Copper electroplating is a widely-used post-processing procedure where a thin layer of copper is used to coat the surface of a metal or any other conductive objects, through a simple electro-chemical process. This technique has been used in broad applications across different industries, thanks to its capability to revamp the surface properties of metal items, improving on their aesthetics and appearance, and give the electroplated metals more practical advantages. This article aims to provide the basic understanding about copper electroplating, including the step-by-step process and common applications where the copper electroplating method is used.
Table of Contents
The Basic Information about Copper Electroplating
Copper electroplating works by following the rule of electrolysis, which includes the utilization of an electrical flow to trigger a certain reaction within an electrolysis bath. You will need to put both the anode (pure copper) and cathode (the designated metal material, such as steel or aluminum) inside the bath chamber before putting any electrical current into it. Electroplating, anodizing, powder coating, electrophoresis, how to choose?
Just when you activate the DC-type electrical current within the bath chamber, the copper particles from the anode, which is made from pure copper, will slowly be transferred onto the cathode, coating the surface of the metal material. You will need to let the electrolysis process develop enough coating for the designated metal material, depending on how thin or thick the copper surface layer you would like to have.
Step-by-Step Process of Copper Electroplating
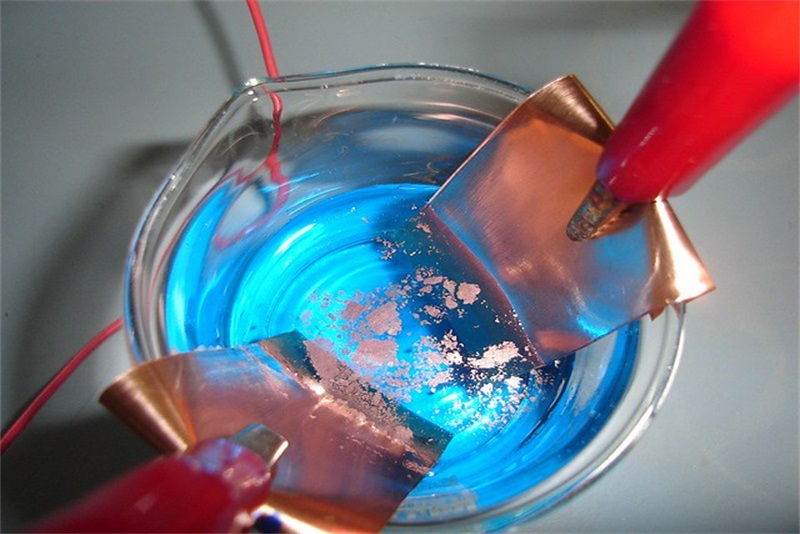
1.Preparing the Metal Material
Prior to electroplating, the outer layer of the metal material to be plated should be completely cleaned and ready. This step includes eliminating dirt, oils, oxides, and different contaminants to guarantee the smooth transfer and coating process of the copper layer. Procedures like de-greasing and corrosive cleaning are often used for this metal preparation process.
2.Preparing the Electrolytic Equipment
The electrolytic equipment, also known as the electrolytic bath chamber, is an important component of copper electroplating. It contains copper sulfate (CuSO₄) as the source of the copper particles, sulfuric acid (H₂SO₄) to enhance the metal conductivity, and various added elements, depending on the end result you would like to get from the copper electroplating process.
3.Preparing for the Copper Electroplating Process
The metal material you want to be plated (steel or aluminum) needs to be placed as the cathode in the electrolytic bath chamber, which belongs to the negative current in the power supply. Meanwhile, the pure copper will need to be connected to the positive current (anode) of the power supply. Both the anode and cathode are then submerged into the electrolytic bath.
4.Copper Electroplating
After turning on the power supply, the DC electric current will flow immediately through the electrolytic equipment, triggering certain reactions inside the electrolytic bath. The pure copper will break down from the anode, forming the copper particles (Cu²⁺) that will go toward the cathode. After reaching the cathode, the copper particles will form elect rons around the surface area of the metal material, resulting in the coating process of a thin copper layer around the metal.
5.Completing the Copper Electroplating Process
During electroplating, different variables like the strength of the electrical current (voltage), temperature of the electrolytic bath, and the electrolytic components need to be configured to accomplish the ideal plating thickness, quality, and appearance. After reaching the ideal plating thickness, you can remove the metal material and then wash and dry it to finish the electroplating process.
