Manufacturing has been transformed by injection moulding, which makes it possible to create increasingly complicated materials accurately and effectively. Threaded injection molding components stand out among the many uses for injection molding as important products in a variety of sectors. This article explores the world of threaded injection molded parts, exploring their usefulness, applications and potential appeal for modern rapid manufacturing.
Table of Contents
- 1 Understanding Threadeded Injection Molded Parts
- 2 Applications Across Industries
- 3 Challenges and Considerations
- 4 In summary
Understanding Threadeded Injection Molded Parts
Threaded injection molded parts are amazing products that are produced by the injection molding process. Unlike traditional injection molded parts, threaded counterparts boast unique characteristics, defined primarily by lines or helical ridges on their surfaces. These lines add functionality, allowing these parts to touch various elements together in the object, if combined, and serve an important function. In injection molding, a liquid is injected into a mold cavity, forming a solid into the desired shape.
Thread molding parts take advantage of this process, adding threads seamlessly during manufacture. This not only simplifies the manufacturing process but also provides distinct advantages over conventional manufacturing methods. The main distinguishing characteristics of threaded parts are the combination of cost-effectiveness, manufacturing efficiency, and lightweight construction with exceptional durability. These features make threaded parts more attractive for many applications. Benefits of Threaded Injection Molded Parts
Threaded Injection Molded Parts is Cost efficiency
Reduced manufacturing costs:
Threaded injection molding reduces manufacturing costs by increasing efficiency. A simpler process allows faster manufacturing processes, reducing labor and energy costs. In addition, the high accuracy of injection molding reduces waste, contributing to a lower overall cost.
Making the most of the content:
Threaded parts generally require fewer materials than regular ones. The injection molding process ensures the best materials are used, reducing costs and environmental impact. This efficiency is especially useful in industries where materials are a major cost factor.
Threaded Injection Molded Parts can be Process flexibility
Complex Geometry:
The flexibility of injection molding enables intricate mold designs that would otherwise be difficult or impossible to manufacture with other manufacturing processes. This versatility opens up new possibilities for innovation in various industries.
Options available:
Threaded injection molding allows parts to be customized to specific requirements. Manufacturers can easily adjust yarn size, pitch, and geometry to meet the unique needs of different applications. This customization increases the flexibility of fiber products to suit different industries.
Threaded Injection Molded Parts can be Lightweight and Durable
Weight Reduction Advantages:
A favorable strength-to-weight ratio is typically exhibited by threaded components, which helps create materials that are both robust and lightweight. This is particularly crucial in sectors like automobile, aircraft, and others where weight loss may improve performance and fuel economy.
Durability in different conditions:
The durability of threaded injection molded parts is due to the inherent properties of the material and the precision achieved during manufacturing. These parts can withstand harsh environmental conditions, making them suitable for applications from consumer electronics to industrial devices.
Applications Across Industries
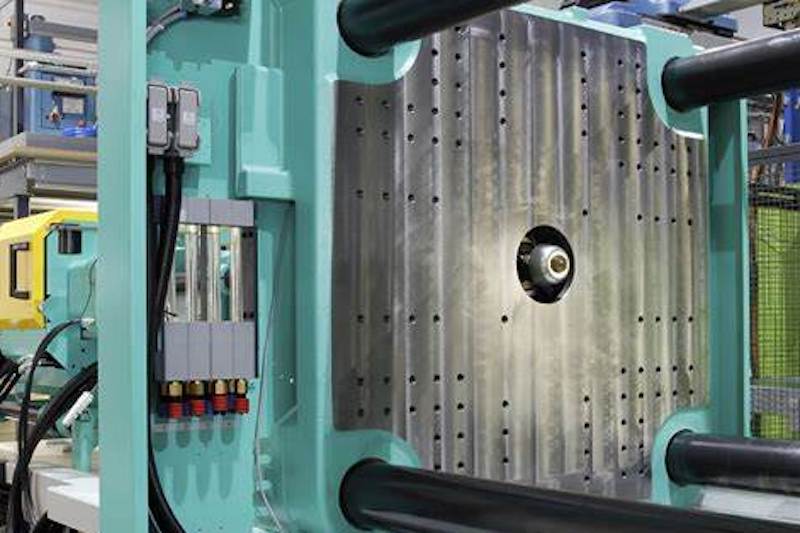
Automotive
Wired features in the car:
Threaded injection molded parts find applications in a variety of automotive components, such as dashboard assembly, interior trim, seating arrangements, and the ability to create complex and custom designs that contribute to the efficiency and aesthetics of vehicle design.
