Surface polish entails polishing the surface area of a material workpiece or final product to make it smoother and more polished. What is polishing? This process uses primary techniques involving abrasive components, chemicals, or electrolytic processes. Each polishing technique will have its own set of equipment and tools.
Table of Contents
What is Polishing – Surface Finishing Options
Polish is an essential post processing you can apply after performing primary manufacturing operations. You can use differing methods for your components or final products according to the project goals. Here are the primary options to apply surface finish for your final products:
Chemical
In chemical-based surface finish, you can apply a surface finish on the material workpiece by immersing the material into a specific chemical composition. Varying chemical compositions can offer distinctive surface polish features, which will depend on the material type. It will result in a smooth finish without any microscopic particles staying on the surface area of the material. You can also eliminate burrs when using the chemical polish solution.
Mechanical
The mechanical polishing method will use physical contact on the material surface with some polishing media or abrasive as the primary polish tool. You can use glass beads, sandpapers, or specialized sponges to polish the surface area of the material. This polishing technique can help you remove various scratches and imperfect surface features on the material with a high level of effectiveness. The polish result provides accuracy and precision, which might require some skilled experts to work on.
Electrolytic
The electrolytic polish method is a step ahead of the chemical-based polishing. Aside from using a chemical solution, this method requires you to immerse the material workpiece into the electrolytic bath chamber for the polishing process to start. The electrolytic ions will work on removing the excess layers of the material surface and polish them in the process. The resulting surface polish will be frictionless and exceptionally smooth when you look at or touch it.
These are the surface finishing options you can pick when upgrading the look and feel of your final products. In each option, you can find differing techniques for polish the surface area of the material workpiece, which will depend on various factors. It’s best to pick the one that matches your design preferences and budget.
What is Polishing – How Surface Polishing Works
Surface polish is a straightforward process. It contains the steps of preparing the material, polishing it, and rinsing it. The length of the process will depend on the surface finish technique you choose. Here’s how it works:
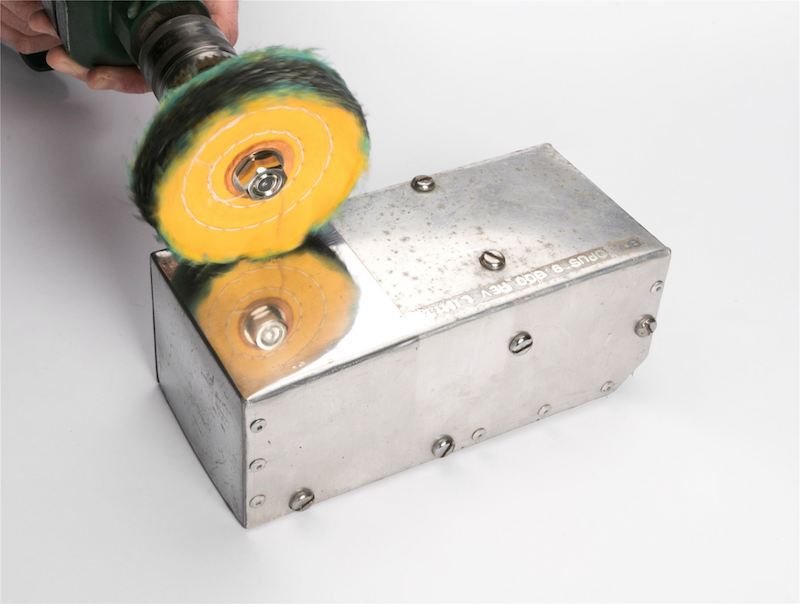
Choose the polishing method
Each material type has an ideal polishing method you can use. However, it doesn’t mean you can only use one specific surface finish method for each material. Varying options are available to polish the material surface and give you specific polish features. It’s essential to pick the method suitable for your final products and project goals.
What is Polishing – Preparation is Important
It is the first step before you can proceed with your chosen surface polishing technique. There are many ways to prepare the material or component for surface finishing, such as roughing the surface, rubbing sandpaper, and more. The goal is to ensure the object is ready for the primary finishing technique. It will also ensure that the object will benefit from the chosen surface polish method.
Surface polishing process
Next, you will go through the surface polish process you have chosen before. You must prepare the equipment with all the extra tools and materials. You can start the polishing operation once you are ready. The surface polishing process will proceed as long as necessary.
Unloading
After finishing the surface polish operation, you must unload the material or final product from the equipment. Then, you will need to place the polished material where you can let it sit for a while. It will allow the material to absorb the components from the polishing operation onto the surface area.
Rinse
Next, the rinsing process will commence, where you clean all the excess chemicals from the surface polishing operation. Most rinsing processes will require plain water for you to perform it. However, sometimes, you might need specific rinsing components or materials for the best result.
Quality check
It is the last step before you can send the polished final products to subsequent manufacturing processes, which include assembly or packaging. This process ensures that your polished materials or components will meet the quality standards you have set for your products(especially for the craft such as custom medal) . Quality checking will also allow you to fix any issues in surface finish before sending the final products to your clients.
