage for the over-molding duet. This orchestrated performance continues as pressure takes center stage, ensuring a seamless integration of materials. The result is not just coexistence but a fusion, bestowing the final piece with heightened resilience, ergonomic finesse, and visual allure surpassing the mere sum of its parts.
Types of Overmolding Operations
l Manual Overmolding: Reducing the Tooling Costs
In the domain of overmolding, manual injection moulding executed in two distinct steps. Firstly, a substrate undergoes the meticulous process of molding and subsequent cooling. This substrate, guided by a skilled operator, then transitions to a second mold. Here, the over-mold material is injected, seamlessly bonding with the substrate. This manual process excels in demanding meticulous attention to detail.
Manual molding finds its niche in low-volume or rapid prototyping production, where the economics of automation may not be justified. Manual overmolding becomes particularly when the substrate and over-mold material require distinct molding conditions, or some projects need in reducing the tooling and sum costs.
l Two-Shot Molding: Excellent for high-volume production
In overmolding, a specialized machine equipped with twin injection units orchestrates a seamless ballet of substrate and over-mold material. The substrate takes the spotlight first, molded with precision. Then, in a harmonious rotation or shift, the over-mold material joins the performance, creating a union that transcends individual elements.
The advantages of two-shot molding resonate across the manufacturing landscape. From heightened production speed to unwavering part quality, this method introduces a level of efficiency that reshapes the narrative of over-molding. The need for specialized machinery and molds reducing the molding costs, making it most cost-effective in high-volume production scenarios. As the two-shot process unfolds, it epitomizes a fusion of art and technology, crafting a story where precision and efficiency coalesce into a harmonious crescendo.
Pros and Cons of Overmolding
Pros:
This intricate process seamlessly integrates complex parts in a singular, efficient endeavor, significantly curtailing assembly time and associated costs. Its transformative touch extends beyond functional enhancements to encompass the realm of aesthetics, introducing elements such as soft-touch grips, seals, and captivating color contrasts. The protective embrace of overmolding acts as a shield, fortifying products against the challenges posed by impact, vibration, and environmental factors, elevating their overall durability and resilience.
Through the overmolding process, designers add a soft-touch exterior onto their parts to enhance the grip feeling or mold the part in 2 or more different materials to implement the functions. The part in overmolding looks more attractive to consumers. There is plastic overmolding, rubber overmolding, silicone overmolding etc. Here's a more in-depth look at its advantages:
1. Implement the functions.
Overmolding Taking an electric front cover, for example, consists of 2 parts, part one is in hard plastic (typically PC/ABS), and part two is a window in clear PC, molding these 2 parts into one single component by plastic overmolding, we can get a plastic cover not only with clear window but also strong strengthen.
2. Enhance the products performances.
Overmolding injection molding soft touch rubber (typically TPE) on the grip can reduce shock and vibration, provides electrical insulation, dampens sounds, and improves chemical/UV resistance, which highly enhances the performances of the products after rubber overmolding.
3. Increased shelf appeal.
The overmolded part can be in 2 or several colors or materials by over-molding, which helps the product stand out from the competition, it increases shelf appeal.
4. Production available in cost effective way.
The overmolding process is mature in the industry. The overmold parts can be produced cost-effectively, even for low-volume production.
Cons:
Within the expansive landscape of over-molding, challenges and considerations emerge. The necessity for specialized machinery and molds, while pivotal, demands a notable upfront investment, contributing substantially to the initial setup costs. Material compatibility stands as a critical linchpin, tethering the process to a subset of materials capable of harmonious bonding. The design complexities inherent in overmolding necessitate meticulous attention to both part geometry and intricacies in mold design. In the economic calculus of production, the brilliance of over-molding may encounter a diminished luster in scenarios of low-volume production, where the setup costs cast a substantial shadow over its cost-effectiveness. In navigating these dualities, the mastery of overmolding requires not only technical acumen but a strategic orchestration of resources and considerations.
Overmolding Materials
Material Selection for overmolding: Precision in Choices - Accurate selection requires attention to 2 points:
l Variety of Material Options
In the realm of overmolding, a diverse selection of materials takes center stage, each contributing uniquely to the final product. Thermoplastic elastomers (TPEs) ascend with acclaim, lauded for their flexibility, durability, and adept bonding capabilities. Alongside, thermoplastic urethanes (TPUs) command attention for their exceptional abrasion and tear resistance, marking a pinnacle in durability. The ensemble finds completion with the entrance of silicone, renowned for its prowess in heat resistance and a soft tactile appeal that resonates across varied applications.
l Accuracy Guidelines
Precision serves as the guiding principle. Primarily, compatibility takes precedence. The over-mold material and substrate must align seamlessly in melting temperatures, engaging in a harmonious bonding during the molding process. This compatibility forms the foundational bedrock upon which the success of the over-molding endeavor rests.Secondarily, the material must align harmoniously with the envisioned performance characteristics of the final product. Softness and flexibility may call for the grace of TPE, while products facing the rigors of high temperatures might find resilience in silicone. In conclusion, pragmatism unfurls in the consideration of cost, influencing the material choice within the pragmatic confines of the project's budget.
