Ready for your next batch of plastic manufacturing process? Vacuum casting manufacturing can be an excellent choice to get your plastic parts and components ready to market. Vacuum-casted products are in high demand today, with many industries using these plastic products for various assembly processes.
Table of Contents
- 1 Here are the benefits of vacuum casting manufacturing:
- 1.1 Vacuum casting manufacturing: Faster Production Process with Affordable Costs
- 1.2 Precise, Accurate, and Durable Parts Production
- 1.3 Consistent Parts or Components Quality
- 1.4 Vacuum Casting manufacturing: Various Applicable Surface Finishes
- 1.5 Compatible with Complex Geometric Designs
- 1.6 vacuum casting manufacturing: Abundant of Color Options
- 1.7 vacuum casting manufacturing: Material Options and Material Grades
- 1.8 vacuum casting manufacturing: Suitable to Produce Parts or Components with Thin Wall Structures
- 1.9 Smoother and More Polished Surface Finishes
- 1.10 vacuum casting manufacturing: Best for Plastic Parts Low Volume Manufacturing services
- 2 Conclusion of vacuum casting manufacturing
Here are the benefits of vacuum casting manufacturing:
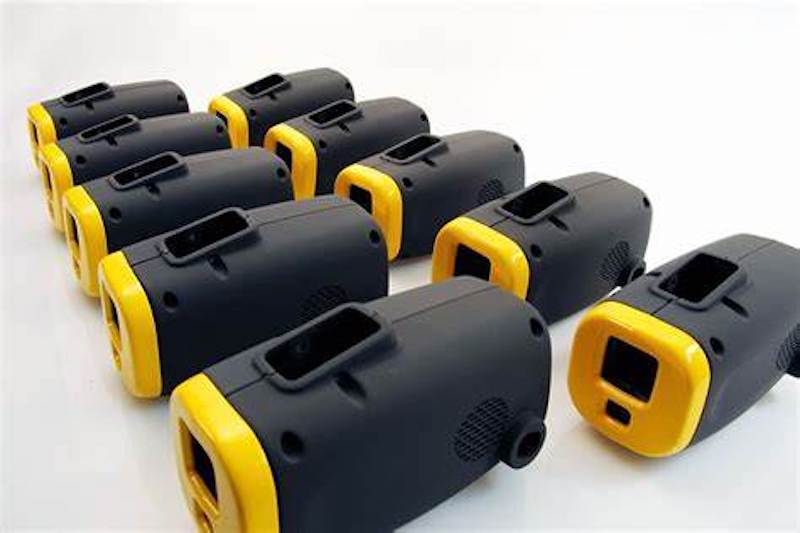
Vacuum casting manufacturing: Faster Production Process with Affordable Costs
The fast production process and affordable costs will make vacuum casting one of the best rapid manufacturing solution for small to medium-scale businesses. You can create various plastic parts and components in different sizes using vacuum casting without breaking your budget.
Budgeting with vacuum casting is also easy because you can pick the level of quality you want to achieve in your plastic products.
Precise, Accurate, and Durable Parts Production
Another advantage of vacuum casting revolves around the precision of plastic parts or components you produce. Vacuum casting can provide you with plastic parts or components with precise, accurate, and durable characteristics. It means the measurements and dimensional properties of the plastic part or component you produce with vacuum casting will have the same properties as dictated by your design blueprint.
There will be minimum to no deviation in the characteristics of the plastic part or rapid prototyping parts you produce with vacuum casting. The production results will also be perfect for further assembly.
Consistent Parts or Components Quality
Need to produce a large volume of plastic parts or components with vacuum casting? All your plastic parts or components will have consistent quality. Vacuum casting is suitable for a larger volume production, with reliable consistency for the production results. You will find less damage or deformations during the vacuum casting production process.
Inconsistent sizes and dimensions for your plastic products can bring bad experiences in further manufacturing and assembly processes. Vacuum casting will prevent the inconsistency problem from happening in your manufacturing production.
Vacuum Casting manufacturing: Various Applicable Surface Finishes
The good thing about vacuum casting is that you can apply various surface finishes to the resulting parts or products. The options are many for the surface finishes you can perform on the vacuum-casted plastic parts, including glossy smooth, structured, polished metallic, and very rough finishes. Vacuum casting finishes can give you plenty of variations in the plastic components you produce.
Applying the vacuum casting finishes is also simple and fast to do. So, you don’t need to wait longer just to get your vacuum-casted products ready to market.
Compatible with Complex Geometric Designs
Vacuum casting is not a manufacturing method that only accepts simple blueprint designs. You can submit blueprint designs with complex geometrical shapes and use them with vacuum casting. So, you can make vacuum-casted products with complex shapes, which will fit various assembly processes with other products.
