In the realm of manufacturing wizardry, injection moulding takes the spotlight by conjuring parts from molten materials within moulds. Enter the protagonist: the injection rate. This dynamic force dictates the material’s dance into the mould, ultimately casting the spell that shapes product quality. Join us on a journey as we unravel the artistry behind injection rate and their paramount role in sculpting manufacturing excellence.
Table of Contents
- 1 Exploring Injection Molding and injection rate: A Precision Manufacturing Process
- 2 Unveiling the Significance of Injection Rate in Injection Molding
- 3 Navigating Injection Rate Dynamics: Factors and Fine-tuning
- 4 Strategies for Injection Rate Optimization in Injection Molding
- 5 Benefits on Display
- 6 Conclusion of injection rate
Exploring Injection Molding and injection rate: A Precision Manufacturing Process
Injection moulding stands as a cornerstone of modern manufacturing, seamlessly bridging the gap between creativity and precision. With the ability to yield a diverse spectrum of parts and products, from intricate components to complex structures, this process is a true testament to engineering excellence.
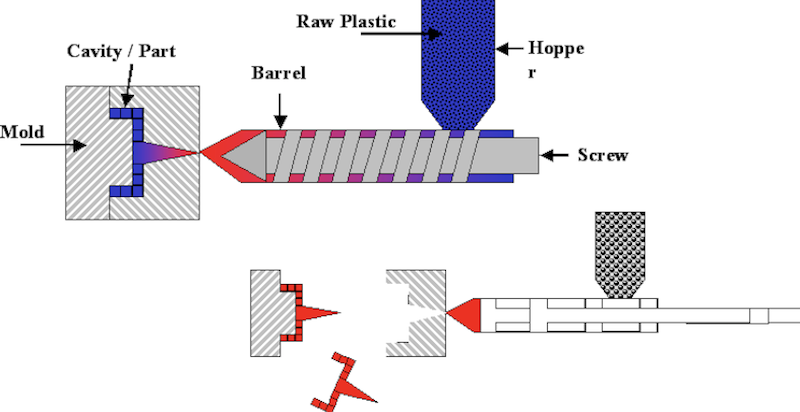
The Intricacies of the Process
The journey commences with the transformation of raw material, often plastic, from solid to molten state. This molten material is then injected into a meticulously crafted mould cavity. The subsequent cooling and solidification bring forth the desired shape, rendering each product a manifestation of meticulous design and execution.
Stages that Shape Perfection
Clamping
The process begins with the closure and clamping of the mould, ensuring a secure environment for the upcoming transformation.
Injection
The molten material takes centre stage, flowing into the mould cavity with calculated precision, guided by controlled pressure and rate.
Cooling
As the molten material cools within the mould, it adopts the mould’s contours, shaping itself into the intended form.
Ejection
The final act involves the graceful release of the solidified product from the mould/rapid tooling, concluding the process with finesse.
The Symphony of Quality
The synchronization of these stages orchestrates the quality of the final product. Variables such as material temperature, injection rate, and cooling duration conduct this symphony of creation.
A Cross-Industry Virtuoso
Injection moulding’s virtuosity extends across industries, delivering excellence in automotive engineering, medical device fabrication, consumer goods production, and the crafting of intricate electronic components.
Curtains Close on Excellence
In the denouement, injection moulding is more than a process; it’s an embodiment of precision and expertise. Understanding and optimizing each stage guarantees products that align seamlessly with specifications, minimizing waste and maximizing efficiency. As the curtains draw to a close on this performance, the legacy of injection moulding remains—an artistry of engineering that shapes the world around us.
Unveiling the Significance of Injection Rate in Injection Molding
At the heart of the intricate dance that is injection moulding lies a pivotal player – the injection rate. This critical parameter holds the reins of control over the process, dictating the tempo at which molten material enters the mould cavity and shapes the destiny of the final product.
Understanding the Injection Rate
Consider it the conductor’s baton in this rapid manufacturing symphony. The injection rate stands as a numerical representation of the material’s ingress speed into the mould. It’s a measurement that transcends mere numbers, wielding a profound influence over the quality and characteristics of the result.
Shaping Quality Through injection rate Control
In the realm of plastic moulding, precision is paramount. An optimized injection rate can unlock a multitude of benefits. Swift injections can translate to reduced cycle times, boosting efficiency without compromising on quality. The material flows harmoniously, ensuring the mould cavity is evenly filled, minimizing the risk of imperfections like sink marks or voids.
However, the rhythm must be carefully conducted. Too swift a pace can lead to challenges. Excessive shear stress might rear its head, impairing the material’s structural integrity. It could potentially induce wear and tear on the mould, chipping away at its longevity.
Striking the Balance
The key lies in calibration. A judicious injection rate strikes a chord between efficiency and excellence. Modern tools, such as computer simulations and real-time monitoring, enable manufacturers to fine-tune this parameter. This orchestration ensures that the material’s journey aligns seamlessly with each part’s intricate demands and the material’s unique attributes.