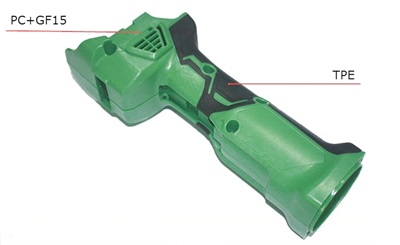
Our Suggestions For Overmolding Materials Selection
Choosing the right overmold material is critical to your part's success in its application and the product's performance. For overmolded parts, we can have the materials:
1. Soft plastic (usually for rubber overmolding) is molded into a second hard plastic.
2. Hard plastic, such as overmolding nylon, PMMA, etc., is molded into a second hard plastic.
We need to consider the materials' compatibility before using the specific material. If the material is incompatible, the rubber on the Hogue over-molded grip will easily peel off or even not adhere to the material, directly leading to the part's functional problem. Below are the summary of materials commonly used in orvemolding:
TEAM Rapid is one of the best overmolding suppliers. We have strong partner relationships with resin manufacturers. We can get special-purpose resins to meet your products' over-molding requirements at a competitive cost, no matter whether overmolding nylon, cable overmolding, or others. We can give you the best solution. Contact us today to learn more now.
Overmolding Design Guides: The Factors You Need To Konw
When delving into the intricacies of overmolding design, an array of factors demands consideration. Firstly, the compatibility of substrate and over-mold materials stands as a pivotal factor. The melding of these materials during the molding process relies on their harmonious bonding and compatible melting temperatures. The part's geometry plays a crucial role, necessitating efficiency in molding and de-molding processes. Special considerations come into play with intricate features or undercuts.
The final product's requirements further influence the design landscape. Mechanical properties, aesthetic appeal, and cost considerations become integral components, steering the design process toward an optimal outcome.
Precision in mold design is paramount, influencing the effectiveness of the over-molding process. The mold must not only accurately form the substrate but also facilitate the seamless injection and bonding of the over-mold material. Efficient cooling and de-molding become imperative factors.
Poor mold design could cast a shadow over the final product, leading to defects such as warping, sink marks, or incomplete mold filling. Thus, the judicious investment of time and resources into meticulous mold design can elevate the quality of the over-molded component and enhance the overall efficiency of the over-molding process. It becomes a silent yet potent force, shaping the success of over-molding endeavors.
It's important to know about clearly of the process, which allows you to have over-molded parts manufacturing more easily. Here, we share our considerations from overmolding suppliers' perspectives:
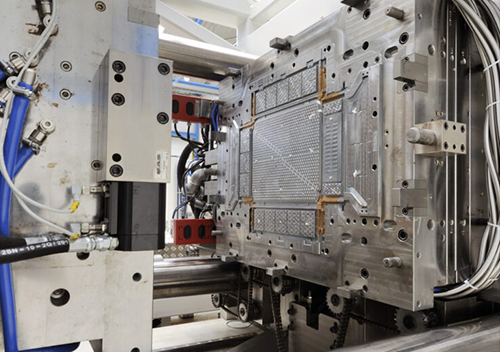
1. For hard plastic molding hard plastic
We need to confirm if these 2 materials are compatible and can adhere well. The thickness of the molded layer is suggested to be thicker than 0.8mm to avoid the short shot and reserve enough sealing areas on the mold to avoid the flash issue. We can take overmolding nylon for reference.
2. For soft plastic molding hard plastic.
Soft plastic, such as the overmolded parts, besides the same considerations as hard plastic over molding hard plastic, we also need to think about the TPE's thickness effects, hardness, and coefficient of friction, as all these will directly affect your part's performance. We can take Hogue overmolded grip and cable overmolding for reference.
3. Overmolding vs Insert Molding - Molding Plastic on Metal.
Molding plastic on metal is popular and wide in the industry, and with rapid manufacturing, both hard and soft plastics are available. Overmolding vs. insert molding? It usually depends on the molding areas and parts structure. We need to take full consideration of the metal part's structure. How can the molding material layer stick to metal firmly? How can the metal part locate in the mold?
4. Overmolding Surfaces in Rough Texture
When comparing to the smooth, glossy surfaces, rough textured surface can provide better bonding. 0.5 degrees draft for the bonding area is good for external surfaces.
5. The More Contacted Surfaces The Better Bonding
Increasing both ribs and gaps are good for bonding. For increased how much and where can be increased, it depends on the product's mechanical requirement
6. No Sharp Corner If Possible
As there are limited contact on sharp corner, the overmolding material is easy to peel-off. We suggest to have at least 0.5mm radius on the corner for bonding.
