Are you among the ones looking for medical device parts with exceptional detail and high precision? Vacuum casting must be your best pick. It comes as a game-changing technique to help you produce high-quality parts for small and medium batch production with unparalleled benefits. What about vacuum casting? Let’s take a closer look at the benefits and best practices of vacuum casting for medical devices.
Table of Contents
- 1 What’s Vacuum Casting?
- 2 Benefits of Vacuum Casting for Medical Device Manufacturing
- 3 Vacuum Casting For Medical Devices: Best Practices
- 4 Get Precision & Durability in Every Cast Part with TEAM Rapid Tooling
- 5 Materials Used in Vacuum Casting for Medical Devices
- 6 Alternatives of Vacuum Casting for Medical Devices
- 7 Conclusion
What’s Vacuum Casting?
Vacuum casting, or urethane casting, is a manufacturing process used to create limited runs of high-quality plastic or metal components. The process begins by crafting a mold of the intended part, which is then filled with liquid plastic or metal under vacuum conditions. This contributes to a part that is consistently detailed with superior surface finish and precise dimensions.
Process
- The master mold is created via CNC machining or 3D printing.
- This mold will be placed in a container and filled with silicone.
- The silicone dries rapidly to form a mold ready for vacuum casting of plastic or metal.
It performs well with high precision and consistency, making it an excellent option for situations where exact measurements are essential. It also supports the casting of more complex designs. However, vacuum casting is not ideal for every situation, especially when handling materials that are sensitive to heat or pressure.
Benefits of Vacuum Casting for Medical Device Manufacturing
Why opt for vacuum casting for your project? As we know, the medical sector is a highly sensitive sector, which means that the materials selected should be based on strict criteria. Then, the vacuum casting better aids in fulfilling those standards. Here are several reasons to opt for vacuum casting in the rapid prototyping and production of medical device components:
Exceptional Precision and Detail Accuracy
One of the main benefits of vacuum casting is its exceptional precision and detail accuracy, though this largely depends on the accuracy of the master mold. The process excels at producing parts with precise dimensions, which is crucial in medical applications where even the smallest differences can make a big difference. Generally, you can expect that vacuum casting can achieve an accuracy of even 0.05mm.
vacuum casting for medical devices: Material Flexibility
Renowned for its great material versatility, vacuum casting stands out as an ideal option across various industries, particularly in medical device manufacturing. This technique empowers manufacturers to utilize a wide spectrum of plastics and resins (including ABS, Rubber, Polypropylene, HDPE, Polyamide, Polycarbonate, PMMA (Acrylic), and Glass Filled Nylon, better catering to diverse requirements in the medical sector.
High Quality
Vacuum casting delivers an excellent surface finish in medical devices. Resin copies of the master model match it in terms of quality and attributes, including texture, surface detail, tolerance, and dimensions. Besides, color pigments can be incorporated to create any desired surface finish, whether glossy, matte, or a unique texture.
Vacuum Casting for Medical devices: Affordability for Small Batches
When it comes to medical device rapid manufacturing, particularly during the development stages, you must consider its managing costs. It’s important to avoid too much expense on prototypes and testing. Luckily, vacuum casting offers a more economical solution compared to other rapid manufacturing techniques. It requires a lower upfront tooling investment and only needs a master mold and resin materials. A single mold can produce up to 25 copies. Unlike other techniques, vacuum casting doesn’t rely on high-powered machines, reducing electricity consumption and overall operational costs.
Shorter Lead Times
In the medical industry which highly stresses rapid production speed, researchers need a quicker process to test their hypotheses efficiently. While methods like injection molding have a lead time of 2 to 3 weeks, vacuum casting shortens this period to just 10 to 15 days from concept to finished product.
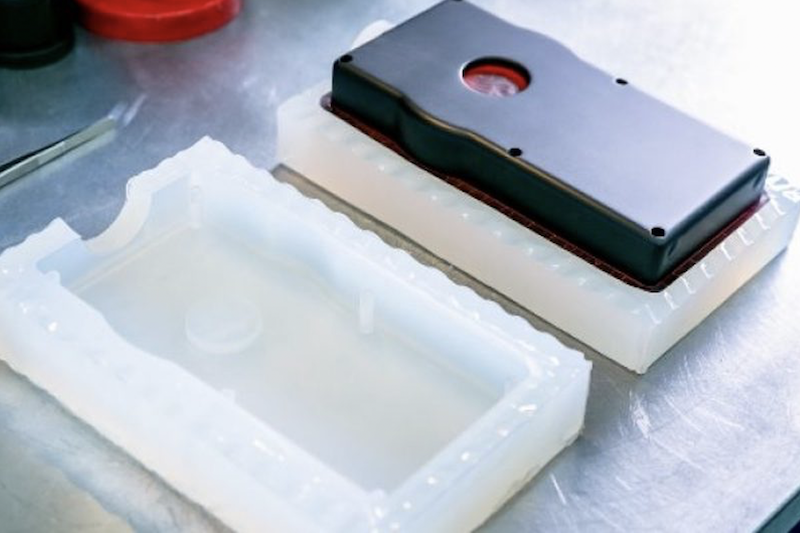
Minimized Risk of Air Bubbles and Imperfections
In casting process, trapped air with molten material can create bubbles, resulting in imperfections in the products. To prevent this, casting is performed under a vacuum, eliminating the formation of bubbles and ensuring the molten material fills every part of the silicone mold.
