Within the expansive realm of manufacturing, injection molding machine emerge as pivotal players, particularly in shaping plastic parts. The crux of their prowess lies in the meticulous calibration of parameters—an art that dictates the very essence of product excellence. This discourse embarks on a journey to illuminate the crucial role of these adjustments and offers a comprehensive guide to mastering their intricacies.
Table of Contents
- 1 Unveiling the Core: Injection Molding Machine and Their Dynamics
- 2 Fine-Tuning Excellence: Unveiling Vital Adjustments in Injection Molding Machine
- 3 Navigating Precision: A Step-by-Step Guide to Parameter Adjustment on injection molding machine
- 4 Precision in Practice: Notes to Remember
- 5 Fine-Tuning Precision: Unveiling the Effects of Parameter Adjustment on injection molding machine
- 6 Conclusion of parameters in injection molding machine
Unveiling the Core: Injection Molding Machine and Their Dynamics
In the intricate weave of plastic rapid manufacturing, injection molding machines stand as maestros of creation. These wonders are reminiscent of artisans, melting plastic granules into fluidity and imbuing molds with meticulous precision, driven by formidable pressure. This symphony of processes births shapes spanning the spectrum from graceful simplicity to intricate sophistication, tailored to precise demands.
The Dance of Creation: Comprehending the Machine’s Odyssey
An injection molding machine’s odyssey unfolds through stages echoing the ascent of a masterpiece. The process initiates as plastic granules settle within a hopper, poised for metamorphosis. From here, a journey through the heating cylinder follows, where granules transform into liquid gold. This molten plastic embarks on its grand performance, surging into the mold through a nozzle, propelled by a symphony of high pressure.
As the mold/rapid tooling becomes a canvas for plastic verse, cooling solidifies the form, crystallizing molten aspirations into tangible reality. At last, the curtain rises as the mold unfurls, revealing the emergence of a finished product nurtured by the machine’s expertise.
Parameters: The Palette of Precision
Underlying this spectacle lies the might of parameter adjustment, a domain where art intertwines with science. Nudging these levers has the power to metamorphose outcomes at every crossroads. The caliber of the creation, the efficiency of performance, and the machine’s very vitality all waltz to the cadence of these adjustments.
A profound mastery of these machines and their parameter intricacies is indispensable for all embarking upon the terrain of plastic manufacturing. The subtleties of refining parameters can mold the trajectory of products, amplify operational finesse, and extend the machine’s longevity.
Fine-Tuning Excellence: Unveiling Vital Adjustments in Injection Molding Machine
Within the intricate domain of injection molding, the potential to craft excellence is wielded through the delicate calibration of essential parameters. These nuanced adjustments, reminiscent of a conductor’s baton, orchestrate the symphony that shapes molten plastic into meticulously crafted products. Let’s delve into the realm of these pivotal adjustments, which hold the key to steering product quality.
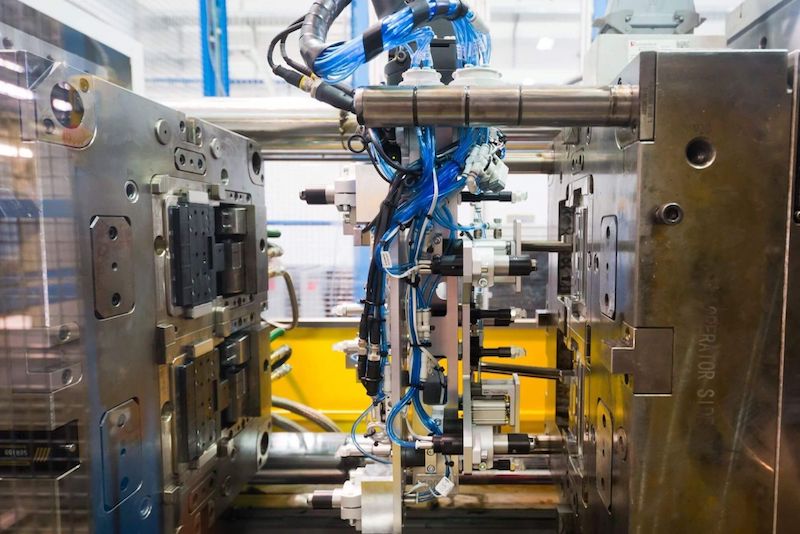
Precision Sculpting: Revealing the Core Parameters in injection molding machine
Injection Pressure
Analogous to a controlled force, injection pressure governs the graceful filling of the mold’s contours. The fine-tuning of this parameter holds the potential to define the intricacies of the final product’s form.
Injection Speed
Like the tempo of a masterful composition, injection speed dictates the fluidity of plastic molding flow. A gradual pace ensures uniformity, while a brisk tempo can expedite the molding process without sacrificing precision.
Mold Temperature
Echoing an artist’s brushstroke, mold temperature imparts texture to the plastic canvas. Elevating the temperature results in a refined surface finish, whereas a cooler setting accelerates solidification.
Cooling Time
The virtue of patience lies in cooling time. Allowing the plastic to solidify gracefully before ejection influences the structural integrity of the end product, a temporal interlude that shapes the outcome.
Back Pressure
An understated influencer, back pressure imparts character. The judicious application of pressure during injection influences the final product’s density and aesthetic appeal, an unassuming yet impactful touch.
True mastery resides in comprehending these parameters and their intricate interplay. A harmonious fusion of adjustments weaves a narrative unique to diverse plastic compositions and mold designs. As the manufacturing landscape continues to evolve, the mastery of these adjustments remains a guiding beacon, molding not merely products, but also shaping the trajectory of the future.