7. Set Undercuts for Better Bonding
Even though chemical bonding is critical, an undercut mechanical design can help the product being much more reliable. With an external force, with the help of undercut, the mechanical bonding will suffer much less external force, so that the over-molding would be more reliable.
8. Have a Even Wall at 1.5-2.5mm
Too thin will cause short shot or not sufficient soft-touch feeling, too thick will cause uneven shrinkage, flashes or unstable molding production. 1.5-2.5mm is good for over-molding.
Applications of Overmolding: Elevating Industries through Versatility
The multifaceted prowess of overmolding permeates a spectrum of industries, bestowing upon products an amalgamation of versatility and heightened functionality.
Automotive Industry
In the automotive sector, overmolding takes center stage, fashioning controls and handles with soft-touch grips, concurrently offering insulation for intricate wiring. Within the automotive realm, over-molding births components like seals, gaskets, and controls, where the soft-touch allure meets enhanced practicality.
Medical Industry
The medical landscape witnessed the ergonomic revolution brought about by over-molding, gracing surgical tools with comfortable handles, and encapsulating electronic components in medical devices. The medical tapestry showcases over-molded marvels, from surgical instruments donning ergonomic handles to medical devices encapsulating sophisticated electronics.
Consumer Industry
in the consumer electronics arena, over-molding crafts housings with tactile finesse ensures a comfortable grip while safeguarding delicate electronics from environmental influences. Smartphones, tablets, and wearable devices embrace over-molding, adorning their housings for an ergonomic grip and elevated comfort.
Instrument
The instrumental role of overmolding extends to power tools, wherein handles undergo over-molding for an augmented grip and heightened comfort, while sports enthusiasts encounter its impact in golf clubs and racquets featuring over-molded grips, elevating the arena of performance.
In these examples, overmolding transcends its role as a manufacturing process, emerging as the architect of innovation, reshaping products across diverse industries.
Overmolding vs. Insert Molding: A Quest for Superiority
· Exploring the Techniques
In plastic molding, the dynamic interplay between overmolding and insert molding unfolds, each technique weaving its distinct advantages into the fabric of manufacturing innovation. Overmolding is an artful process where a material envelops a preformed part and extends its prowess to bestow a soft-touch exterior or forge seamless bonds sans adhesives or fasteners. In the parallel realm, insert molding steps onto the stage, wrapping plastic around a preformed entity—often a metal insert—giving birth to a unified component.
· Overmolding vs. Insert Molding, How to Choose
The choice between overmolding and insert molding emerges as a nuanced deliberation. Should the pursuit be to infuse a gentle exterior into a robust plastic entity or seamlessly unite two parts without the crutch of adhesives, over-molding emerges as the artisan's choice. Conversely, if the aim is to cocoon a metal insert within a plastic embrace, the spotlight gracefully shifts to insert molding. The verdict, whether favoring over-molding or insert molding, aligns with the bespoke demands of each unique project, where precision and innovation coalesce in the quest for manufacturing excellence.
Exploring Prototyping Techniques: Over-Molding, Insert Molding, and 3D Printing
Prototyping stands as a pivotal phase within the product development journey. It serves as a testing ground for novel concepts and a platform to resolve uncharted design challenges. However, this crucial phase often comes with a hefty price tag and considerable time investments, particularly when relying on external sources for component production.
In response to these challenges, leading innovators across the globe are merging various manufacturing methods such as over-molding, insert molding and 3D printing.
At Google's Advanced Technology and Projects (ATAP) lab, designers managed to slash costs by over $100,000 and compress their testing period from three weeks to a mere three days. Their breakthrough was achieved through a fusion of 3D printing and insert molding. By opting for 3D-printed test parts, they circumvented the need for costly electronic components shipped from suppliers. This case is just one example of the myriad ways in which businesses strategically amalgamate 3D printing with other rapid manufacturing techniques.
Dame Products, a startup rooted in Brooklyn, focuses on crafting health and wellness-oriented innovations. Within their repertoire, they utilize silicone insert molding to encase internal hardware for customer beta prototypes. Their product line flaunts intricate ergonomic shapes enveloped in a layer of skin-safe silicone, boasting vibrant color schemes.
The engineering team at Dame Products churns out numerous insert and over-molded devices within a single day, employing a rotation system through three or four SLA-printed molds. While one prototype undergoes the curing process for its silicone rubber, the subsequent prototype is de-molded and readied for the next stage. Simultaneously, the finishing touches and cleaning of the de-molded prototypes take place in parallel. Upon the return of prototype hardware to the company, the beta device undergoes a bleaching process, shedding its thin silicone layer, enabling the internal hardware's reuse in crafting new beta prototypes.
