Plastic injection mold and plastic molding stand as a pivotal cornerstone within modern manufacturing, profoundly influencing the contours of numerous everyday items. This article takes a comprehensive plunge into the inner workings of this intriguing procedure. We’ll navigate through its mechanics, the diverse array of molds employed, the spectrum of materials harnessed, and the nuanced landscape of its merits and demerits. Prepare to be immersed in the realm of plastic injection molding—a journey that promises insightful enlightenment.
Table of Contents
- 1 Revealing the Mastery of Plastic Injection Mold – Revolutionizing Production and Beyond
- 2 Traversing the Stages of Plastic Injection Molding
- 3 Mastering Plastic Injection Mold Types in Molding
- 4 Navigating the Advantages and Drawbacks of Plastic Injection Molding
- 5 Conclusion of plastic injection mold and molding
Revealing the Mastery of Plastic Injection Mold – Revolutionizing Production and Beyond
Plastic injection molding emerges at the forefront of contemporary manufacturing, redefining the crafting of plastic components. This transformative methodology finds its origins in the innovative spirit of John Wesley Hyatt during the late 19th century, a pursuit ignited by the quest for an ivory billiard ball alternative.
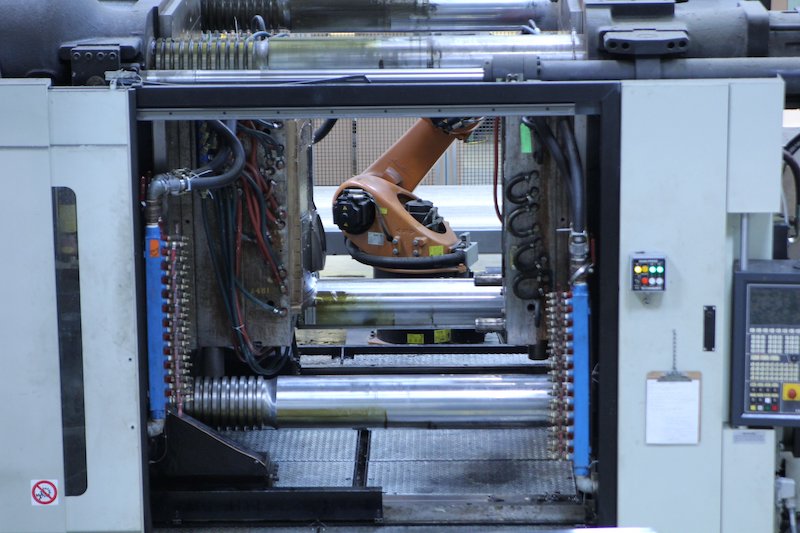
Harmonizing Creation
In the core of plastic injection molding lies the graceful interplay of heat and pressure. Its inception involves the heating of plastic granules, transforming them into a molten state brimming with potential. The subsequent enchantment unfolds as this liquefied amalgam is deftly coerced into a metal mold bearing the contours of the desired end piece. The union of form and fluidity transpires under the watchful eye of elevated pressure.
Convergence of Enchantment and Reality
The mold’s role as a cocoon of metamorphosis becomes evident as the molten essence cools and solidifies within. The veil rises on the theater of creation when the mold is ultimately unveiled, exposing the emergence of a resolute plastic masterpiece.
Transcending Mere Production
The appeal of plastic injection molding resides in its capacity to orchestrate swift, precision-driven mass production at a mere fraction of conventional expenses. Its reach extends across a spectrum of industries, whether the automotive sphere, the intricate domain of medical apparatus, or the everyday fabric of consumer goods. This adaptable technique has indelibly etched its place as the pulse of modern manufacturing — an artistry that shapes our very world.
Traversing the Stages of Plastic Injection Molding
From Raw Material to Transformed Artifact
The plastic injection molding process intricately weaves raw plastic into refined objects that epitomize contemporary existence. An orchestrated journey unfolds, ushering plastic through precise phases to achieve its final form. Let’s traverse this process step by step.
Material Preparation
The inception lies in the meticulous selection of plastic resins, each tailored to meet the exact specifications of the end product. These granulated resins are methodically measured and introduced into the feeding system.
Melting and Injection
Enveloped by heat, the granules transmute into a molten state, a fluid that carries the promise of transformation. Under elevated pressure, this molten essence finds its way into an intricately fashioned metal mold.
Mold Filling
The mold’s core and cavity act as a canvas for this liquid plastic symphony. With precision reminiscent of a maestro’s baton, the molten material fills the mold, capturing every nuanced curve and dimension.
Cooling and Solidification
As the molten plastic embraces the mold’s contours, the orchestration shifts to a cooling cadence. The once-fluid material solidifies, encapsulating intricate details within its solid embrace.
Ejection and Unveiling
With finesse, the mold parts reveal the emergence of a formed plastic entity. Ejector pins delicately usher the new product out of its molding abode, showcasing the seamless marriage of design and manufacturing prowess.
Post-Processing
In this stage, the newly formed creation may undergo refining touches. Trimming surplus material and refining edges ensure the object emerges with immaculate contours, poised for its designated function.
