With the advancing technology in sheet metal forming, you can now use a computerized design in your sheet metal production. With the assistance of 3D software, it’s easier nowadays to create the design for your metal sheet products. However, some basic sheet metal design principles are still in place, which you need to follow.
Table of Contents
- 1 Precautions Before Creating a Design for Sheet Metal Forming
- 2 Design Steps and Processes of Sheet Metal Forming
- 2.1 Calculating the Basic Parameters of the Sheet Metal Materials
- 2.2 Use 3D Design Software to Create the Design Blueprint of Your Product.
- 2.3 Calculate the Steps Necessary to Meet Your Product’s Requirements
- 2.4 Apply Various Sheet Metal Forming Methods
- 2.5 Quality Checking the Product after Sheet Metal Forming
- 3 Conclusion
Precautions Before Creating a Design for Sheet Metal Forming
There are some crucial things to acknowledge before designing a product for sheet metal forming. You can examine these precautions before creating a design for sheet metal forming:
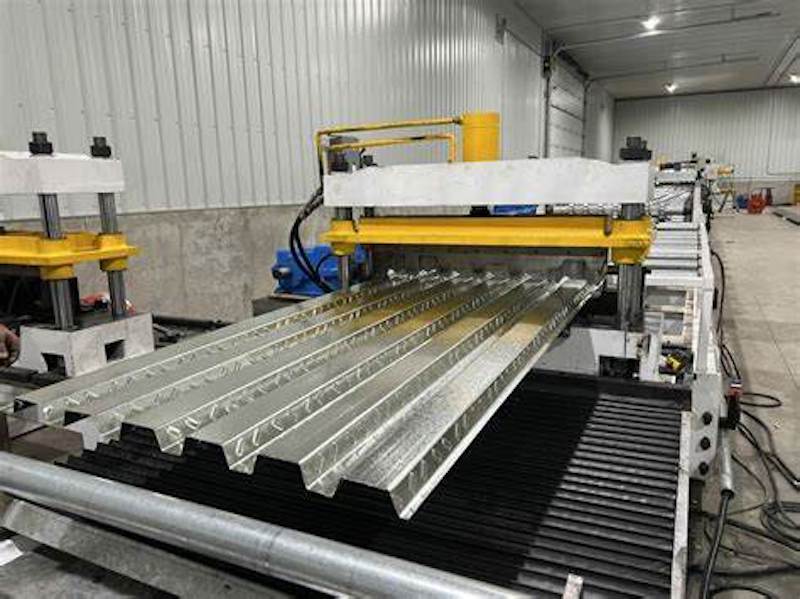
Minimum Bending Radius for the Sheet Metal
Each sheet metal material has a bending radius, which determines the maximum bending area you can apply. Be sure to follow the bending radius calculation in your sheet metal design. You might damage the sheet metal materials during the metal sheet forming process when you disregard the bend radius calculation.
Bend Orientation and Hole Size
The bend orientation you apply will affect the overall looks of the resulting sheet metal product. In your design, it’s essential to determine the bend orientation of each sheet metal. Be sure that the bed orientation will be uniform among the various metal sheets you use for the product. The hole size in each metal sheet should not exceed the overall thickness of the sheet metal materials. It will avoid many potential issues in your sheet metal product and mold design.
Material Characteristics
Every available metal sheet material will have differing characteristics that make it good or bad for your project. It would be best if you considered the properties of your sheet metal material before starting the design process.
By examining the material properties, you can adapt your design blueprint based on the capability of the metal sheet you use. Also, you can avoid any potential issues during the sheet metal forming process.
Tight Tolerances and Offsets
Each sheet metal will also have tight tolerances that it can handle during the sheet metal forming process. Designing your sheet metal products must include calculating the best tolerances for your product design and whether you should use normal or tight tolerances.
Creating offsets in your product design will also help you get the perfect measurement for your product later. Offsetting will help maintain the correct dimensions for your product and avoid any issues in your production.