These are the steps on how the surface polishing operation will work on your manufacturing production. The surface polishing technique will give your final products the best quality before you package them for sale. Surface polished components will also be more fitting for further assembly processes.
What is Polishing – Practical Tips
Following the procedure is your best bet to get the highest-quality result for the polished components. A little mistake can sometimes take you a lot of time to fix. Here are some practical tips to follow during the surface polishing procedure:
Thorough cleaning
You need to clean the component’s surface before applying any procedure. Dirt and contaminants might interfere with the surface polishing operation, resulting in uneven material polish distribution or even massive polishing failure. Thorough cleaning is essential to ensure the best result in your polishing operation.
Distribute pressure evenly
Surface polishing requires you to distribute pressure evenly across the material workpiece to allow the even distribution of abrasive polish. Uneven pressures will only give a poor result on the material surface, as the polish won’t spread across all surface areas. Keep the pressure steady during processing to get an even polish distribution across the material surface.
Don’t overheat
Overheating can cause problems with the abrasive or polish material. It can melt the abrasive, which can affect the result. It might also damage the surface material of the final products during the procedure.
Practice safety first
Surface processing procedures will use the equipment you need to handle with care. In electrolysis, you must use high-voltage equipment to run the polishing procedure. So, prioritize your safety when you run these techniques.
Take it step by step
You cannot work with the surface finishing equipment and expect everything to finish in one big step. Surface polishing requires gentle care and patience when you apply the abrasive components on the material surface. So, take it step by step and let the process unfold gradually.
Test abrasive before use
Testing the abrasive compound before you apply it to the material surface can help prevent any issues during the polishing procedure. First, you must test the abrasive on a small area around the surface before applying it to all surface areas. It is to prevent any unwanted issues during processing, such as incompatibility with the material.
Follow these tips to get the best result in your surface finishing operation. Always check how you follow the surface polishing procedure to avoid any problems that can render your surface finishing process useless. It’s best to stay on course with your surface finishing procedure and avoid deviating from the polishing best practices.
What is Polishing – Common Issues
Surface polish can give perfection to the material or component you work on. However, some issues might disrupt the overall quality of your surface finish. Keep in mind of these issues:
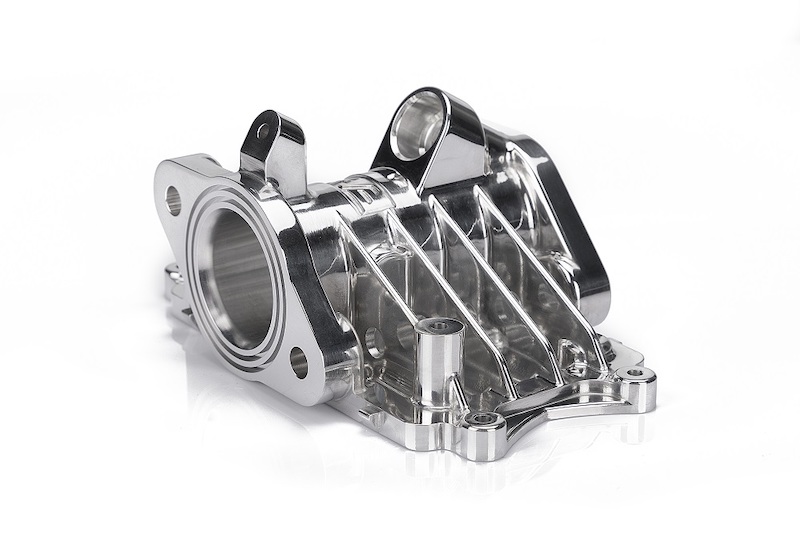
Imperfections
Polished surface imperfections can manifest in the form of burrs, which can disturb the component’s performance during use. Incorrect surface processing methods can cause burring on the material surface area, which you must fix later. Deburring is essential to remove any burring imperfections on the surface area, which you can complete using electrolytic polishing.
What is Polishing – Stains
Stains can also appear on the material surface after you complete the procedure. The stains often come out when you use chemical-based polishing on an unsuitable surface area. Again, electrolytic polishing will help clean the stains from the material surface.
Material incompatibility
Another common problem you can experience during the surface processing operation is material incompatibility. Some materials might not be compatible with the abrasive or chemical components you use for surface polish. It can lead to issues related to the look and feel of the surface area after you polish it with incompatible abrasive or chemical components.
Uneven polish
Uneven polish can happen when you apply uneven pressure on the material surface during processing. It can happen on abrasive-type polishing where you need to apply pressure on the surface material to apply the polish. Put consistent pressure on the surface material during polishing to prevent this issue.
Always be mindful of potential issues you can experience during the polish process. Perform the necessary steps to prevent those issues. It will ensure the best quality for your polished surface.
Conclusion
Rapid manufacturing often produces components or final products with rough surface areas. Surface polish provides a post processing technique that can help eliminate the roughness on your product’s surface and make it look more polished. Pick the polish technique with the best compatibility for your material type to ensure the best result in your surface polishing operation. TEAM Rapid offers rapid prototyping, CNC machining, injection molding, and die casting for your project needs. We can apply polish on your parts as you want, contact our team today to request a free quote now!