Flexible Design Modifications
The use of permanent metal molds in metal die cast makes design modifications both challenging and costly. In contrast, the silicone itself is cheap and the silicone molds are more affordable and easier to produce. Before full-scale production, you can easily modify or redesign the mold at a relatively low cost. This approach also accelerates the development process while ensuring that high-quality standards are upheld.
Vacuum Casting For Medical Devices: Best Practices
Vacuum casting is widely adopted across various industries due to its adaptability and exceptional accuracy, with its importance in the medical sector standing out. This technique is especially beneficial for creating exact replicas of human organs or complex components of medical equipment. Now, let’s have a look at its typical uses in the medical sector, accompanied by best practices of devices and components produced through vacuum casting.
Application | Best Practices |
Prosthetic Parts | lightweight prosthetic limbs with customized shapes and sizes |
Implant Prototypes | joint replacements, spinal implants, and dental implants |
Surgical Models and Simulators | anatomical models, surgical training simulators, and practice dummies |
Medical Enclosures and Housings | diagnostic device casings, portable medical equipment housings, and protective covers |
Hearing Aid Components | custom ear molds, protective casings, and internal component housings for hearing aids |
Surgical Instruments and Tools | ergonomic handles, precision tool prototypes, and custom grips for surgical instruments |
Respiratory Therapy Devices | mask components, tubing connectors, and device housings in respiratory therapy devices |
Dental Devices | dental impression trays, orthodontic device components, and custom molds |
Custom Orthotics and Braces | foot orthotics, knee braces, and support splints |
Get Precision & Durability in Every Cast Part with TEAM Rapid Tooling
TEAM Rapid Tooling excels in delivering precision medical device parts through expert rapid tooling and vacuum casting. It makes it possible to bring your designs into reality from producing detailed medical prototypes to small batch productions.
The skilled engineering team will provide you with professional ideas on choosing the most appropriate manufacturing method, whether it’s injection molding for large-scale production, 3D printing for detailed designs, or CNC machining for precision components. With quick turnaround times and the ability to customize solutions like custom orthotics, dental tools, and respiratory therapy components, TEAM Rapid Tooling will better meet your specific medical needs efficiently.
As a reliable partner, TEAM Rapid Tooling supports medical device manufacturers in achieving superior performance and efficiency. Trust us as a go-to choice for your precision medical component needs. Get a quote today!
Materials Used in Vacuum Casting for Medical Devices
A wide range of plastics is commonly utilized in the production of medical devices because of their versatility and dependability. These materials are preferred for their capability to fulfill the rigorous standards required in medical applications. Different materials offer different properties, making them ideal for specific applications. Here are some popular material options.