Quality Assurance
Stringent quality assessments ensue, validating that each creation aligns with the highest standards of precision. Imperfections, if any, are meticulously addressed, safeguarding that only excellence endures.
Culmination
As the final product emerges, the journey culminates, embodying the intricate fusion of plastic, heat, and pressure. This meticulously crafted artifact stands as a testament to the technical finesse and artistry encapsulated within the realm of plastic injection molding.
Mastering Plastic Injection Mold Types in Molding
In the mesmerizing realm of injection molding, the pivotal role of mold design and type cannot be overstated. These sculptors of form hold the key to the very essence of the final product. Let’s delve into the world of molds, unveiling their variations and significance.
Two-Plate plastic injection Molds: Crafting Simplicity
In the grand tapestry of molds and rapid tooling, the two-plate mold stands as the humble protagonist. Simplicity defines its essence, with one cavity plate and one core plate in harmony. As plastic flows into the cavity, the mold’s curtain rises, revealing the masterpiece. The ejected creation takes its final bow from the core side.
Three-Plate plastic injection Molds: Sculpting Complexity
For creations that demand a touch of complexity, the three-plate mold emerges as the virtuoso. An extra plate introduces newfound capabilities, enabling intricate shapes to materialize. The runner system finds its stage, enhancing the product’s aesthetics and quality in the grand performance of molding.
Hot Runner Molds: Igniting Innovation
Within the ensemble of molds, the hot runner mold takes the spotlight. With a heated runner system, plastic remains in its molten allure, eliminating the need for solid runners. This innovation curtails waste, orchestrates swifter cycle times, and sets the stage for sustainable rapid manufacturing.
Cold Runner Molds: A Different Symphony
In contrast, the cold runner mold embraces a cooling system to solidify plastic within the runner system. Simplified in nature, these molds are cost-effective but may produce more waste compared to their heated counterparts.
Unveiling the Yin and Yang of Manufacturing
Just as life weaves intricate patterns of light and shadow, plastic injection molding, too, dances between its own set of merits and shortcomings. Let’s embark on a journey to explore the delicate balance that defines this manufacturing marvel.
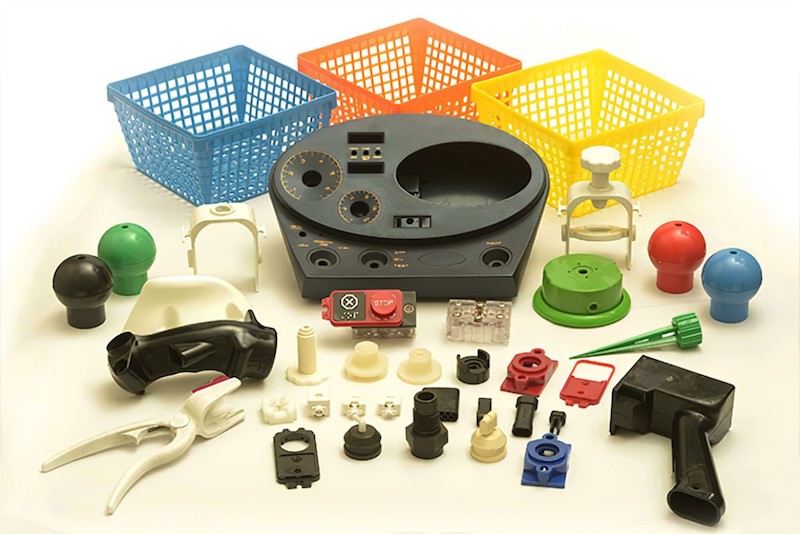
Advantages
1. Efficiency
Like a masterful maestro, plastic injection molding orchestrates high-speed production, generating copious identical plastic parts in a remarkably short span.
2. Precision
In the grand canvas of manufacturing, this technique wields a fine brush of precision, crafting complex parts with intricate detail that suit a diverse spectrum of applications.
3. Labor Efficiency
With automation as its muse, the process gracefully sidesteps hefty labor costs, celebrating the realm of efficiency.
4. Minimal Waste
A virtuoso in conservation, plastic injection molding curtails waste production, often reincarnating excess material for future creations.
Disadvantages
1. Initial Hurdles
Like the commencement of any grand journey, the design and production of molds can present a financial mountain, especially for intricate designs seeking physical form.
2. Material Limitations
The palette of plastics is vast, yet not all shades harmonize with the injection molding symphony, posing limitations in material selection.
3. Design Boundaries
Amidst the possibilities, there exists a realm of constraints. Maintaining uniform wall thickness to avert defects is a delicate art in itself.
Conclusion of plastic injection mold and molding
In the intricate tapestry of modern manufacturing, plastic injection molding stands tall. Its precision, efficiency, and adaptability redefine industries, shaping our world with innovation and excellence.
Besides from injection molding, TEAM Rapid also offers 3d printing services, CNC machining services, die casting etc to meet your projects needs. Contact us today to request a free quote now!