Common Applications of Copper Electroplating
Copper electroplating offers a large number of uses across various industries because of its numerous advantages. A few common applications include:
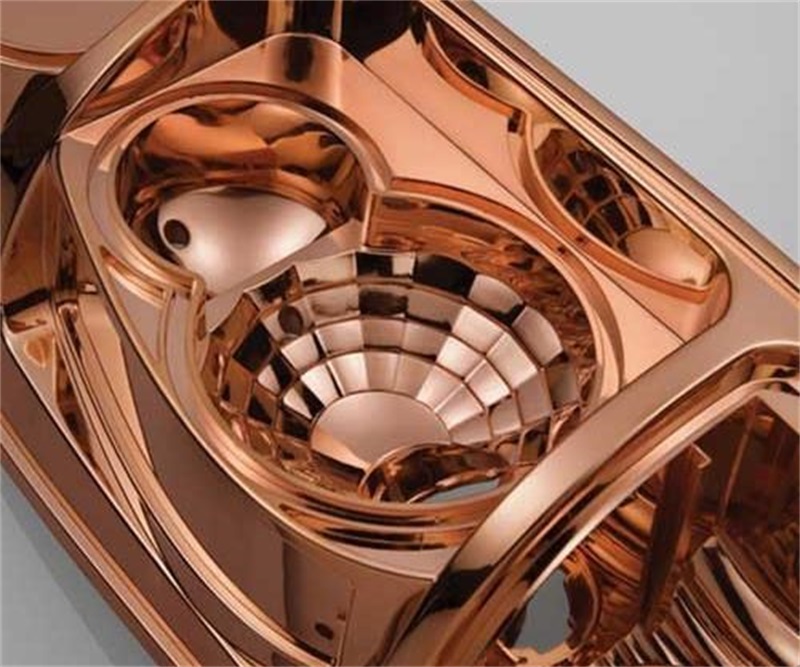
●Gadgets and Electronics Industry
Copper offers an excellent electrical conductivity, making it a preferred metal alloy for electroplating electrical circuits, connectors, wires, and other electrical rapid prototypes and parts. The copper layer is beneficial in improving the flow of electrical currents, improves the solder ability of electrical components, and reduces electrical consumptions on various electronic products.
●Industries Related to Decorations and Ornaments
Copper electroplating is generally utilized in the creation of beautiful ornaments and decorations, whether for indoor or outdoor uses. The electroplating process can create appealing aesthetics for various metal-based objects, adding the shiny and sparkling effects on the surface of various metals, such as plating and others. Copper-plated objects are also perfect for ornamental and decorative uses, which include the applications in various architectural structures and household ornaments.
●Auto Industry
In the auto industry, copper electroplating has different applications for different aspects of vehicle rapid manufacturing. Auto manufacturers can use this process to improve the aesthetics of various auto parts, such as wheel trims, exhausts, and many others. Moreover, copper electroplating can also help prevent corrosion or damages on various auto parts, such as engines and exhaust systems.
●Coin Creation
Electroplating is instrumental in the development and creation of coins. Coins are normally made of a base metal before being electroplated with a copper layer to grant an ideal appearance and to safeguard against regular wear and tear.
●Antimicrobial Coating
Copper has excellent antimicrobial properties, making it the best material to protect against an expansive range of bad microorganisms, bacteria, and parasites. Copper electroplating can be applied to create an antimicrobial coating around everyday objects found in healthcare facilities, public spaces, and also various everyday items, to help with minimizing the spread of diseases.
Antimicrobial coatings can also be applied on various medical devices that are intended to minimize the spread of microscopic organisms, infectious diseases, parasites, and other bad microbes. These antimicrobial coatings also contain some added substances that can help to effectively kill these microorganisms upon contact.
By applying the antimicrobial coatings on different surfaces, such as clinical hardware or medical devices, entryway handles, ledges, and other flat metal objects (benches and tables) found on the public, the spread of harmful contaminants and the transmission of diseases can be minimized.
Conclusion
Copper electroplating is a multi-purpose post-processing technique commonly used across various industries. Its capability to improve various metal surface properties, develop more electrical conductivity, and give better aesthetics makes copper electroplating a preferable post-processing technique to use in various manufacturing activities.
Understanding the basic information and steps associated with electroplating will give various industries more advantages to successfully implementing this process. From gadgets to automobiles, ornamental things to antimicrobial coatings, the wide range of applications of copper electroplating can help manufacturers find new ways to apply this post-processing technique to improve our daily life.
TEAM Rapid offers value-add post finish services to meet your 3d printing, die casting, and injection molding projects needs. Contact our team today to request a free quote now.