Vacuum casting, also referred to as urethane casting or polyurethane vacuum casting. It is a versatile method for producing high-quality prototypes and short fabrication runs of complicated plastic elements. Vacuum casting combines three-D printing and conventional casting strategies. With sophisticated facts, great floor finishes, and a wide variety of material homes by using which elements are allowed to be produced. This article aims to provide complete expertise on vacuum casting process, along with its system, benefits, dangers and often requested questions.
Table of Contents
Vacuum casting process:
The first step in the vacuum casting process is to create a master pattern, often done using CNC machining or 3D printing technology. After that, the primary paint is put into the casting box, and smooth moulds are created by pouring liquid silicone rubber on top of the paint. The mould is washed to obtain a rough imprint of the necessary portion, and the primary image is erased. After that, the mould is assembled again, and a two-dimensional polyurethane resin is poured into the cavity. Every mould is placed within an aeration chamber that releases air to ensure that the resin gets into all of the mould’s crevices and nooks. When the mould has finally dried, it is opened to reveal the finished portion.
Advantages of vacuum casting process:
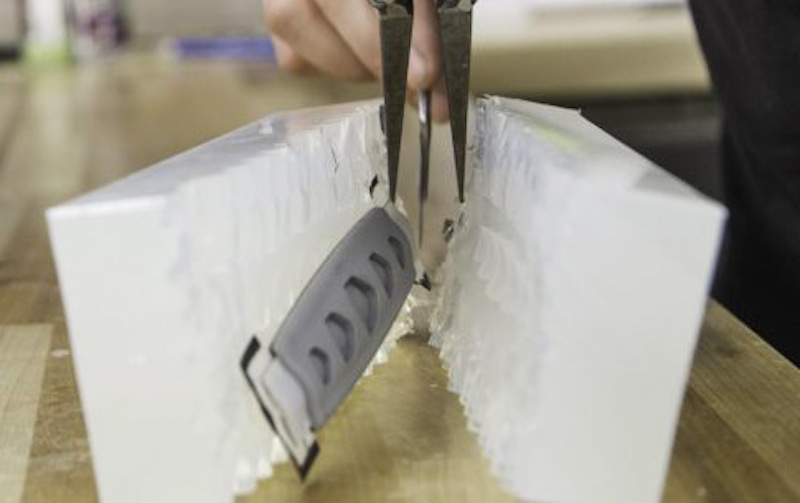
1. Economic prototype
For small company-run rapid prototyping or low volume manufacturing, vacuum casting process is a more affordable option than injection moulding. It makes it possible to produce working prototypes that have the same material qualities as the finished product. Enabling extensive testing and validation before the installation of pricey equipment.
2. Complex geometries and refined details
Thin walls, undercuts, and other delicate characteristics that would be challenging or costly to achieve with traditional manufacturing processes may all be replicated by vacuum casting. Because of this, it is the ideal choice for producing parts with complex geometries. Such as those found in automotive, medical, and consumer electronics components.
3. Extensive material selection
Accommodates a broad range of vacuum casting materials, such as polyurethane resins, with various surface treatments, colours, and mechanical characteristics. Because of its adaptability, components that are almost identical to the final product may be produced, guaranteeing accurate functional testing and aesthetic evaluation.
4. Faster turnaround time
Compared to traditional methods like injection moulding, vacuum casting process offers a faster turnaround time. The process eliminates the need for complex tools, allowing for more rapid iterations and design flexibility. This speed is beneficial for applications that require high-speed processing, such as consumer electronics and automotive prototypes.
