Insert moulding has emerged as a revolutionary method in the dynamic field, innovating in the production of quality products. Its applications broaden the range of industries, while its interest increases in hearing details with good design considerations and self-consciousness. Which is critical to success in its full potential.
Table of Contents
- 1 Design Considerations Unraveling core: Fusion in Insert Molding
- 2 Creating Masterpieces: Exploring the Complexities of the Insert Molding Process in Design considerations.
- 3 Fine Art: Insert Molding Design considerations Guide
- 4 Case studies: Learning from Success
- 5 Releasing Flexibility: The Art of Complexity
- 5.1 Q: How does insert moulding pave the way for more complex and sophisticated design Considerations?
- 5.2 Q: Design considerations – How does insert moulding contribute to production consistency?
- 5.3 Q: How does insert moulding achieve a delicate balance between weight reduction and strength enhancement?
- 6 Conclusion: Guidelines for the Design Considerations
Design Considerations Unraveling core: Fusion in Insert Molding
Essentially, insert moulding is a careful choreography in which molten plastic resin neatly covers a well-placed metal insert. This dynamic integration manifests itself under the guidance of specialized horizontal production machines. Akining to master musicians conducting an orchestra of materials. However, the particles extend beyond basic fusion, encompassing the delicate art of temperature and pressure control.
In the lab, these particles are craftsmen’s tools, conditions of optimization to ensure a harmonious and harmonious mix of plastics and metals. Imagine a ballet of molecules perfectly designed, culminating in a final product that not only fulfills functional requirements but enforces the art of seamless integration. This is where insert moulding, amid an intricate dance of materials and machinery, transcends mere manufacturing and becomes a play of artistic and technical genius.
Creating Masterpieces: Exploring the Complexities of the Insert Molding Process in Design considerations.
When you start the journey with insert moulding, it feels like a masterful art form. Starting with shaping the metal insert, the process goes smoothly. This preparation stage sets the stage for the insertion of the molten plastic resin, and the metal-plastic compound plays an important role.
In this vessel of creativity, a delicate balance is required – a careful balance that goes beyond a mere pile of ingredients. The goal is not only to achieve an evenly hardened product but also to ensure a strong bond between the plastic and metal components. This conversion phase is where the alchemy of insert plastic molding comes to life.
But as with any artistic endeavour, challenges cast their shadow. Flaws such as the creation of a vacuum, weld lines, or the threat of interference add complexity to the creative process. Addressing these challenges requires more than just technical expertise; It requires an unwavering commitment to perfection. This commitment manifests itself through meticulous temperature and pressure control. Ensuring that every product comes out flawless and free of defects that could compromise its structural integrity.
Essentially, the insert injection moulding process is not just a technical feat but a well-prepared set of steps to create a rhythm; each contribution to a masterpiece is a testament to the fusion of art and technology, where precision connects with creativity to make things beyond function.
Fine Art: Insert Molding Design considerations Guide
The instruction set plan is a comprehensive insert mold design guide. This design encourages designers to avoid sharp corners, maintain uniform surface thickness, and carefully select materials for plastic and metal parts. The last important task is to put the product to work under thorough testing at the end of use to ensure it meets real-world requirements.
Case studies: Learning from Success
There are real-world case studies of the efficacy of inserts. From electronic components to automotive parts, medical devices, and consumer products, these examples demonstrate the tangible impact of design thinking on the final product. These studies create roadmaps for engineers and aspiring designers, providing insight into the fine art of successful packaging applications.
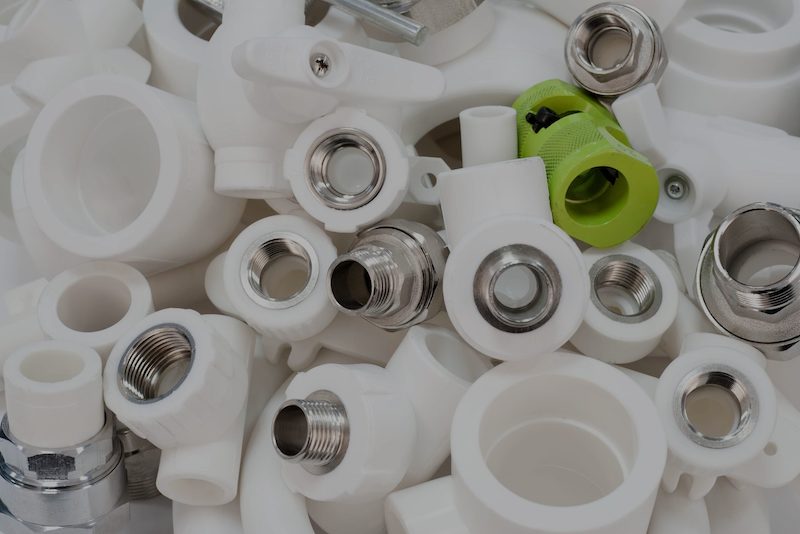
Releasing Flexibility: The Art of Complexity
Insert moulding gives the designer freedom, resulting in remarkably strong fabrics. This innovation flexibility is particularly important in industries where specificity and expertise are a determinant of success. The question then arises: How do inputs pave the way for complexity and sophistication?
