Overmolding is recognized for its versatility and capacity to produce intricately designed parts that enhance both function and visual appeal. This method, which includes applying a new layer of material over an already molded piece. Requiring a deep insight into the unique needs of each component crafted. Among these requirements, the selection of compatible materials for overmolding is crucial. It is vital to choose materials for the base and the over-mold that align chemically and thermally. Neglecting to do so could have detrimental consequences, such as the product losing its functionality or getting distorted. Therefore, ensuring a high-quality and durable over-molding product requires careful overmolding materials’ selection. A thorough understanding of their properties and how they interact are needed.
Table of Contents
Overmolding Materials for the injection molding process
Overmolding stands as a key rapid manufacturing approach, enabling the production of parts that are both strong and consistent. Merging diverse materials opens the door to a wide array of material pairings for each component. The industry is rich with various resins, each offering unique benefits. Spanning from the robustness of polypropylene and polyethylene to the thermal endurance and security offered by silicone, a suitable resin exists for nearly every use, including the resilience and pliability provided by thermoplastic elastomers. Components can be engineered to improve longevity, weather resistance, or aesthetic attributes by carefully combining different materials. Owing to its adaptability, over-molding is extensively used in several industries, such as electronics, healthcare, and automotive, where the production of durable and superior components is essential.
What is achieved through overmolding materials?
Overmolding involves embedding a plastic or metal component within an additional mold at a second stage, where extra cavity space has been crafted. Into this space, a secondary molding substance, typically elastomeric though it can be rigid, is injected. This substance encases the initially clamped component, filling the new cavity and chemically bonding with the base material to form a unified piece. Almost any type of polymer is suitable for over-molding onto another object.
Commonly, thermoplastic rubbers and thermoplastic elastomers (TPR and TPE) are overlaid onto various grades of engineering and consumer plastics, enhancing aesthetics, providing shock resistance, or improving grip. For products demanding high ingress protection levels, such as those used in marine or outdoor settings, over-molding plays a critical role. It facilitates the creation of precise, high-pressure seals that maintain integrity during the engagement and sliding of casing components, overcoming the usual difficulties of fitting O-ring seals. While TPR and TPE are frequently used materials, alternatives like liquid silicone rubber molding or fluoroelastomers are also options for these applications.
Commonly Used Overmolding materials
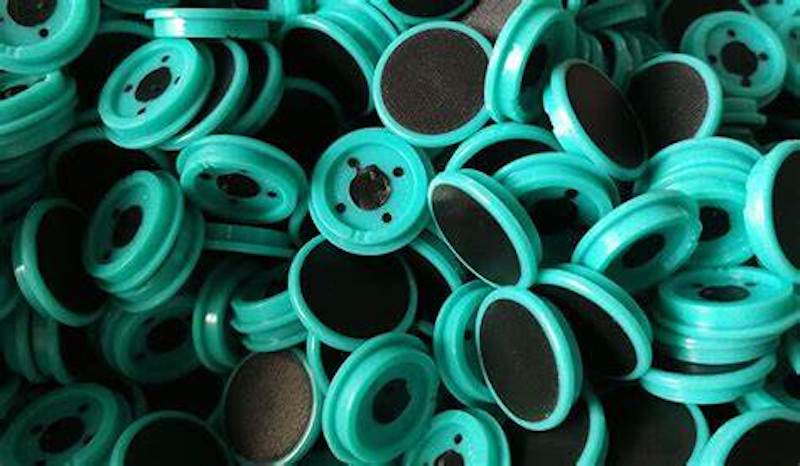
Acrylonitrile Butadiene Styrene (ABS)
Popular for consumer and automotive parts due to its compatibility with soft, elastomeric materials used for grips and seals. It often features mechanical engagement enhancements to secure the over-molded material, reducing reliance on chemical bonding.
Ovemolding materials: Polypropylene (PP)
A stable and flexible polymer used in disposable items and higher-grade consumer products. Advances in molding have enhanced its appeal, particularly for items like electric toothbrushes. Special TPEs have been developed to adhere to PP, overcoming its low surface energy challenges.
Low-Density Polyethylene (LDPE)
Known for applications in piping and food-grade equipment, LDPE’s low surface energy has historically limited over-molding. However, newer TPE variants have broadened their over-molding potential despite generally lacking in mechanical bond capabilities with metal.