Within the intricate domain of prototyping, the harmonious integration of over-molding, insert molding, and 3D printing unfolds a vast spectrum of possibilities. These methodologies, each endowed with distinct virtues, empower designers to meticulously craft prototypes endowed with heightened functionality and precision. Particularly noteworthy is the transformative impact of 3D printing, catalyzing expediting design iteration processes and ushering in a democratic era of innovation within the prototyping landscape.
TEAM Rapid - One of the Best Overmolding Suppliers in China
The overmolding cost at TEAM Rapid is affordable. Our advantages:
1. Overmolding Production1. Advanced injection molding equipment can achieve highly precise over-molded parts such as Hogue overmolded grip.
2. Molding parts with consistent quality guaranteed by instrumented molds.
3. Improved part functionality (i.e., creating an adjust-resistant seal or clear plastic window).
4. Low-volume production is available and cost-effective for mass production through robotics and automation.
5. Diversities over molding injection materials are available, which allows you to get the right properties parts.
6. Significant reduce the risk of assembly operations failure modes and save your cost by cutting down the high fall-out rates.
Looking for low-overmolding cost suppliers in China? To receive a quote or start a discussion about your project, don't hesitate to contact us at [email protected] today.
Frequently Asked Questions
What is Overmolding?(What is Plastic Overmolding?)
Overmolding is a process that involves combining multiple materials to create a single part. This process, which is usually performed in a mold, involves the insertion of a wire and a connector into a mold. The first material covered by this process is the substrate, while the other materials are used to cover the other components. The over-molded part can be either a rigid plastic component or an overlay layer of a TPU. There are two overmolded components: the insert molding technique and the multiple-shot method.
An over-molded cable is a type of full assembly consisting of a wire and a connector combined into one seamless part. The process begins by placing the cable assembly inside a mold. After the plastic material melts, it solidifies and conforms to the mold's shape. This then seals the junction point of the wire and the connector.
How does Overmolding Work?
In the manufacturing industry, overmolding is a widely used process. One of the most common types of this process is multiple-material molding. Multiple-material mold is also known as 2K or Two-Shot molding. This process involves creating a bond between over-molded parts and a substrate. The multiple material molding processes involve creating two sets of cavities, known as cavities 1 and 2. The first holds the substrate, while the other molds the over-molded component. This process is commonly used to produce various products, such as flexible components and industrial equipment. This technique has various advantages, such as superior part quality and low cycle time.
Multiple Material Molding Options:
Elastomer over Thermoplastic Substrate
Thermoplastic over Thermoplastic Substrate
Multiple Material Molding Steps:
Step 1: Mold the parts that need to be over-molded.
Step 2: Put the molded parts into cavity 2.
Step 3: The injected molten plastic is cooled, followed by the separation of the core and cavities.
Step 4: In this step, the mold is closed, and the molten plastic is injected into cavity 2.
Step 5: After cooling, the material, the part, is ejected from the injection mold.
What is Overmolding in Injection Molding?
Overmolding is one of the important parts of the injection molding process. In addition to creating a single part, overmolding involves combining two different materials. This process is usually performed in two shots. The first shot is usually made from more rigid plastic. The second shot, called the over mold, is made from a more flexible plastic-like material. Through overmolding, product designers can create functional and beautiful components by combining two different plastic materials.
What is Overmolding Process?
The materials can be very different in the overmolding process, which involves creating a single component from the combination of several materials. Understanding the various materials used in the overmolding process is very important. The two main categories of these are the substrate and the overmold.
substrate and overmold
The over-mold is molded onto a substrate, while the base material is the substrate. Depending on the end product and the manufacturer's creativity, there are typically two or more over-molded components.
What is the Difference between Insert Molding and Overmolding?
Overmolding and insert molding are structural differences. The former involves the creation of a base or substrate inside a mold, while the latter involves the addition of a layer to enclose it. The most common process in this mold is adding plastic components to a metal part, such as a screwdriver.
What Files to Send for Cable Overmolding?
We need the STEP or IGS format 3D files of your products. Our engineers will suggest the available proposals according to your design and demanded quantities. The vacuum casting process makes your over-molding prototypes or rapid tooling for over-molding small-volume prototypes.
What is Overmolding? How to Design It?
Mechanical Interlock
Overmolding follows the same principles as traditional injection molding processes but a few additional quirks in design:
1. Proper draft angles and uniform wall thickness with smooth transition lines maintained in both parts.
2. The wall thickness of over-molding areas should be equal to or less than that of the substrate below.
3. The overmolding materials should in lower melting temperature than the substrate.
4. Mechanical interlocks can be used to repair practical chemical bonding.
5. Texturing on the substrate part can help with adhesion.
Have no idea about insert molding vs. overmolding? Contact us for more design tips for your project today. Our engineer will tell you the differences between insert molding vs. overmolding and give you the best selection!