Can you use silicone rubber materials in your injection moulding process? The answer is yes. You can use silicone rubbers in your injection molding, with a smoother, faster, and cheaper process than the regular injection molding operations. With the many benefits of silicone rubbers, you can perform the silicone rubber molding process with better adjustability and customizability.
The high tensile strength and inert quality of silicone rubbers make it easier to create stretchable products that retain their basic shape. Let’s dive deeper into the applications and benefits of silicone rubber molding.
Table of Contents
Applications of Silicone Rubber Molding
Today’s manufacturing industries use the molding to produce a wide range of products we can easily find around us. From cookware to the lifestyle products you use, silicone rubbers have become a big part of our lives. Here are the applications of this rubber plastic molding:
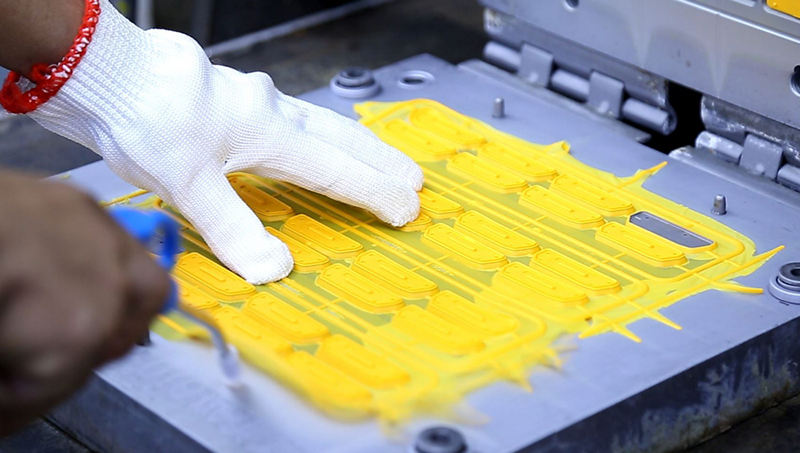
Rubber Molding in Medical
Silicone rubber molding can produce many products in the medical device development industry. These medical products have a principal role in helping healthcare professionals work with their patients better. Among the applications of the molding in the medical and healthcare industry include valves, tubing systems, catheter products, and anesthetics. Also, silicone rubbers are safe materials for the human body–another reason for their heavy usage in the medical industry.
Sealants
Another application of the molding is the production of sealants for various hardware parts. The sealants produced from silicone rubbers are often better than their rubber counterparts. Silicone rubber sealants will have very low porosity, making it possible for you to reduce the amount of potential leakage for the sealed hardware parts.
Rubber Molding in Consumer Electronics
You can also find many applications of the this molding process in the consumer electronics industry. Cables and electrical connectors are the everyday uses of silicone rubber materials in various electronic products. Silicone rubbers are also best for creating insulators in big electronic products like freezers, refrigerators, and cookware.
Food-grade Products
Silicone rubbers are very safe to use. The materials also have the non-toxic properties needed to create various food-grade products. You can use silicone rubber molding to produce food packaging equipment, parts for vending machines, and other food-grade items to help preserve different food products.
Rubber Molding in Lifestyle
Silicone rubber molding can also be advantageous for producing different lifestyle-related products, such as apparel, hair care products, cosmetics, and more. Silicone rubbers support today’s modern lifestyle with various uses, from fashion to skin care.
Automotive
The automotive industry also benefits from silicone rubber molding to create various essential parts in their vehicle production. You can use silicone rubbers in gaskets, sealants, radiators, and other automotive fasteners vehicle parts.
Advantages of Silicone Rubber Molding
Among the regular plastic and rubber materials, silicone rubbers are the most preferred materials for injection molding because of their unique properties. In a way, silicone rubbers are the upgraded version of regular rubber materials. Silicone rubbers can do many things much better than basic rubbers, especially in industrial applications. Here are the advantages of this molding:
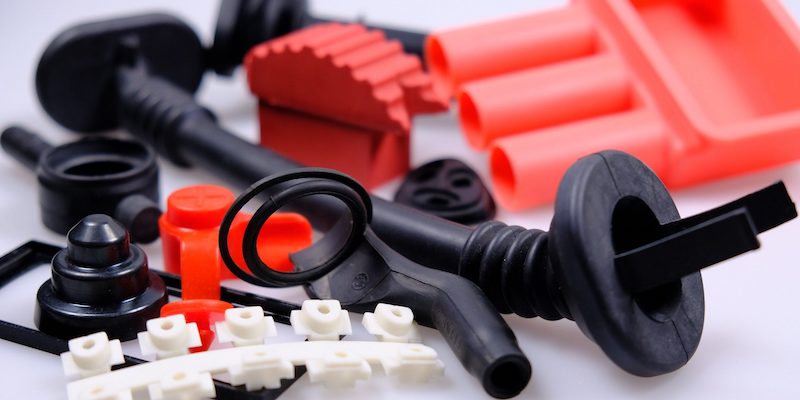
Lighter Mold
The molding process for the silicone rubber material will require you to use a mold lighter than usual. You need to use a heavier mold for the regular injection molding process, such as plastic injection molding. But, with silicone rubber, you need to use a lighter mold because of the characteristics of the silicone rubber material that is more susceptible to deformations.
Rubber Molding has Cheaper Production Costs
Using a lighter mold, accompanied by the silicone rubber materials, makes the overall silicone rubber molding cheaper for you to perform. Thus, you can use the molding to produce various consumer products at an affordable price and in low volume manufacturing. The affordability factor is not the only benefit of silicone rubber molding. Rubber molding is also faster, following the standard injection molding procedures.
Resistance to Heat and Compression
Silicone rubbers have a high level of resistance against heat and compression. It is tough to break or damage when you apply a lot of compression or pressure to it. Also, silicone rubbers are highly resistant to high temperatures or flames, making them safe for high-heat environments.
Highly Flexible
The high flexibility of silicone rubber is unmatched, especially compared to other plastic materials. No matter how you stretch the silicone rubber, it will return to its former shape. Silicone rubbers become one of the most flexible polymers for many industrial-level injection molding processes.
Rubber Molding Can have A High Level of Tensile Strength
Silicone rubbers also have a high level of tensile strength that allows the materials to keep their stable properties when you stretch them. Regular rubber materials might have similar tensile strength characteristics, but silicone rubber has a much higher tensile strength.
Perfect for Making Seals
Compared to regular rubbers containing porosity in their material buildup, silicone rubbers don’t have the same porosity. Thus, silicone rubbers are better materials for making seals than basic rubbers. Using silicone rubber materials can help prevent leaks and other problems during and after applying the seal.
A High Level of Versatility
Designing and molding a silicone rubber product is way easier than when you work with other plastic materials. You can customize the product in any shape you want. Also, it’s easier to mold design and create the mold for silicone rubbers, helping you meet your production goals faster.
Rubber Molding can have A High Level of Inertia
The inertia of silicone rubbers can help you use this molding material in various applications. It doesn’t react to most chemical components, making it a solid and steady material for different industrial purposes. The medical industry also benefits from the inert properties of silicone rubbers, making them suitable for creating medical products that are safe for human contact.
Conclusion
With a high level of flexibility and versatility, silicone rubbers have become the most preferred rubber materials for many industries nowadays. From helping healthcare professionals work with their patients to helping you keep your food safe, silicone rubber molding has contributed a lot of uses in our everyday lives. You can use this molding today to help create the best products for your manufacturing projects.
Besides from injection molding, TEAM Rapid also offers rapid prototyping, CNC machining services, and die casting to meet your project needs. Contact our team today to request a free quote now!