The rule of thumb for sheet metal design encapsulates a comprehensive collection of guidelines and best practices specifically tailored to streamline the design phase, guaranteeing that the sheet metal fabrication parts from sheet metal are not only manufacturable but also functional and economically viable. This abundance of information, condensed into simple-to-apply concepts, considers the nuances and variations present in various materials, applications, and rapid manufacturing processes.
These broad considerations include things like material selection, which is crucial in determining how long a part will last and whether it is appropriate for its intended use; intricate design details that affect assembly and manufacturing; and cost considerations that guarantee the project stays within budget without sacrificing quality.
Table of Contents
These Sheet Metal Design flexible rules are as follows
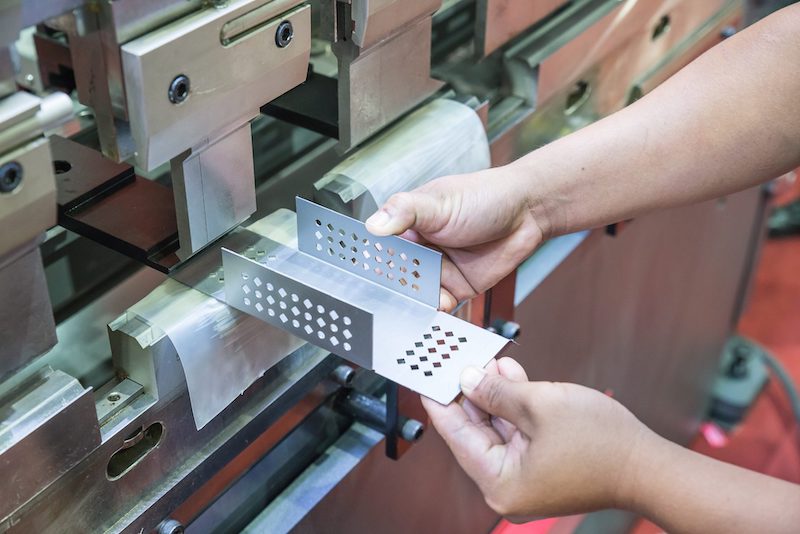
Minimum Bend Radius
The principle of the minimum bend radius is vital in sheet metal fabrication to prevent material cracking or failure during bending. This guideline suggests that the bend radius should at least equal the sheet metal’s thickness to preserve the product’s structural integrity. However, this is a basic guideline, and the ideal bend radius varies with the material’s properties and the bending technique. Greater ductility materials, like some grades of aluminum, can withstand a lower sheet metal bending radius without stress fractures, but more brittle materials need to be handled carefully. The endurance and dependability of the final product are dependent on carefully weighing material limits, usefulness, and aesthetics when determining the right bend radius.
Hole Diameter In Sheet Metal Design
When incorporating holes into sheet metal designs, it’s crucial to balance the hole diameter with the sheet metal’s thickness. Following the principle that the hole diameter should at least match the metal’s thickness prevents material stress and deformation, preserving the part’s structural integrity and mechanical properties. Although material characteristics like tensile strength and hardness can slightly modify this rule, adhering to this ratio ensures a harmonious balance between the material’s capabilities and the design’s functional demands. Accurate control of hole diameter is vital for the part’s durability, especially if it will face additional processing or mechanical stress.
Hole Placement
The strategic positioning of holes within a sheet metal part is just as critical as their size. Ensuring that holes are placed a safe distance from the material’s edge — typically recommended to be at least 1.5 times the material thickness — is crucial for maintaining the sheet’s structural integrity and preventing edge distortion.
This precaution helps distribute stresses more evenly across the material, reducing the risk of creating weak points prone to cracking or tearing, especially during subsequent manufacturing processes like bending or welding. Moreover, thoughtful hole placement can enhance the aesthetic quality of the final piece while optimizing its functional performance. This guideline requires designers to thoughtfully navigate the constraints of material behavior and manufacturing capabilities, leading to the creation of robust and reliable sheet metal parts.
Notches and Cutouts in Sheet Metal Design
In sheet metal design, positioning notches and cutouts correctly is crucial to preserve material integrity. These features must be placed at a distance greater than the material’s thickness from any edge or other features to avoid structural weakening. This approach ensures stress is evenly distributed, reducing failure risk. The size of these elements should also facilitate manufacturing while ensuring durability, balancing aesthetic and practical considerations effectively.
Flange Width
Flanges enhance sheet metal parts by increasing stiffness and providing reliable attachment points. Their width should be at least four times the material thickness to allow for proper forming and functionality, contributing to the part’s structural integrity and resilience. Early consideration of flange width is vital for optimizing part performance and durability.
