Surface treatment is an important step in the aluminum die casting process, as it can improve your aluminum die casting parts and add more properties to it. With the treatment, you can give various other benefits to your aluminum casting parts, such as better corrosion resistance, better aesthetics, better durability, and many others.
There are various surface treatment procedures you can use to enhance the die casting for industrial components properties. In this guide, you will learn about the guidelines for treatment on aluminum die casting parts.
Table of Contents
Do You Need to Apply Surface Treatment on Aluminum Die Casting Parts?
In most cases, yes, you will need to apply surface treatment on the aluminum die casting parts you produce. It often becomes a necessary step in the die casting process itself, in which you will need to apply treatment as an additional procedure to complete before finishing your production process.
Surface treatment on aluminum die casting parts can come in various types, depending on various factors, such as the materials, equipment, costs, and the benefits you want to get. Also, each treatment process will have different procedures, which can provide you with a variety of advantages for your aluminum die casting parts.
Surface Treatment Guidelines for Aluminum Die Casting Parts
There are various surface treatment procedures you can follow, and depending on the benefits you would like to get, you can choose between 4 primary treatment procedures, which are chrome plating, anodization, electroplating, and powder coating. Each will have different processes you will need to follow, with their own set of equipment and materials to use. Here are the surface treatment guidelines you can follow for aluminum die casting parts:
●Chrome Plating Surface treatment Guidelines.
For the chrome plating process, first you will need to clean the aluminum die casting parts until there is no more grease or dirt on the surface of these parts. Then, you will need to put the rapid prototypes and parts into the chrome plating equipment and heat the equipment to a soluble temperature. Next, you will need to start the electric currents on the chrome plating equipment, waiting for the chrome materials to plate the surface of the aluminum and zinc die casting parts. Depending on your thickness goal, you might need to wait longer for the chrome plating process to complete.
●Anodization Guidelines.
What is anodizing aluminum? Anodization will require the cleaning process at first, so you will need to clean the aluminum die casting parts from all the impurities that might hinder the anodization process. Next, you will need to put the parts into the anodization equipment, which will contain an electrolytic bath. After putting the aluminum casting parts there, you will need to apply the electrical current to the electrolytic equipment, so that the anodization process can happen. It will allow you to cover the surface of the aluminum die casting parts with the oxide layer to increase its corrosion-resistant properties.
●Electroplating surface treatment Guidelines.
For electroplating, you will need to place your metal material of choice to electroplate the aluminum die casting parts inside the electroplating equipment, and you will need to use this metal as the anode. Then, you will use the aluminum sheet metalwork die casting parts as the cathode. Now, you will need to put both the metal and aluminum parts in the electroplating equipment, which you can then give the electric currents into. The electroplating process will begin, and the metal you choose will cover the surface layer of the aluminum die casting parts.
●Powder Coating Guidelines.
You will need to pick between thermoplastic and thermoset materials for powder coating and then prepare it for application on the aluminum die casting parts. You will need to prepare the powder coating materials by heat curing them using a specific spray gun for this process. Applying the powder coating materials on the aluminum die casting parts is quite simple, as you only need to use the spray gun to spray the powder coating materials on the aluminum surface and let it dry.
Benefits of Applying Surface Treatment for Aluminum Die Casting Parts
There are plenty of benefits you can get when you apply surface treatment on aluminum die casting parts, so make sure that you pick the surface treatment procedure that is most suitable for your parts. Here are some benefits of applying surface treatment for aluminum die casting parts:
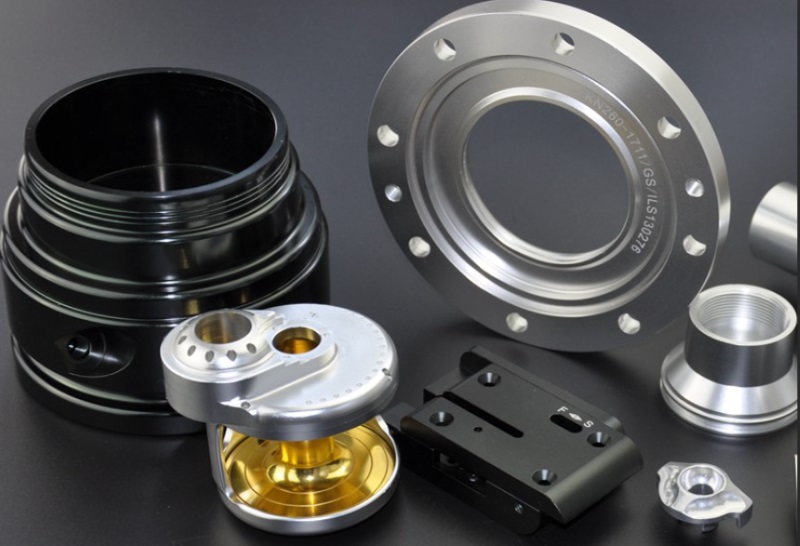
●Better product durability and lifespan.
The most common benefit of surface treatment is that it can provide you with better product durability and lifespan, meaning that the entire rapid manufacturing aluminum parts will become much rougher and more difficult to break, and you can also use them for the long term without worrying about breaking the aluminum die casting parts in the process.
●Better aesthetics and functionality.
The treatment will also provide the aluminum die casting parts with better aesthetics, so it will be great for decorative purposes. If you plan to use the die casting parts outdoors, the better aesthetics can make it have a more pleasant look. Also, the treatment can provide better functionality for your aluminum die casting parts while minimizing technical problems when you use them.
●Improved electrical conductivity and heat transfer.
In some surface treatment processes, you can also improve the electrical conductivity and heat transfer capability of the die casting parts. So, the parts that have undergone the surface treatment process will become more fitting to use in the applications that require higher electrical conductivity and heat transfer capability.
●Improved corrosion resistance and resistance against regular wear and tear.
Surface treatment will also provide better corrosion resistance for the aluminum die casting parts. Also, after applying the surface treatment process, the aluminum die casting parts will become more resistant against regular wear and tear, preserving the smoothness of the aluminum surface much better.
Conclusion
With various surface treatment options, you can improve the quality of your aluminum die casting parts depending on the benefits you want to get. One treatment procedure might be more expensive than the others, so you will need to factor in the budget you have to undergo the whole surface treatment process. For instance, with electroplating, different materials will also give you different costs, and higher costs will often bring you better results. So, it’s best to calculate the overall costs of the surface treatment procedure beforehand.
TEAM Rapid offers a series post treatment services to meet your needs of 3D print services, CNC machining services, plastic injection molding services needs. Contact our team today to request a free quote now!