Insert molding process innovatively blends metal and plastic, significantly bolstering the resilience and structural robustness of parts. This method entails encasing metal inserts in molten thermoplastic and is widely used in the consumer goods, sports equipment, aerospace, and defense industries. It makes use of plastic’s moldability and metal’s strength to create long-lasting, accurate components that are also lightweight. This method stands out for its contribution to streamlining production workflows and enabling the exploration of new design frontiers. Insert molding is a cornerstone technology in crafting sophisticated, durable products across an expanded range of applications.
Table of Contents
The insert molding process
Insert molding excels in merging varied materials into single, cohesive items, starting with the precise placement of metal inserts like brass or stainless steel within a mold / rapid tooling. These metals underpin the component’s durability. The crucial phase follows, where thermoplastic resin is injected to encase the inserts, solidifying it into a durable composite.
The selection of the thermoplastic resin is vital, influencing the final product’s attributes. Choices vary from durable nylon to tough polycarbonate and versatile polyethylene; each is picked for the specific benefits it brings, such as wear resistance or flexibility.
This process uniquely combines different materials to produce components that are not only strong but also customized to specific needs. Insert molding stands out for its ability to deliver specialized, robust parts efficiently, making it a key technique in advanced rapid manufacturing for producing intricate, multi-material designs.
Enhancing Product Strength with Insert Molding
Insert injection moulding offers a unique advantage in enhancing the structural robustness of manufactured products. This method integrates metal inserts into plastic components, significantly upgrading their mechanical capabilities. The inclusion of these metal inserts—a process at the heart of insert molding—directly contributes to a notable increase in the tensile strength of the final product. Tensile strength, a critical measure of a material’s ability to withstand pulling forces, becomes especially vital for parts that will face rigorous use or mechanical stress in their application environment.
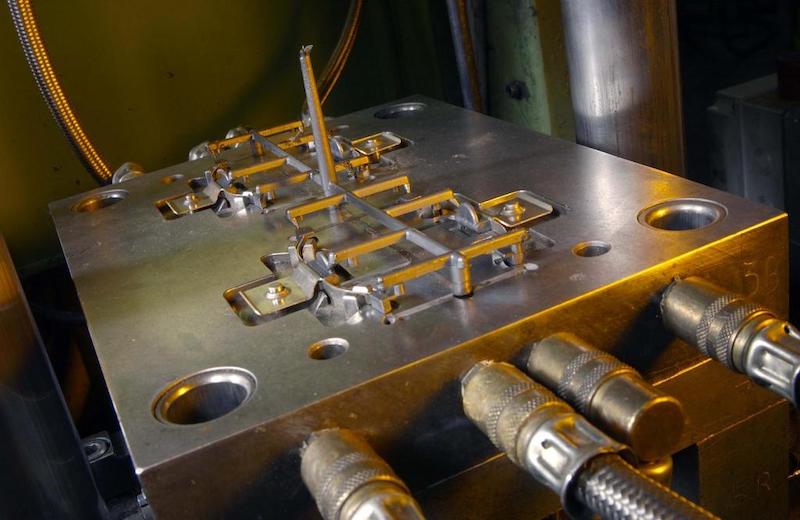
Beyond tensile strength, insert molding also elevates the load-bearing capacity of components. This attribute is essential for parts that must support weight or endure pressure without compromising integrity or performance. The ability to sustain such stresses makes insert-molded products indispensable in fields where failure could result in significant consequences, including automotive engineering, construction, and heavy machinery.
A key component of this procedure is the interaction between metal implants and thermoplastics.
Not every combination of metal and plastic works well together, so it’s critical to select complementary materials. For airplane applications, where weight is an important consideration, a robust and lightweight part manufactured of high-impact thermoplastic with aluminum inserts is perfect. An alternative would be to combine heat-resistant thermoplastic with stainless steel inserts for parts that are exposed to high temperatures, such as those in industrial or kitchen appliances.
This deliberate choice of materials not only guarantees the component’s structural integrity but also customizes it to fulfill the unique requirements of its intended application. Insert molding pushes the envelope in terms of product design and usefulness by maximizing the interaction between metal and plastic to create products that are tougher and better suited to difficult applications.
