Shrinkage is a big nightmare for any vacuum casting production. This problem can cause product defects that are difficult to repair. The bigger the shrinks, the more it will become irreparable. Irreparable product defects cannot go to the next phase in your production cycle. It is imperative to stop the shrinkage from happening in your vacuum casting production. It can help improve the overall product quality you make. No shrinkage also means a better and easier assembly process for your casted product. How can I reduce shrinkage of vacuum casting?
Table of Contents
- 1 Let’s delve deeper into how to reduce shrinkage of vacuum casting.
- 1.1 Reduce Casting Temperature
- 1.2 Reduce Shrinkage of vacuum casting: Rigid and Strong Molds
- 1.3 Avoid Thin Walls
- 1.4 Reduce Shrinkage of Vacuum Casting: Utilize 3D Scaling
- 1.5 Create Enough Ventilation
- 1.6 Reduce Shrinkage of Vacuum Casting: Adjust the Feeding System
- 1.7 Improve the Mold Design
- 1.8 Optimize the Liquid Material Flow
- 2 Conclusion
- 3 Vacuum Casting Services with Team Rapid Tooling
Let’s delve deeper into how to reduce shrinkage of vacuum casting.
Reduce Casting Temperature
Temperature problems are one of the most common causes of shrinkage in vacuum casting. Unstable temperatures during the casting process can increase the chance of porosity and shrinkage. Reducing and stabilizing the casting temperature is the best way to prevent casting shrinkage.
You need to adjust various aspects of the casting chamber to get the best result. Installing cooling ribs can help prevent overheating inside the casting chamber. It will, in turn, help reduce the shrinkage during the casting process.
Reduce Shrinkage of vacuum casting: Rigid and Strong Molds
The mold rigidity and strength can also affect the quality of the casted products. Mold rigidity can also determine whether you might create porosity on the casted products. The reason is that a rigid mold can give you solid and stable casting processes inside the casting chamber. It builds a perfect balance that prevents shrinkage from happening.
Rigid molds will also prevent unnecessary movements of the mold walls during casting solidification. It creates a stable casting chamber that can maintain the dimensional stability of the casted products without shrinkage.
Avoid Thin Walls
Thin walls are great recipes for disasters in your casting process. Add more thin walls to your casting chambers, and you can get more porosity in your casted products. Thin walls can be unstable and might contribute to deformations of your casted products. It can also spread uneven hot temperatures around the casting chamber.
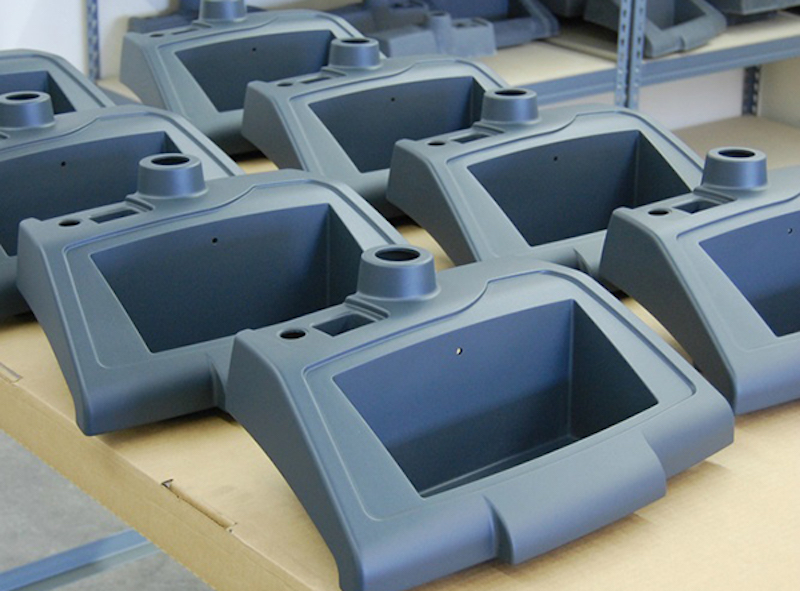
Use high carbon content when using thin walls in your casting mold design. It can help reduce the potential shrinkage and porosity in your casted products.
Reduce Shrinkage of Vacuum Casting: Utilize 3D Scaling
The good news about 3D Autocad is that you can use 3D scaling to enlarge your tool size. It is a great feature to help reduce the amount of porosity and shrinkage in your casted products. You can use 3D scaling to enlarge the tool size a bit. As a result, the tool for casting will be able to withstand the hot temperature throughout the casting process.
