The use of undercuts can complicate the entire rapid manufacturing process if you don’t do it in the right way. Undercuts are sometimes problematic, and it can give the final products some inherent design flaws, which is the reason manufacturers will avoid it as much as possible. However, there are some effective uses of undercuts in the injection molding process, which can help you take the best advantage of it. In this guide, we will delve deeper into learning about the effective use of undercuts injection molding designs.
Table of Contents
What is Undercuts Injection Molding?
Undercuts can take various forms, such as holes, latches, snaps, and other unique designs. But what is undercut in plastic injection molding? To put it simply, undercut in injection molding means the specific region of your hardware parts or components that are not available for ejection from the mold.
During the injection molding process, you will need to release your rapid prototypes, parts and components from its mold once the process is complete. However, if there is a certain part of the hardware that you can’t remove from the mold, you can call it an undercut. Undercut can have various uses in a wide range of industries, whether it is medical, electronics, automotive, and others. However, it’s best for you to use undercuts effectively to avoid any problems in your subsequent production processes.
Effective Uses of Undercuts Injection Molding
Applying undercuts will provide you with various benefits in your parts production. Some undercuts have specific functions, whereas some others might not have any specific function other than to add some decorative aspects of your hardware designs. Here are some effective uses of undercuts in injection molding:
●Creating special designs for your hardware and sheet metalwork parts.
Some parts have special designs that you can’t create simply by using regular cuts. Thus, you will need to apply undercuts to follow those special designs, so that you can create the correct hardware body, sizes, and dimensions. Some special designs that require using undercuts include interlock, fitting, custom inserts, side holes, and more.
●Connecting other parts via the undercut holes.
Another effective use of undercuts is that it will allow you to connect to other parts via the undercut holes you have made. This way, you can assemble the final product by building the smaller parts through these connecting holes. You can only create these holes by using undercuts, not regular cuts.
●Creating vertical threading for parts and components.
Vertical threading is a common aspect of any product assembly process, whereby you use the vertical threads to hook up connectors, components, and other smaller parts together. Like undercut holes, vertical threads can only be applied via undercuts, so you can’t do it any other way.
●Using the interlocking mechanism.
There are various hardware CNC machining parts that require the use of interlocking mechanisms across a wide range of industries, such as in the automotive and medical industries. It will allow you to snap the hardware component to another component and lock them together for them to work. This is another effective use of undercuts, which will allow you to create the interlocking mechanism in various hardware parts and components.
●Using specific geometrical complexities for your parts.
Sometimes, undercuts don’t have any specific function other than adding some specific geometrical complexities for your parts. Thus, you can use undercuts to add certain unique styles for your hardware designs, allowing you to make it more aesthetically appealing. This is the effective use of undercuts that manufacturers can take advantage of in their production process.
Important Things to Keep in Mind when Using Undercuts Injection Molding
Undercuts can be a problem in your manufacturing production, but the right use of undercuts can give you some advantages. The good way to approach undercuts is that you shouldn’t be completely against it, but you need to know exactly when to use it and how you should deal with it. Here are some important things to keep in mind when using undercuts in injection molding(especially for overmolding and insert molding):
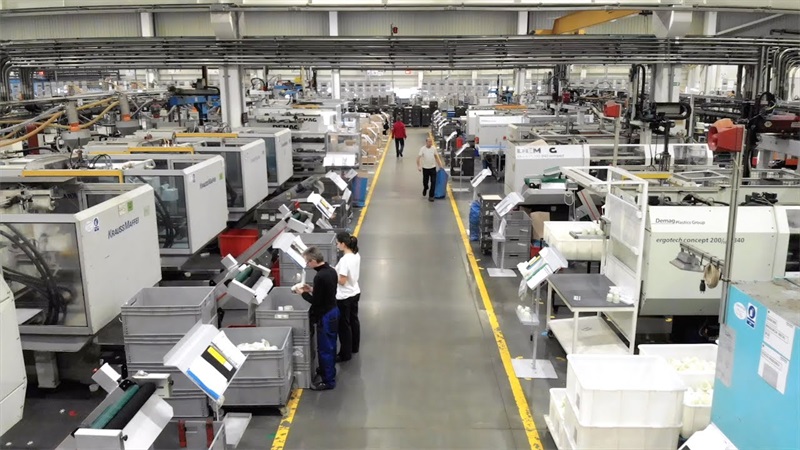
●Use undercuts only when necessary.
Most manufacturers will avoid using undercuts because it can pose a problem in their overall product design. So, it’s best for you to use undercuts only when necessary. Some applications, such as in the medical field, consumer electronics, automotive, and other industries, will require the use of undercuts in their parts design. However, it is still important for you to use the most effective undercut designs to avoid problems with your parts or components later on.
●Inspect your CAD design before using Undercuts injection molding process.
It’s always best for you to double-check your CAD design by mold flow services before using it in your injection molding process, as a wrong design can cause bad undercut problems later. Inspect your CAD design for potential use of undercuts for your parts and components, and calculate the undercuts well, so you can make effective use of it.
●Use the best undercut techniques for your design.
There are excellent undercut styles you can use for your parts design, such as pick-out inserts and side actions. These undercut techniques can save you a lot of hassles in your injection molding production, providing you with the best undercuts for different material types.
●Use the right parting line to avoid bad undercuts.
You can prevent bad undercuts by using the right parting line in your injection molding process. The parting line on the molds can create an undercut problem if you don’t set it in the right way. Thus, it’s important for you to examine your mold design and determine the right point for the parting line before putting it into production.
●Applying the hand-loaded inserts for undercuts injection molding.
Hand-loaded inserts are the inserts you will need to apply manually to deal with the undercut problem in your injection molding process. You will need your technician to apply this method if you have some undercut problems in your injection molding process. However, you need to use caution to ensure that you can stay safe during the application of hand-loaded inserts.
Conclusion
It’s best for you to follow the effective uses of undercuts in injection molding as explained above, so you can get the best undercut applications in your production. You also need to give a closer look at your CAD design to ensure that you get the best undercuts for your hardware parts and components and make some improvements when necessary.
TEAM Rapid has over 10 years injection molding experience, we help many customer to make their undercuts injection molding projects successfully, they are happy with our quality and price. As a one-stop factory, we understand what the customers’ needs, and offer a series of manufacturing services such as 3d print services, die casting services, etc besides from the injection molding. Contact our team for a free quote now!