The compatibility with complex geometric designs will allow you to add more features to the vacuum-casted parts or components you produce. Vacuum casting will deliver these products according to your submitted blueprint design.
vacuum casting manufacturing: Abundant of Color Options
You can also apply various colors on the surface of the vacuum-casted parts or components you produce. As with the colors, there are many color options you can choose from. So, aside from the variations in the surface finishes, you can also get variations of colors with vacuum casting. The sky’s the limit for the aesthetic you can give for the vacuum-casted products.
With the abundant color options, you can market your vacuum-casted products in different models, which can also help increase the profitability of your products.
vacuum casting manufacturing: Material Options and Material Grades
Vacuum casting is also compatible with various material options and material grades for each of your production runs. For the budget-conscious, vacuum casting can provide you with a selection of cheaper materials with a higher material grade. Also, there are premium-level plastic materials for high-quality and premium vacuum casting production. So, there’s flexibility in how you can approach each vacuum casting process based on your project requirements.
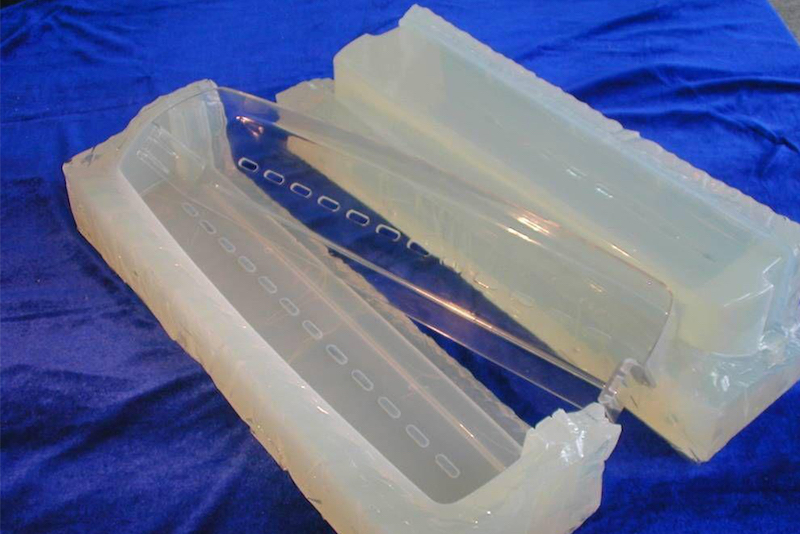
With various grades or quality levels offered for each plastic material, you can also use the most suitable vacuum-casting materials based on your project and target audience.
vacuum casting manufacturing: Suitable to Produce Parts or Components with Thin Wall Structures
Producing thin-walled plastic parts or rapid prototypes has plenty of risks involved. You can risk damaging the thin walls during production if you don’t calculate your design accurately. Also, thin-walled plastics will naturally be weaker in structure than metals. However, you can use vacuum casting to create plastic parts or components with thin-walled structures without considerable issues.
Creating thin-walled plastic components or parts will still require a highly accurate calculation in your design blueprint. It is to maintain the overall parts’ structural integrity and durability for long-term use.
Smoother and More Polished Surface Finishes
Vacuum casting can produce neat-looking plastic products with more polished surface finishes, even before you apply any post-processing on them. With more polished surface finishes, vacuum casting can provide great-looking and aesthetically designed plastic parts and components for various industrial applications. The surface finishing of the vacuum-casted plastic products is also smooth and high quality.
The result will be better when you apply additional surface finishing processes for your vacuum-casted products. It can add a more premium feel to the plastic vacuum-casted parts or components you produce for your project.
vacuum casting manufacturing: Best for Plastic Parts Low Volume Manufacturing services
You can only use plastic materials with vacuum casting. Vacuum casting doesn’t support the casting of metals. However, with its specialization in plastic materials, vacuum casting has become the best manufacturing method for plastic parts production in various industries. You can use vacuum casting to produce small or big-sized vacuum-casted plastic parts.
Vacuum casting is the best production method for manufacturing projects involving plastic materials, and you can complete it with a low budget and within a tight deadline.
Conclusion of vacuum casting manufacturing
Many benefits of vacuum casting are ready to give you the best production results for your manufacturing project. Use vacuum casting in your next manufacturing production plan and take advantage of the vacuum casting production process to create the best quality vacuum-casted plastic parts and components.
Besides from vacuum casting, TEAM Rapid also offers 3d print services, injection moulding services, and die casting to meet your projects needs. Contact us today to request a free quote now!