Applications under the hood:
Automakers use threaded injection molded parts on critical hood-under components, including engine mounts, cooling system elements, and electrical connectors. The combination of cost-effectiveness and durability makes these parts ideal for challenging traffic conditions.
Electronics
Threaded Parts of Consumer Electronics:
The electronics industry benefits from wireless parts in smartphones, laptops and wearable devices. The lightness of these parts is especially beneficial in handheld machines, contributing to the overall efficiency of the product.
Applications in industrial electronics:
In industrial settings, threaded parts play a role in electronic enclosure connectors and products that require safe and reliable bonding. The customization options offered by threaded molding govern technology to meet the specific needs of the products.
Medical
Threaded components in medical devices:
Specificity and customization are increasingly important in the medical industry, where threaded injection molded parts find use in medical devices such as pumps, connectors, diagnostic tools, etc. The ability to produce sterile and biocompatible parts makes them key to medical development.
Sterilization and Biocompatibility Considerations:
Mechanically wired parts must meet strict sterilization and biocompatibility standards. The inherent quality of the materials used in injection molding and the optimized manufacturing processes ensure that these parts meet the exacting requirements of the pharmaceutical industry.
Challenges and Considerations
While threaded plastic molding has many advantages, it has challenges. Producers must address potential issues such as yarn quality and equipment complexity and ensure consistent production. Strategies to overcome these challenges include improved equipment manufacturing techniques, quality assurance methods, and ongoing research to refine wiring efficiency.
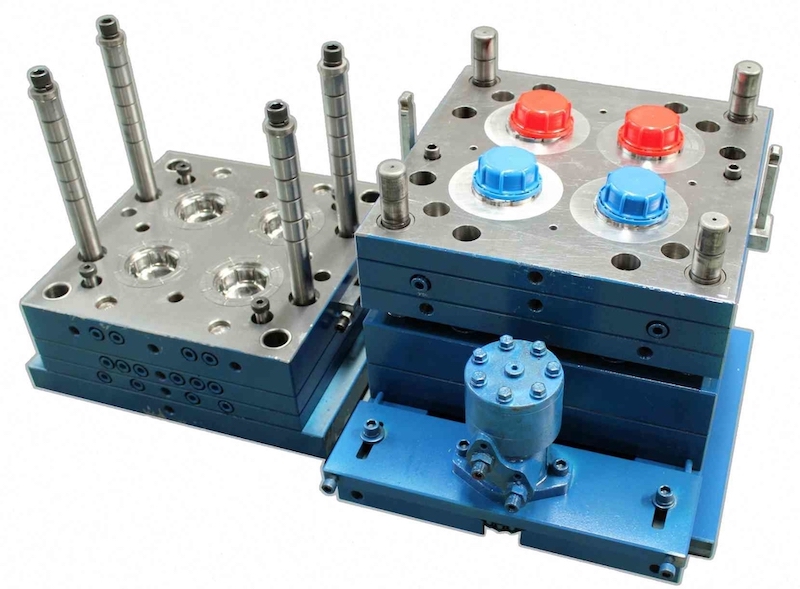
Quality control and testing play an important role in ensuring the reliability of injection molding parts. Rigorous testing for yarn integrity, material strength and design accuracy is essential to meet industry standards and deliver high-quality products to end users.
Case Studies
To demonstrate how spindles work in the real world, let’s look at two example scenarios.
Case Study 1: Seating Systems
To enhance performance and design, an automobile manufacturer included injection-molded cable portions into their seat systems. The overall weight of the chairs was boosted by the sturdy yet lightweight knotted material, which improved fuel efficiency. Customers may have a distinctive and cozy in-seat experience thanks to the customization choices that enable creative thread patterns.
Case Study 2: Parts of Medical Pumps
One producer in the medical device field has successfully produced pump components using threaded injection molded parts. The exacting molding process guaranteed the continuous thread quality, which is essential for safe connections in medical equipment. These threaded pieces are essential to the dependability of the pumps since the material’s sterilizing capabilities and biocompatibility satisfy the strict criteria of the medical profession.
In summary
In conclusion, threaded injection molded components provide a multitude of advantages and applications across sectors, hence representing a paradigm change in production. These components’ affordability, adaptability in design, and durability are essential to the state of production today. Threaded injection molding is expected to become increasingly more significant as technology develops, promoting sustainability and innovation in a variety of sectors. To open up new options and keep up with technological advancement, producers and designers alike must investigate the enormous potential of threaded spinning components.
Besides from injection molding, TEAM Rapid also offers rapid prototyping, CNC machining, and die casting to meet your projects needs. Contact our team today to request a free quote now!