Enhancing product durability with insert molding
One of the most important methods for increasing the durability and toughness of manufactured goods is insert molding. Products can be effectively protected by this technology from a wide range of environmental dangers, such as strong chemicals, caustic compounds, and extreme temperature variations. The basic procedure, which encases metal inserts in a strong thermoplastic shell, creates a strong barrier that keeps the core material out of direct contact with these harmful elements. Even in situations that are renowned for being difficult, this protective layer is essential in maintaining the component’s structural integrity and functional capabilities.
The remarkable resilience of insert-molded items against wear and strain adds to their lasting quality. Many materials can eventually deteriorate due to frequent use and the physical stress that follows, necessitating replacement. Nevertheless, insert molding’s clever use of plastic and metal produces a synergy that dramatically lowers this risk. When the intrinsic strength of the metal insert is paired with the thermoplastic’s resistance to deformation, the composite material becomes much more resilient to repeated pressures than any of its constituent parts could.
Moreover, the bond that is formed between the metal insert and the thermoplastic matrix during the molding process is of paramount importance.
This bond is not merely a physical entanglement but a fusion that locks the materials together at a molecular level, enhancing the unity of the component. Such a bond is crucial for ensuring that the insert does not become dislodged or weakened over time, thereby maintaining the structural integrity and functionality of the part throughout its lifecycle.
This increased durability is extremely beneficial for a wide range of uses. For example, corrosion resistance and high-temperature tolerance are critical components for the longevity and safety of automobiles in the automotive industry. Medical device equipment’s durability ensures that it won’t break down under pressure or require sterilizing. Comparably, resistance to wear and environmental conditions increases the lifespan of consumer electronics, meeting consumer demands for dependability and sustainability.
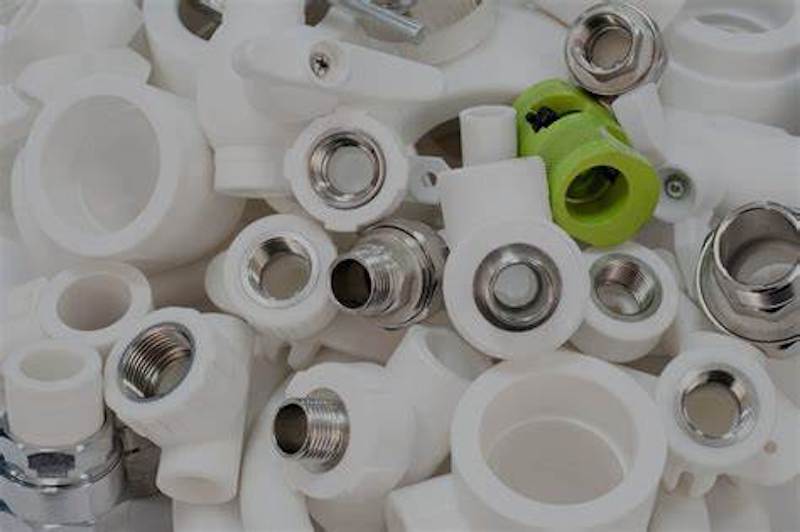
In essence, insert molding not only enriches product strength but also significantly extends the usable life of components by providing unmatched protection against environmental and mechanical degradation. This contributes immeasurably to the value and reliability of products in demanding industries, affirming insert molding’s role as a cornerstone of durable, high-performance low volume manufacturing and mass production.
Conclusion
To sum up, insert molding is a revolutionary manufacturing technique that is essential to creating components with exceptional strength and longevity. Through the clever integration of metal inserts with thermoplastic materials, a synergistic effect is achieved that improves the goods’ mechanical qualities and environmental resilience. The elements are fortified against corrosion, temperature fluctuations, and chemical exposure, and their tensile strength and load-bearing capability are heightened by this process.
The result is a generation of parts that are more reliable and have lengthier lifespans, which is pivotal for satisfying the stringent specifications of many industries, such as the automotive, medical, and electronics sectors. Therefore, insert molding is a monument to the unrelenting quest for innovation in manufacturing, providing a means of producing goods that are not only more durable but also customized to satisfy changing consumer demands in a dynamic marketplace.
Contact TEAM Rapid today for insert molding, rapid prototyping, CNC machining, and die casting!