Overmolding materials: Thermoplastic Elastomers (TPEs)
Although TPEs are a flexible class of elastomers that work well for over-molding, they can have adhesion and stability issues over time. They have several subtypes with distinct characteristics and uses, such as TPV, TPO, TPU, and TPS.
High-Density Polyethylene (HDPE)
Its chemical resistance and low surface energy complicate overmold adhesion. Surface treatments can improve adhesion for attaching parts, but HDPE is more commonly used for encapsulating metal parts through mechanical means.
overmolding materials: Polyoxymethylene (POM)
Shares many properties with HDPE, including low surface energy, making it unsuitable for dual polymer over-molding. However, it’s effective in overmolding injection molding metal parts due to its toughness.
Polyetherimide (PEI)
A high-performance polymer prized for its thermal, mechanical, and chemical properties. PEI excels in insert molding with metals, offering high strength and temperature resistance, and is often used in medical devices and scientific equipment.
The strength of overmolding materials
The performance of over-molded materials is determined by the choice of polymers. Flexible polymers like TPU, TPE, and TPR provide elasticity but are more prone to wear and are suited for impact-sensitive or soft-touch products. On the other hand, LSR and EPDM offer greater toughness and durability, which makes them ideal for harsh conditions.
Using hard or engineering-grade polymers in over-molding delivers parts with metal-like strength yet lighter and corrosion-resistant. This approach enhances durability, weather resistance, and appearance across sectors such as electronics, automotive, and healthcare. Effective over-molding relies on selecting materials with appropriate levels of toughness to ensure the production of durable, high-quality parts.
Overmolding materials’ life duration
Abrasion and material wear are two factors that affect the durability and strength of over-molded components. The material’s durability may be seriously compromised if it is subjected to elements that compromise its chemical integrity, such as UV radiation, oxidizing chemicals, or extremely high temperatures. Soft materials can have shorter usable lives because they are more likely to break, chip, and flake under stress. Reliance on mechanical connections may make these problems worse and reduce the over-molded parts’ operating durability even further.
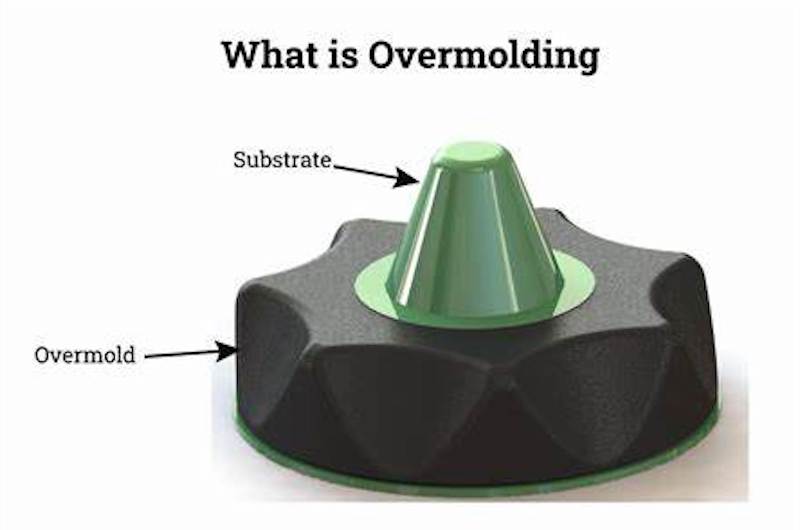
Conclusion
In summary, the choice of materials for over-molding is a complex process that strikes a balance between adaptability, robustness, and visual appeal to satisfy particular application needs. Each material offers a distinct advantage to the over-molding process, ranging from the pliability of ethylene propylene diene monomer (EPDM) and liquid silicone rubber (LSR) to the robustness of thermoplastic elastomers (TPE), polyurethanes (TPU), and thermoplastic rubbers (TPR). Advanced polymers are particularly valued for their combination of strength, lightweight properties, and corrosion resistance, offering a metal-like performance with additional advantages. This strategic choice of materials underpins the success of over-molding in key industries such as electronics, automotive, and healthcare, ensuring that the resulting components not only function optimally but also meet high standards of visual quality.
Besides from overmolding, TEAM Rapid also offers insert molding, injection molding, rapid prototyping, and die casting etc to meet your projects needs. Contact us today to request a free quote now.