Disadvantages of vacuum casting process:
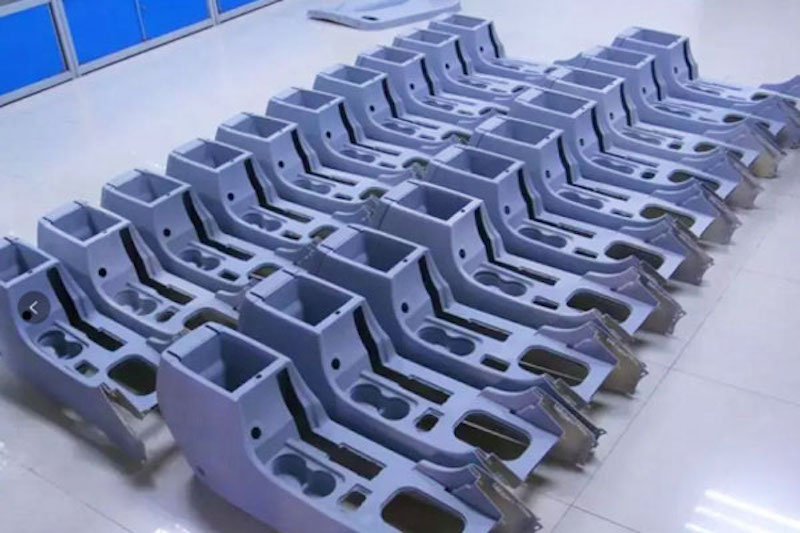
1. Limited Production Volume
Although vacuum casting process is suitable for small production runs, it is not efficient and cost-effective for large-scale fabrication. Injection moulding or other mass fabrication methods are better suited for high-volume production due to their fast cycle times and half-a low therefore cost.
2. Material limitations
Although vacuum casting supports a vast range of programs. It can now not be appropriate for a few packages that require unique substances, along with excessive thermal resistance or excessive strength. In such instances, alternative manufacturing methods such as injection moulding or CNC machining can be extra suitable.
3. Long lead time for complex parts
Parts with complex geometry or complex materials may require additional time to mould and assemble. The hardness of the mould and the method of curing can extend the overall use time and should be considered when designing the mould.
4. Modifications that alter surface properties
Although vacuum casting process generally produces high-quality finishes, factors such as mould damage, temperature fluctuations, and material differences may vary slightly between parts.
Questions and Answers:
Q: Can vacuum casting produce parts with transparent material?
A: Yes, vacuum casting can produce parts with soft materials using a specific polyurethane resin formulated for visual clarity. These resins are designed to maintain excellent transparency, providing visible results. This feature is especially helpful in fields like consumer electronics, lighting, and optics. Where using transparent components is frequently necessary for practical or aesthetic reasons.
Q: What is the duration required to finish vacuum casting?
Several variables can affect how long the vacuum casting process takes to finish. These variables include the part’s hardness, the number of moulds required to achieve the necessary volume, and the resin’s chosen cure time. The duration of the vacuum casting process typically ranges from several hours to many days. Complex parts with complex details may require additional time for moulding and assembly, while resin curing time may also affect the overall production schedule. It is important to consider these factors during fabrication planning the vacuum casting tasks to ensure realistic expectations and efficient scheduling.
Q: Can vacuum casting recreate solid interiors?
A: Yes, vacuum casting can accurately reproduce the complex internal structures of the parts. This is accomplished through the use of removable tissue and advanced moulding techniques. With the addition of removable cores, moulds can form complex internal geometries such as hollow structures, lattice layouts, fluid channels, and so on.
Q: What are the most significant parts that can be vacuum cast?
A: The size of parts that can be vacuum cast depends on the size of the casting chamber available and the capacity of the vacuum equipment used. Although there is no set limit, vacuum casting is generally suitable for sections up to about 1 meter inside length. The exact measurements that can be obtained may vary depending on the equipment and resources available. It is essential to consult with the vacuum casting service provider or manufacturer to determine the maximum size limit for a particular application. For more significant parts, other manufacturing processes, such as injection moulding or further bulk processing, may be more appropriate.
Conclusion
Vacuum casting is an effective technique that has several advantages for creating specimens and small objects. Many different types of enterprises find it attractive because of its ability to handle and build complex pieces from a wide range of materials. Although the process has limitations, including long lead times and a restricted manufacturing capacity. Vacuum casting offers a versatile and cost-effective solution for complex products. Contact TEAM Rapid to request a free quote now!