Selecting the proper mold type for injection molding is of the utmost importance for effective and inexpensive manufacturing operations. Multi-cavity molds and family molds are two common mold types you can use to boost your production results. While both multi-cavity and family molds have their benefits as well as downsides, the most ideal mold type to use is not entirely set in stone, as there are a variety of aspects you need to consider, such as potential part defects, production capacity, tooling expenses, and the mold design analysis for flexibility requirements.
Table of Contents
Understanding mold type of Multi-Cavity Molds
The plastic multi-cavity molds are the mold type used to create multiple components, parts, or products in a single production cycle. It consists of multiple mold cavities or hollow chambers, each of which contains different cavity shapes for parts of similar design. Before deciding to use multi-cavity molds, you can consider these aspects:
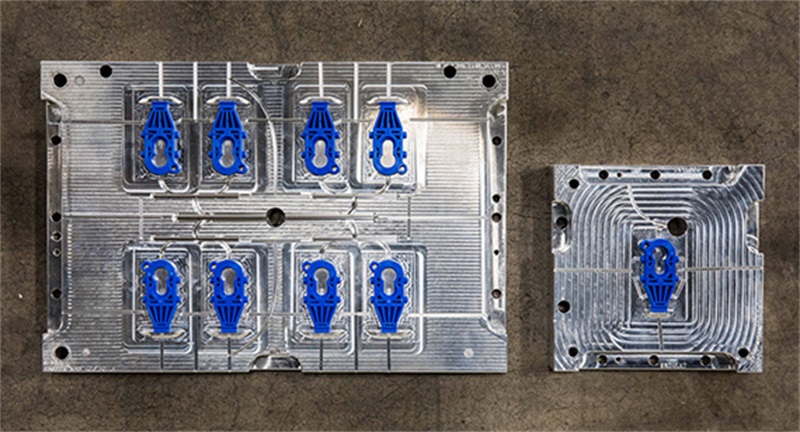
●The Characteristics of the Final Products You Make
When the parts being manufactured have the same or equivalent dimensions, forms, and requirements, multi-cavity molds will be appropriate for you to use. If the components you are making are simple and identical, multi-cavity molds can offer greater efficiency because they can produce many components at the same time.
●Production Volume
Multi-cavity molds will become very useful when a massive volume of similar components is required in your rapid manufacturing production. The multiple parts production offered by this mold type substantially improves manufacturing efficiency, decreases cycle time, and prevents wasteful resource usage.
●Costs
It is crucial to remember that multi-cavity molds usually involve elaborate tooling and have higher startup costs. These molds’ tooling procedures can be very complicated, as it demands precise engineering and tighter tolerances. The higher initial tooling costs, however, will give you the benefits in higher production output and decreased cycle time.
●Tooling Time
Multi-cavity molds will need extra tooling time for its design, production, and certification due to their degree of complexity. The increased complexity demands precise attention to some particular aspects, which may cause the development phase to take longer. If time is your concern, it is vital to consider the tooling time required to get these multi-cavity molds ready for production.