Material | Description |
Rubber Grade Materials | Rubber is favored for its flexibility, allowing it to be easily shaped into intricate forms. It is also cost-effective and recyclable. In vacuum casting, rubber-like materials such as T0387, a translucent rubber, and UPX800 are commonly used. This kind of material is excellent for crafting elastic prototypes. |
Polypropylene (PP) and HDPE | Polypropylene (PP) is a type of thermoplastic material that is particularly well-suited for use in vacuum casting processes. It is known for being lightweight and resistant to heat. Similar in properties is high-density polyethylene (HDPE), though it is more rigid than PP. |
Polyamide | Polyamide, commonly known as nylon, boasts superior strength and durability while being exceptionally flexible. This ensures that components can endure the mechanical stress they encounter during usage. It is particularly recognized for its chemical resistance, which makes it perfect for uses that involve elevated temperatures. |
Polycarbonate-like Resins | Polycarbonate-like resins are renowned for their exceptional durability combined with a lightweight structure. Besides, their excellent dimensional stability ensures that components retain their shape and function over time, even under varying environmental conditions. UP6160 and PX510 are frequently used in polyurethane casting. |
PMMA/Acrylic-like | With exceptional clarity, acrylic (also known as PMMA), allows for excellent visibility, which is crucial in medical sectors where precision and observation are vital. Its lightweight nature makes it an easy material to handle and integrate into various devices, reducing the overall weight of medical equipment without compromising strength. In the market, popular PMMA grades include X522HT, PX5210, and PX5210H. |
Glass-filled Nylon-like Material | Glass fiber-reinforced nylon is an innovative material increasingly used in the vacuum casting of medical devices. Adding glass fibers to nylon greatly enhances its strength and rigidity while also boosting its resistance to wear and thermal stress. This makes it particularly well-suited for internal moving parts that experience friction and wear. |
ABS-like General Purpose Resin | Characterized by a low melting viscosity, ABS simplifies the casting process. Once solidified, it exhibits impressive impact resistance, toughness, and chemical resilience. Its dimensional stability ensures that ABS components remain free from warping over time. Additionally, the variants, PU8260 and PU8263, offer superior flame resistance, making them ideal for producing robust and high-strength parts with smooth surfaces. |
Filled ABS | Filled ABS often integrates ABS with various materials to improve its attributes. This significantly boosts its strength, rigidity, and impact resistance, making it a highly reliable choice for medical applications, and contributing to the longevity and reliability of medical devices. |
Alternatives of Vacuum Casting for Medical Devices
While vacuum casting is a popular choice, several alternatives are available for different stages of medical device manufacturing to achieve similar results. Key among these are injection molding, 3D printing, and CNC machining.
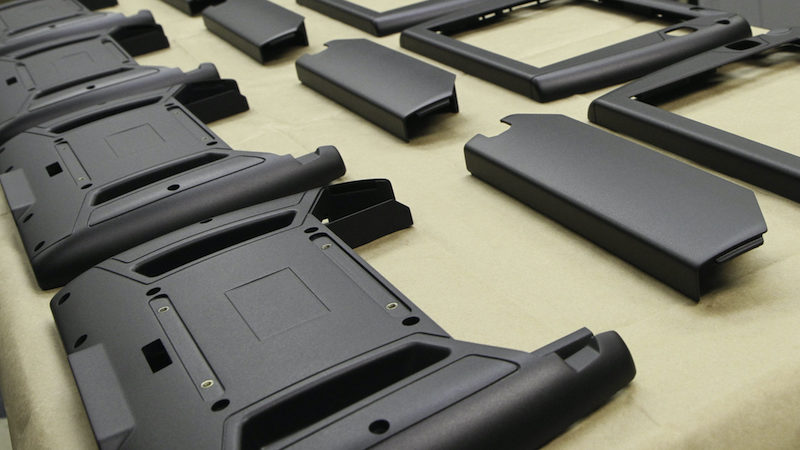
Vacuum Casting vs Injection Molding
Injection molding service shares similarities with vacuum molding as both processes utilize a mold cavity to form products. Vacuum casting is often employed for creating prototypes and producing small batches thanks to its cost-efficiency and adaptability. Unlike injection molding, it doesn’t require a DFM process. Many developers adopt it for testing and development stages. In contrast, injection molding is more suitable for mass-produced parts because of its precision and efficiency.
Vacuum Casting vs 3D Printing
Both vacuum casting and 3D printing offer distinct advantages in manufacturing. 3D printing is an additive manufacturing process praised for its ability to achieve high levels of customization and rapidly prototype complex geometries. In contrast, vacuum casting excels in providing superior surface finish and is more cost-effective for low volume manufacturing.
Vacuum Casting vs CNC Machining
Vacuum casting and CNC (Computer Numeric Control) machining cater to different manufacturing needs. CNC machining is a subtractive process. Renowned for its precision and versatility, it is capable of handling a broad spectrum of materials to produce intricate and accurate parts. Compared to vacuum casting, it tends to be more expensive. Besides, vacuum casting is more suitable for early-stage development with a focus on aesthetics, while CNC machining is ideal for precise, high-tolerance parts in the medical device industry.
Conclusion
Vacuum casting for medical devices, nowadays, is widely regarded as a cost-effective and versatile choice to realize high-quality prototypes and flexible designs. No matter it involves creating joint replacements, dental implants, tubing connectors, or rapid prototyping, this method works smoothly and efficiently. It firmly keeps advancing technological progress and improving healthcare solutions.
Are you planning any new projects requiring vacuum cast parts? Simply upload your CAD files to TEAM Rapid Tooling’s Instant Quoting Engine and you will get a quote asap.