The Culmination of Craftsmanship
As the curtain falls on the stage of injection moulding, the spotlight remains on the injection rate. It is not just a numerical value but rather the architect of precision. Through its guidance, the molten material gracefully assumes its role, manifesting into a product that embodies the synergy between engineering, artistry, and meticulous calculation.
In the captivating world of injection moulding, the injection rate’s tempo isn’t a solo performance – it’s a symphony composed of various factors that influence its rhythm.
Material Moves
Material properties kick off the overture. Viscosity and melting temperature dance together to influence the injection rate’s pace. High-viscosity materials may require a gentler injection rate, ensuring they elegantly flow and fill the mould’s embrace.
Mould’s Influence
Next, the mould takes the stage. Its dimensions, complexity, and contours can dictate the injection rate’s melody. A grand and intricate mould might call for a more spirited injection to guarantee an even and complete fill.
Machine’s Harmonics
The machine settings chime in with their unique notes. Barrel temperature and pressure settings play a role in shaping the injection rate’s cadence. Tuning these settings orchestrates the ideal injection rate for the material and mould at hand.
Environmental Orchestra
The environment lends its voice to the harmony. Ambient temperature and humidity, like atmospheric musicians, join in. A warmer setting, for instance, can encourage the material to glide more smoothly, harmonizing with a quicker injection rate.
Fine-tuning the Ensemble
This intricate composition can be guided with precision:
Mastering Material
Experimentation with materials of varying viscosity and melting temperatures reveals their preferred tempo.
Moulding Marvels
Meticulous mould design strikes a balance between complexity and injection rate, ensuring a seamless performance.
Machine Maestros
Calibrating machine settings finely tune the injection rate, matching the material’s flow dynamics.
Environmental Choreography
Adapting to environmental conditions ensures the injection rate dances smoothly, irrespective of the surroundings.
Striking the Perfect Chord
In this symphony of manufacturing, the injection rate harmonizes with multiple factors. Each element can be fine-tuned and adjusted to attain a crescendo of efficiency and quality, creating products that resonate with perfection.
Strategies for Injection Rate Optimization in Injection Molding
Efficiency and excellence converge in the realm of injection moulding, where optimizing the injection rate holds paramount importance. Delving into this practice involves a meticulous approach driven by several strategies and techniques:
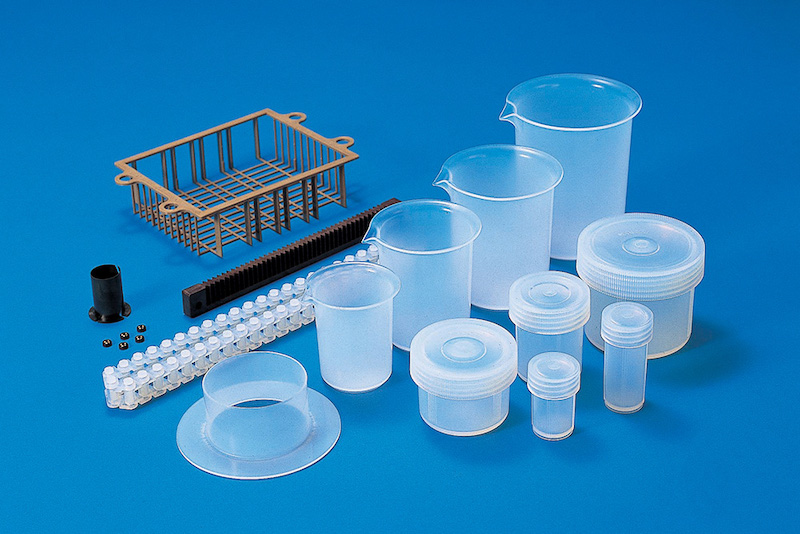
Computerized Precision
The implementation of advanced computer simulation software emerges as a pivotal strategy. It empowers manufacturers to model the injection moulding process digitally, enabling the testing of diverse injection rates. Through this virtual experimentation, the optimal injection rate for specific materials and parts can be accurately determined.
Real-time Vigilance
The orchestration extends to real-time monitoring. Manufacturers, equipped with the ability to observe the injection process in action, can make dynamic adjustments to maintain the injection rate within the desired range. This on-the-fly calibration ensures consistency and precision.
Insights from the Past
Leveraging historical data takes the spotlight as another strategy. The analysis of past injection moulding endeavours unveils trends and patterns. This invaluable information empowers manufacturers to fine-tune injection rates, crafting a pathway to enhanced efficiency.
Benefits on Display
Optimized injection rates reap a rich harvest of advantages. Cycle times shorten, part quality attains new heights, and waste is curtailed. The culmination is a harmonious symphony of efficiency and cost-effectiveness. In the intricate tapestry of injection moulding, the optimization of injection rates serves as a linchpin in achieving superlative outcomes.
Conclusion of injection rate
In the landscape of injection moulding, mastering the understanding and regulation of the injection rate emerges as a pivotal factor. This mastery underpins the creation of products characterized by precision, efficiency, and exceptional quality.
Besides from injection molding, TEAM Rapid also offers rapid prototyping services, CNC machining services, and die casting to meet your projects needs. Contact our team today to request a free quote now!