In the sphere of injection molding machinery, altering the parameters resembles the orchestration of a finely calibrated ensemble. Every adjustment possesses the capability to metamorphose the final symphony of product quality. Presented here is a comprehensive guide, unveiling the sequential actions for the modification of each pivotal parameter:
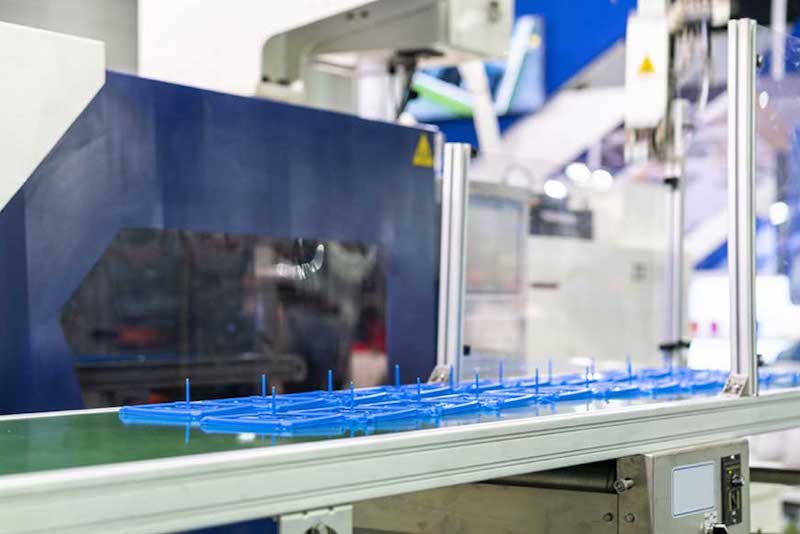
Injection Pressure: Balancing Force and Finesse
• Locate the pressure configuration within the machine’s control panel.
• Incrementally modify the numerical value, while considering that heightened pressure bolsters mold filling. Yet, exercise caution against bestowing undue stress upon the machinery and mold.
Injection Speed: Tempo Control for Precision
• Delve into the control panel to meticulously refine the injection speed setting.
• Slower speeds foster uniform filling, whereas swifter speeds expedite the procedure at the potential expense of uniformity and material integrity.
Mold Temperature: Crafting Textures with Temperature
• Direct your attention to the dedicated temperature controller, assigned to mold temperature.
• Adjust the designated value to govern the warmth of the mold. Bear in mind, that elevated temperatures engender smoother surface finishes, whereas cooler temperatures hasten the cooling process.
Cooling Time: The Grace of Cooling
• Locate the parameter denoting cooling time on the control panel.
• Elongate or truncate this temporal interval to influence the duration during which the plastic material consolidates before its ejection from the mold.
• Effectuate the manipulation of back pressure via the control panel.
• Elevating this pressure augments product density and aesthetic attributes. However, this elevation necessitates a balancing act to circumvent exerting undue strain upon the machinery.
Precision in Practice: Notes to Remember
Each adjustment mirrors the creation of a chord; their harmonization is the crux. Initiate changes with gradual increments, and closely observe the consequent impact on product quality. Maintain thorough documentation detailing the outcomes of each modification, decoding their effects and forging the path for refined tuning. As you embark upon the exploration of parameter mastery, bear in mind that the amalgamation of art and science unfolds with each adjustment, guiding you toward the crescendo of manufacturing excellence.
Fine-Tuning Precision: Unveiling the Effects of Parameter Adjustment on injection molding machine
In the realm of injection molding machines, the meticulous calibration of parameters exerts a profound influence on the ultimate product. Each adjustment, comparable to a stroke on an artist’s canvas, leaves an indelible mark on the final creation. Let’s delve into the intricate effects of these adjustments, unraveling a tapestry that shapes the fate of the end product.
Precision Engineering: Unraveling the Implications
1. Elevating pressure ensures comprehensive mold filling, resulting in a precise form. However, excessive pressure can introduce stress marks or deformations in the end product.
2. A measured injection speed attains uniform filling, curbing defects like short shots or flashes. Conversely, elevated speeds trim cycle time, potentially introducing irregularities or material wear.
3. Heightened mold temperature yields a polished surface finish and nurtures smoother plastic flow. Cooler temperatures expedite cooling, though they might yield coarser surfaces or induce warping.
4. Extending cooling time reinforces the product’s structural integrity, albeit prolonging the overall cycle. A truncated cooling duration accelerates production, albeit with the trade-off of potential warping or shrinkage.
5. Increased back pressure elevates product density and enhances visual appeal, yet it bears the risk of straining the machine and lengthening cycles.
The Balancing Act: Forging the Ultimate Product
Each parameter adjustment reverberates distinctively, contributing to the intricate fabric of the final result. Striking an equilibrium amidst these adjustments encapsulates the essence of sculpting superior products. Proficiency in this orchestration not only optimizes product quality and operational efficiency but also safeguards the machine’s endurance. Amidst this dynamic interplay between science and artistry, manufacturers wield the potential to sculpt excellence in every molded creation.
Conclusion of parameters in injection molding machine
Within the realm of injection molding, the process of parameter adjustment assumes the role of a conductor, orchestrating the intricacies of product creation. Each adjustment resonates with a spectrum of effects, spanning from structural integrity to aesthetic finesse. The synchronization achieved through meticulous parameter calibration underscores the foundational importance of this expertise, underscoring its pivotal role in shaping manufacturing excellence.
Besides from injection molding, TEAM Rapid also offers rapid prototyping, CNC machining, and die casting to meet your needs. Contact our team today to request a free quote now!