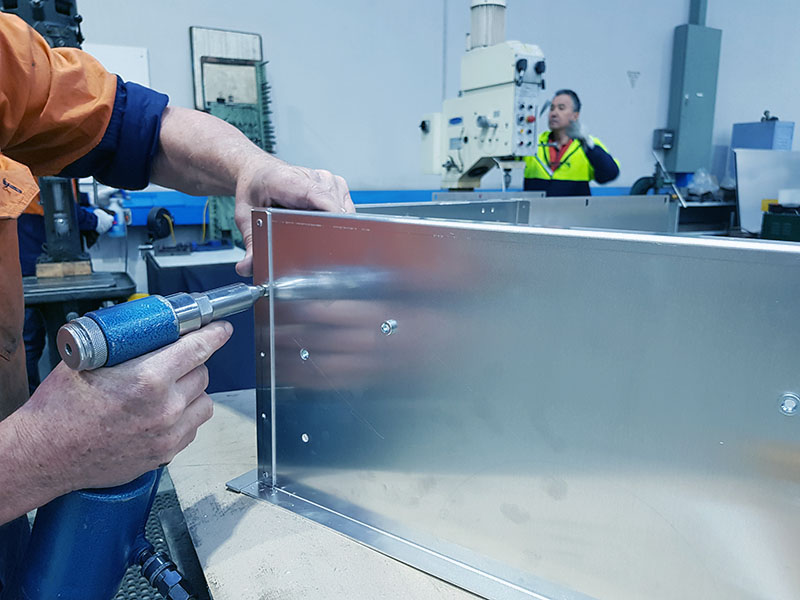
Bend Relief in Sheet Metal design
Adding bend relief cuts near sheet metal edges prevents tearing during bending. The size of these cuts should align with the material thickness or bend radius, allowing for adequate metal stretching. This design choice is essential for clean bends and maintaining material integrity, highlighting the importance of precise bend relief implementation.
Welding Considerations
Welding requires careful joint design, tool access, and consideration for weld shrinkage to achieve strong, consistent welds without distortion. Addressing these factors ensures the welded part meets all specifications and maintains its structural and functional integrity. Appropriate weld selection and joint design are key for optimal results.
Material Selection in sheet Metal Design
Choosing the right material is fundamental, affecting design parameters like bend radius and finish. Material properties, such as strength and corrosion resistance, determine its application suitability. Proper material selection balances performance with cost, ensuring the part meets operational demands efficiently. Matching material properties with application needs is crucial for project success.
The genera Sheet Metal Design rules of thumb
In sheet metal design, the “Rule of Sixes” serves as a pivotal guideline, particularly for bending operations. This rule advocates for a minimum bend radius, bend relief width, and bend distance, each being six times the material thickness. By adhering to this rule, designers can ensure that sheet metal parts are both structurally sound and capable of withstanding the stresses imparted during bending processes. The emphasis on uniform multiples of the material thickness across these three key areas simplifies the design approach, facilitating more reliable and consistent manufacturing outcomes. This rule exemplifies how strategic guidelines can significantly influence the quality and durability of fabricated metal parts, ensuring they meet the required specifications and performance standards.
Following the rule of thumb for sheet metal design is crucial for multiple reasons
- Manufacturability: These guidelines ensure designs are ready for efficient production, minimizing issues like incorrect part assembly or shape achievement failures.
- Material Efficiency: Adhering to recommended specifications for bend radii and hole sizes helps reduce waste and use materials more effectively, lowering costs and supporting sustainability.
- Functionality: These rules maintain part integrity and functionality, preventing issues such as material cracking or deformation and ensuring parts perform as expected.
- Aesthetics: Proper design practices enhance the visual quality of parts, avoiding defects like uneven bends and contributing to a polished final product.
- Durability: Considering material choice and joint design improves part longevity and resistance to environmental factors, leading to greater customer satisfaction.
- Cost Reduction: By streamlining manufacturing processes and minimizing waste, these practices can lower production expenses.
- Streamlined Prototyping: Following these principles simplifies the rapid prototyping and revision process, helping to quickly identify and address design issues and speeding up time to market.
Conclusion
In conclusion, the rule of thumb for sheet metal design provides essential best practices and guidelines that ensure sheet metal parts are manufacturable, functional, and cost-effective. Including principles like the “Rule of Sixes,” these guidelines give designers a solid framework for tackling the challenges of material selection, bending, and placement of notches and cutouts. Following these principles helps optimize product durability, appearance, and manufacturing efficiency. These rules are fundamental in producing durable, high-quality sheet metal components suitable for various applications.
Besides from sheet metal parts fabrication, TEAM Rapid also offer CNC machining, injection molding, and die casting to meet your low to high volume production needs. Contact us today to request a free quote now!