Understanding mold type of Family Molds
Another approach in improving your plastic injection molding production can be done by using family molds, also known as combination molds, which allow the creation of different but connected components in a single molding process. Family molds have multiple cavities, each of which contributes to making different sections of a single part. Before using the family molds, take consideration of the following aspects:
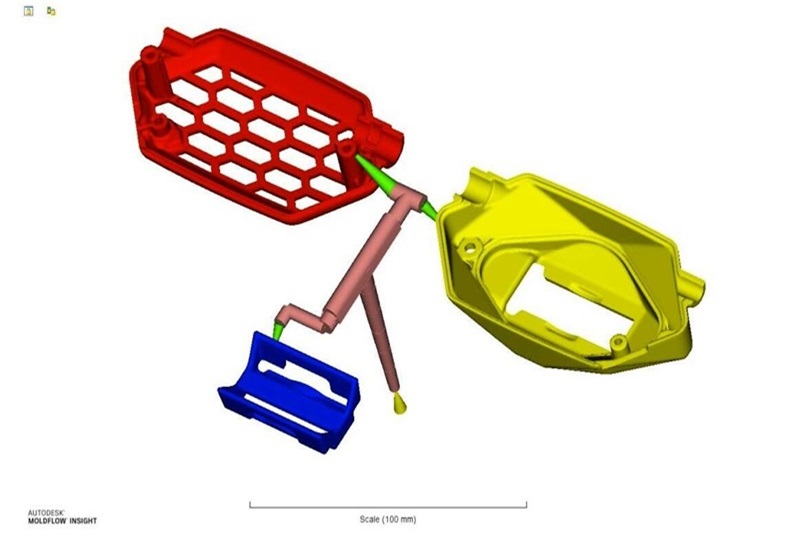
●Part Variants
When you manufacture different items that have comparable features or materials but with slight alterations to structure, size, or other properties, family molds are
the best selection. Family molds can provide the best flexibility and cost efficiency in your production by allowing the creation of a broad range of parts in a single molding process.
●The Quantity of Production in this mold type
Although family molds support the creation of different part layouts, this mold type is typically more appropriate for low to medium production volume. The level of details of the family molds and the complexity of the manufacturing process will rise as you add more segments into the molds. Consequently, multi-cavity molds will be more suitable for high-volume manufacturing, whereas family molds will suit more for lower or medium production volume.
●Costs of Manufacturing and Tooling for this mold type
When you need to create several associated components, family molds can help you save money on the tooling and production expenses. Compared to manufacturing individual molds for all of the components, the overall costs needed for rapid tooling, molds, and production can be reduced considerably by using family molds.
Key Elements for Picking the Most Ideal Mold Type
When you choose between the multi-cavity molds and family molds, it is better to consider a few factors based on your production needs. These factors should be considered before choosing the ideal mold type for your manufacturing production:
1.Part Intricacy and Likeness
Assess the intricacy and likeness of the parts you want to produce. If the parts share comparative shapes, sizes, and design requirements, multi-cavity molds are usually more suitable to use. On the other hand, if the parts have different varieties or distinctive design requirements, family molds can give you the flexibility to create all these component variations in a single mold.
2.Production Volume
Think about your expected production volume. Multi-cavity molds are appropriate for high-volume production runs, as they can deliver multiple similar parts at the same time, effectively reducing the manufacturing duration. Meanwhile, family molds are great for lower to medium production volumes, and they offer design flexibility and cost-effectiveness in the tooling and production process.
3.Tooling and Production Expenses
Calculate the estimated tooling and production expenses you need to spend. Multi-cavity molds often require you to pay higher upfront costs because of their complex design requirements and production prerequisites. Also, using the multi-cavity molds might require you to prepare for large expenses over the long haul, especially when you plan to expand your production volume. Family molds, on the other hand, can be more practical and cost-effective for creating different connected parts, as they can use shared tooling for each mold section.
4.Lead Time
Consider the lead time you need for mold configuration, assembling, and testing. Multi-cavity molds often have longer lead times because of their intricacy, accuracy requirements, and testing process. If you are on a tight deadline, family molds might offer faster completion times, as these molds have simpler and less strict design requirements.
5.Maintenance and Quality Checking
Consider the maintenance and quality checking requirements for each mold type. With multi-cavity molds, a problem in one mold cavity might possibly affect the entire multi-cavity molds along with the production results. Family molds offer more versatility in such situations, as an issue in one mold section won’t affect the entire family molds, and it also won’t disturb the whole production process.
Conclusion of mold type selection
Choosing between multi-cavity molds and family molds relies upon a few important factors, including part intricacy, production volume, tooling costs, lead time, and production maintenance. Multi-cavity molds are great for high-volume production of similar parts, while family molds give you flexibility in delivering different yet related parts.
Besides from injection molding services, TEAM Rapid also offers CNC machining services, 3D printing services, die casting services etc to meet your projects needs. Contact our team today to request a free quote now!