Process of die casting is an advanced manufacturing technique where a high-pressure mold, known as a “die,” is employed to make intricate metal components, often referred to as “casts.” These casts stand out for their precision and uniformity. Predominantly, this method utilizes non-ferrous metals, meaning they lack iron content, including but not limited to aluminum, zinc, magnesium, and copper.
This process finds its application across a diverse range of sectors, producing parts that are ready for assembly or direct consumer use. Die casting shares a resemblance with injection molding; however, the latter process involves the use of molten plastic instead of metal, distinguishing the two in their material application but linking them in their foundational approach.
Table of Contents
Spaces die casting is utilized currently.
Die casting has transformed into an essential, flexible manufacturing process that is pivotal for various sectors. It’s fundamental in creating durable components for heavy machinery and construction vehicles, including hydraulic systems and frames, supporting the surge in renewable energy by manufacturing vital parts for wind turbines, solar panels, and energy storage.
In consumer markets, it’s behind the robust and visually appealing metal parts found in household appliances such as refrigerators and coffee machines. Moreover, in the recreation sector, it crafts lightweight yet strong components for sports equipment like bike frames and fitness machines. This evolution underscores die casting’s critical role in pushing forward the manufacturing domain, proving it a cornerstone for producing efficient, innovative, and attractive industrial solutions.
How the process of die casting is performed
Die casting is executed through a carefully structured six-phase process designed to fabricate precise and high-quality metal components. Let’s examine each segment of the die-casting workflow.
Mold Creation
The process initiates with the creation of a custom mold from a non-ferrous material. This mold/rapid tooling is engineered with exacting precision to mirror the specifications of the target component, setting the foundation for the entire casting process.
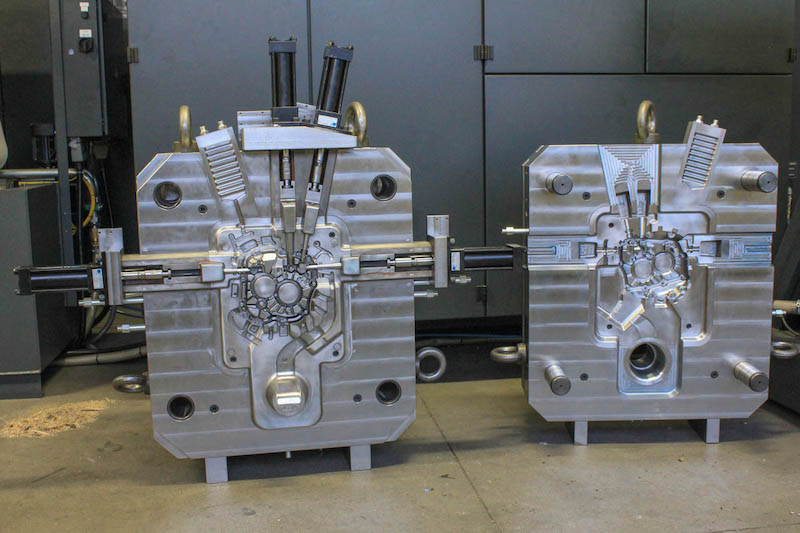
Mold Setup
To ensure a smooth casting process, the mold is first treated with a lubricant to prevent the molten metal from sticking. It’s then securely fastened shut, preparing it for the introduction of metal.
Metal Injection
During this critical phase, molten metal is propelled into the mold under high pressure through a die-casting machine. This ensures the metal spreads uniformly throughout the mold, capturing the intricate details of the desired shape.
Solidification
After injection, the mold undergoes a cooling period. The molten metal is quickly solidified by a sophisticated cooling system, which enables it to precisely conform to the complex mold features.
Component Removal
The molding cycle ends after the metal has been completely set, at which point the mold is opened, and the formed part is carefully removed using ejector pins.
Refinement
To improve its quality and look, the freshly cast part goes through several finishing procedures. This includes trimming off any excess material, polishing for smoothness, and possibly applying a protective layer, making the part ready for its final application.
This streamlined process ensures die casting is an efficient and accurate method for rapid manufacturing metal parts, catering to diverse industrial needs with precision and quality output.