Design Steps and Processes of Sheet Metal Forming
Designing a sheet metal product is a bit complicated because you need to think about various aspects of the metal sheets and how you want to build your product. Wrong calculations can lead to technical issues with your metal sheet product and potential deformations. Here are the design steps and processes of sheet metal forming:
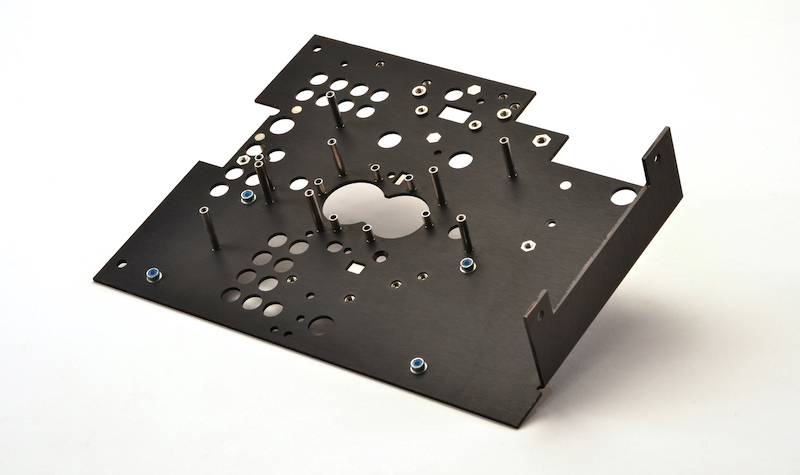
Calculating the Basic Parameters of the Sheet Metal Materials
Before starting your design process, you must gather enough information about the sheet metal material you will use to create the product. You must know the capabilities of the metal sheet materials and how they can handle various sheet metal forming processes during the manufacturing phase. It will serve as the basic information on which to base your design blueprint.
Next, you must know the technical limitations of the sheet metal materials you will use for your product, such as the maximum bend radius, tight tolerances, etc. Design your end product based on these parameters and technical limitations.
Use 3D Design Software to Create the Design Blueprint of Your Product.
Designing a blueprint for your sheet metal product requires 3D design software. You can use open-source or commercial 3D design software to create the blueprint for your sheet metal product. You can add new features to your product with the 3D design software while still considering all the characteristics of the sheet metal materials you will use.
Building a product with sheet metal differs from using CNC machining services or 3D printing. So, keep in mind the technical specs of the sheet metal as the primary material for your product. Understand what you can and can’t do with the sheet metal materials.
Calculate the Steps Necessary to Meet Your Product’s Requirements
During the sheet metal forming production, you can apply various sheet metal-related processes to meet your product’s requirements. You can bend the sheet metal, add holes to the sheet metal, or fold the sheet metal to follow your design blueprint. You need to calculate the necessary steps to turn your design blueprint into an actual product with metal sheet forming.
Calculate the length and radius of your bend, the orientation of your fold, the position of the holes, etc. Be as specific as possible using an actual measurement to help create a functional product using sheet metal. Create a detailed blueprint for your sheet metal product, which you can follow precisely later.
Apply Various Sheet Metal Forming Methods
Next, it’s time for you to use the sheet metal bending equipment to work on the sheet metal materials and follow your design or sheet metal prototype blueprint. Convert your design blueprint into specific commands for the sheet metal equipment. Then, apply various sheet metal forming methods following the production commands you have created.
Modern sheet metal tools will allow you to use computerized commands to work on each sheet metal forming method following your design blueprint. It will take a longer time to follow your design blueprint when using manual sheet metal equipment. So, using computerized sheet metal equipment will be preferable, especially if you need to follow a complex design blueprint for your product.
Quality Checking the Product after Sheet Metal Forming
After completing all the metal sheet forming activities, it’s time for you to check the quality of your sheet metal product. Quality checking is essential because it can make or break your product. A good sheet metal product will have excellent quality, with correct functions and features. There should be no technical issues, damages, or deformations for the sheet metal product you create.
Performing regular QC activities after your sheet metal forming low volume manufacturing and production will ensure the best customer satisfaction and help retain the value of your sheet metal product. It will also warrant using your sheet metal product for the next production steps, such as during assembly and disassembly.
Conclusion
Always take the necessary steps before designing your sheet metal product to avoid any problems during sheet metal forming later. It would help if you studied the advantages and limitations of the metal sheet materials you will use in your production. Also, check the quality of your sheet metal products before wrapping up your production schedule.
Besides from sheet metal fabrication, TEAM Rapid also offers rapid prototyping, CNC machining, injection moulding, and die casting to meet your project needs. Contact us today!