Calculate the tool scaling to a certain percentage to help you get into the sweet spot where shrinkage can disappear.
Create Enough Ventilation
Enough ventilation in your casting chamber can help boost the air circulation inside. It results in a more stable temperature control for the mold. A stable temperature control can help minimize the instances of porosity and shrinkage. Without an excellent ventilation system, shrinkage can happen because of overheating inside the casting chamber.
Optimizing the ventilation system can also help dissipate heat during the solidification process. It can reduce the porosity level down to its absolute minimum.
Reduce Shrinkage of Vacuum Casting: Adjust the Feeding System
Adjusting and optimizing the feeding system of the casting mold can help ease the solidification process. During solidification, a proper feeding system can give your casted product a constant flow of molten materials. The appropriate flow of casting materials can help you to create a more effective solidification.
Optimizing the feeding system and risers can minimize the instances of porosity and shrinkage for the casted products. It can also improve the casting mold quality to maintain the best dimensional stability for the casted products.
Improve the Mold Design
Shrinkage and porosity can happen because of a poor mold design. A poor mold design will affect the overall function of the mold during the casting process. Unstable liquid metal flow and inconsistent heat dissipation can create problems with the casted products. Shrinkage is one commonplace problem that can happen during the casting process.
It’s best to review your mold design before proceeding with the casting process for the final product. Create mold rapid prototypes and determine the best design for your mold based on your product shape. Improve your mold design until you can reduce the shrinkage possibility to a minimum.
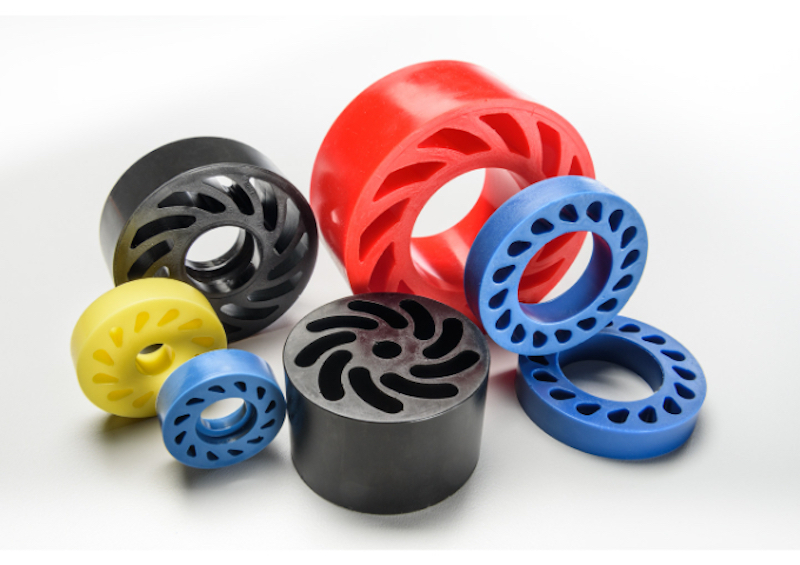
Optimize the Liquid Material Flow
One key to solving the shrinkage problem during casting is in the liquid metal flow. Optimizing the liquid metal flow can help the solidification process of the casted metals. With it, you can also ensure no shrinkage can happen during the solidification process. You can optimize the liquid metal flow in various ways.
Fixing the gating system for the casting mold is one way to optimize the liquid material flows to reduce shrinkage. Another way to reduce the shrinkage is to optimize the temperature within the casting chamber. Note that a higher percentage of shrinkage can happen when the liquid material flow gets stuck during the rapid manufacturing process.
Conclusion
One of the commonplace reasons for product failure in vacuum casting is shrinkage and porosity. In manufacturing, it’s always best for you to reduce shrinkage during the casting process. You can follow the tips explained in this guide to minimize the shrinkage occurrences in your vacuum casting production. Always check the mold and casting chamber design in your vacuum casting production. It can help you optimize various aspects of your vacuum casting process to minimize shrinkage and porosity. As a result, you can make perfect casted products that meet all your production standards and requirements(such as finish SPI standard).
Vacuum Casting Services with Team Rapid Tooling
Team Rapid Tooling provides vacuum casting services to meet your industrial requirements. We offer various materials for the vacuum casting process, including ABS like and PC like. You can determine the deadline for the production. We can meet your production timeline in the best way. Contact our sales team to get the best quote for your order. You can reach out to us by accessing https://www.teamrapidtooling.com/contact_us.html today.