The process of designing a mold for die casting
Mold design for die casting involves critical considerations to ensure the quality and integrity of the cast parts. Key factors include managing wall thickness for uniformity and optimal performance, implementing draft angles between one to three degrees to facilitate easy removal of the cast without damage, and rounding off sharp edges to prevent stress concentrations and potential cracking.
Additionally, minimizing or avoiding undercuts can simplify the ejection process while carefully designing the parting line to ensure it doesn’t compromise the part’s critical features. Gate placement is vital for achieving even filling and reducing turbulence during the casting process. Ejector pin locations must be strategically chosen to prevent damage to the final product. Lastly, the mold’s surface finish plays a significant role in determining the cast’s surface quality, with smoother finishes leading to fewer defects and enhanced appearance. These guidelines help in creating efficient and reliable molds for die casting.
Pros and cons of using die casting
Die casting presents several advantages, making it a cost-effective choice for low volume manufacturing to mass production with its capability to produce parts at a lower labor cost due to semi or fully-automated processes. It excels in creating intricate forms and complex shapes, accommodating part sizes from 25g to 25 kg, and can achieve walls as thin as 0.38 mm thanks to the high pressure applied during casting. This process yields parts with fine-grained, hard outer skin that enhances strength, especially as wall thickness is reduced, improving the strength-to-weight ratio.
Die casting also achieves smooth surfaces ideal for bearings and produces shape products with minimal post-processing needed, boasting excellent dimensional accuracy and surface finishes between 0.8-3.2 um Ra. Additionally, it allows for the efficient manufacturing of smaller pieces through multi-cavity or miniature die-casting techniques.
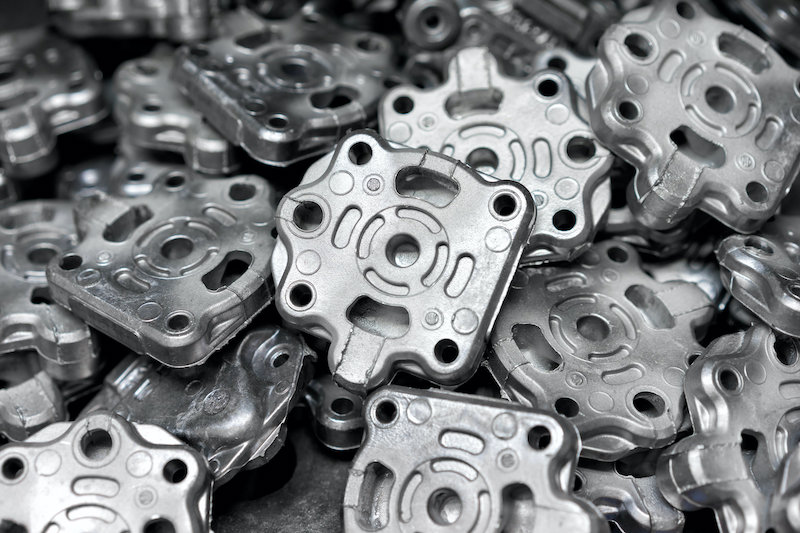
However, die casting comes with its set of disadvantages, notably being economically viable only for large-scale production runs due to the high initial equipment costs. It is not suited for high melting point metals and alloys, nor for ferrous metals like stainless steel, carbon steel, and alloy steel, which are prone to rusting.
The process also faces limitations in casting large pieces, incurs high die costs, and has a generally lengthy lead time. Modifications to part designs can be costly and time-consuming, emphasizing the importance of prototyping before full-scale production. Lastly, porosity issues arising from trapped air and gases can compromise part integrity, although vacuum die casting offers a solution by reducing porosity through the creation of a vacuum before the metal fill.
Conclusion
In summary, the die-casting technique is a unique way to produce metal parts that combine speed, consistency, and diversity. It is also incredibly accurate and efficient. From the design of the mold to the last post-processing, every step is painstakingly planned to ensure that complicated forms and details are created with exceptional strength and accuracy. Die casting is an invaluable technique in many industries despite its challenges with high initial costs, limited material availability, and rigid design. Other benefits include cost-effectiveness in high-volume production, excellent surface finishes, and the ability to produce parts with little post-processing. Die casting’s capabilities and applications will grow with technology, guaranteeing its position as a key component of contemporary production.
Besides from die casting, TEAM Rapid also offers rapid prototyping, CNC machining, and injection molding to meet your projects needs. Contact us today!