Q: How does insert moulding pave the way for more complex and sophisticated design Considerations?
A: Insert moulding’s ability to precisely insert metal inserts allows for stronger products, combining the strength of metal with the versatility of moulded plastic. This connectivity enables the manufacture of products with complex geometries, sophisticated features and unique functionality to meet the demands of innovative design requirements
Balance sheet: Cost of Insert Molding
The efficiency of the insert moulding system is reflected in the low cost of production. The addition of multiple components to a flexible system reduces production time, thereby reducing labour costs. As we go through the comparative analysis with conventional methods, the economic advantage of insert moulding becomes more apparent.
Sustainability at Work: Engage Molding with the Environment
At a time when environmental considerations are paramount, inserts emerge as a sustainable solution. Reduced energy consumption, minimal waste, and low environmental impact make pottery an environmentally friendly option. This raises the question: how does insert moulding contribute to sustainable construction practices?
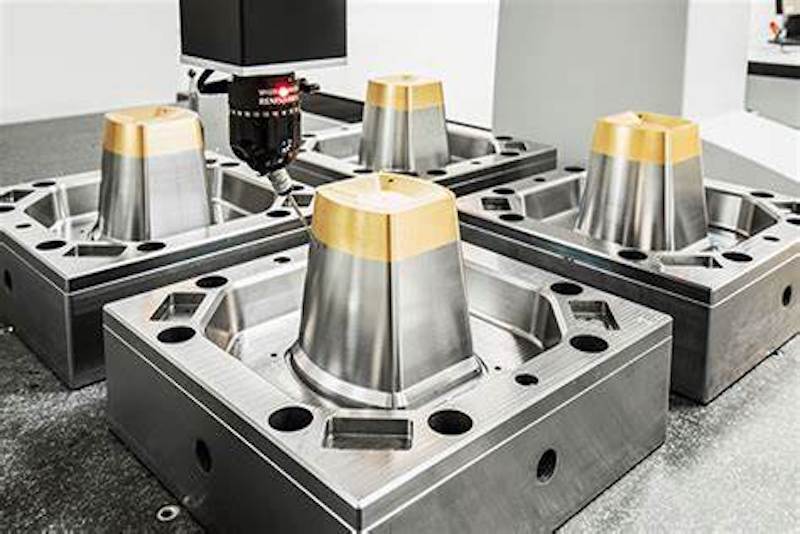
Q: Design considerations – How does insert moulding contribute to production consistency?
A: Insert moulding helps sustain materials by reducing waste with its efficient, one-step process. The efficient manufacturing process and low energy consumption make it environmentally friendly. The integration of design thinking further ensures that the resulting products are durable and have an extended life cycle in line with the principles of sustainability
Weightless but Strong: The Promise of Weight and Volume Reduction
The promise of packaging extends beyond design flexibility and cost reduction. The ability to produce lightweight yet strong materials benefits applications with severe weight and size constraints, such as aeroplanes and automobiles. The question remains: How does insert moulding achieve balance? Want a simple trade-off between weight loss and strength gain?
Q: How does insert moulding achieve a delicate balance between weight reduction and strength enhancement?
A: The integration of steel inserts adds strength and strength to the moulded components. This allows engineers to design details without compromising system integrity. By strategically placing metal inserts, the inserts achieve a flexible balance that meets the requirement of weight reduction without sacrificing strength.
Performance competency: Vitality and Confidence
The combination of steel inserts not only increases strength but also increases overall reliability. As we explore industries where complex rapid manufacturing is out of the question, insert moulding is emerging as a preferred option, offering materials that can withstand the rigours of demanding applications.
Conclusion: Guidelines for the Design Considerations
Insert moulding shines as a light of creativity in the confusing world of contemporary architecture. Understanding the complexity, adhering to design thinking’s tenets, and maximizing its potential for a range of applications are necessary for success. As we look to the future, insert moulding continues to be a showcase for engineering brilliance and shapes how we envision and build the world of stimulating components.
TEAM Rapid offers not only insert molding, but also overmolding for your rapid prototyping, low volume manufacturing, and mass production needs. Contact us today to request a free quote now!