Black oxide coating, also called blackening, is a corrosion-resistance method that involves adding a layer of black oxide on the ferrous metal surface. This coating process adds a corrosion-resistance layer to the surface of the ferrous metal, which will help to minimize, slow down, or even eliminate the occurrences of corrosion on the metal. Manufacturers use this method to delay corrosion for various manufacturing equipment, hardware parts, components, and other ferrous metal materials. This guide will help you understand the process and its benefits in rapid manufacturing.
Table of Contents
The Problem with Corrosion in Manufacturing
One of the most common problems in manufacturing is corrosion, which you will get when you are using ferrous metals during your manufacturing process. Ferrous metals are metals that contain iron, and when these metals get in constant contact with oxygen, electricity, hydrogen, and regular dirt particles, they will corrode. What makes corrosion one of the biggest problems in manufacturing? Here are the reasons corrosion is a big problem in manufacturing:
●Loss of function.
Corroded metals will have some function loss, and some features of the metal might no longer be functional. The function that might get lost includes the loss of capability to transfer heat or electricity if the metals belong to certain electrical components.
●Changes in physical appearance.
Corroded metals will also have an uglier physical appearance. Thus, it might not be suitable for you to put corroded metal equipment on display. The changes in physical appearance will get worse as the corrosion gets more intensified later.
●Less efficiency.
Corrosion in ferrous metals can also make the metals to be less efficient in performing their regular function. For instance, corroded metals in your manufacturing equipment might affect your production output and jeopardize the overall production process.
●Loss of metal components on the surface.
The corrosion that happens in ferrous metals can damage the metal components on the surface. Thus, the corroded parts of the metals will no longer have normal metal properties on it.
●Damaged equipment or components.
The more corrosion that happens in ferrous metals in your manufacturing equipment, the more the equipment or component will get damaged. This can render your equipment to be unusable unless you can replace the corroded metals with new ones.
Black Oxide Coating – The Solution for the Corrosion Problem
It is a coating process that involves adding black oxide to the surface of ferrous metals. This process helps add resistance to corrosion for the metals that are otherwise susceptible to corrosion. With this coating, you can also add extra protection against corrosion by layering the ferrous metals even more with wax or oil.
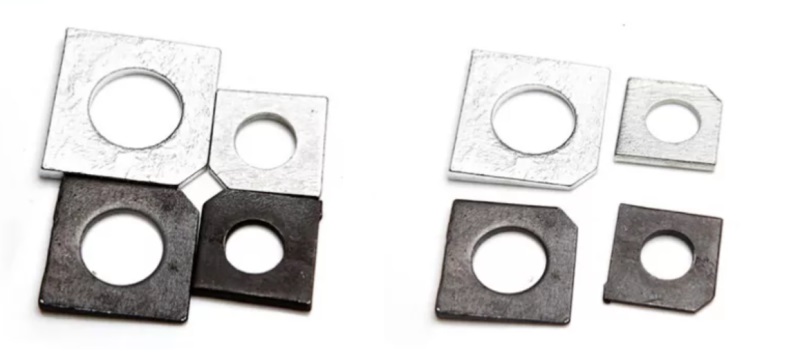
There are various metals that are suitable for this treatment, such as zinc, stainless steel, copper, silver solder, powdered metals, and copper-based alloys. In most cases, this coating can help prevent ferrous metals from getting corroded. However, black oxide coating will not give 100% protection against corrosion, as the metals can still corrode when you place them in certain environments. If the coating is not satisfied for your project, maybe you can consider about anodized aluminum(what is anodized aluminum).
The Primary Advantages of Black Oxide Coating
There are various methods to add corrosion resistance to ferrous metals. However, black oxide coating has some benefits compared to other similar methods. With this process, you don’t need to worry about altering the metal CNC turning parts’ appearance when you apply this coating on the surface. Also, you will keep the metal parts free from light reflection. Here are some primary advantages of this coating:
●Adding mild corrosion resistance to ferrous metals.
The black oxide coating is effective in adding mild corrosion resistance for certain ferrous metals. After this application, ferrous metal objects such as CNC milling parts will not corrode fast when you use them. You can even add extra corrosion-resistance layers on top of the coating.
●Black oxide coating is an Affordable corrosion resistance method.
Compared to more advanced corrosion resistance methods, such as chrome plating, black oxide coating is much more affordable to use for manufacturers. They can apply this coating method in large volumes at a time.
●black oxide coating is a Quick application.
It is a corrosion resistance method that is quick and easy to do. Manufacturers don’t need to spend too much time applying the coating to their ferrous metal objects.
●It doesn’t change the size of the objects after black oxide coating.
You don’t need to worry about changing the ferrous metal objects’ size or shape when applying this coating. You just add a thin surface layer on top of the ferrous objects so that it won’t disturb the functions of the metal objects later.
Black Oxide Coating Applications
The primary applications of the black oxide coating are for fasteners, such as nuts and bolts, along with other small hardware components. However, there are still various other applications for black oxide coating in various manufacturing processes such as in sheet metal parts and die casting for industrial component. Here are some of the black oxide coating applications in manufacturing:
●Fasteners.
Fasteners such as nuts and bolts often use black oxide coating to prevent rusting. These include fasteners used in various industries, such as automotive, consumer electronics, and more.
●Gears and switches.
Rusted gears and switches might damage the equipment. Thus, manufacturers often use this coating for the gears and switches used in various equipment.
●Clipping tools and cutters.
You can find black oxide coating applications in various clipping tools for gardening, as these tools are susceptible to rusting. Wire cutters are also a common application for this coating method.
●Cans.
You can find various cans that get the blackening treatment to prevent corrosion on the metal surface. This process often gets applied to oil cans in most vehicles.
●Fixtures.
Various fixtures get the blackening treatment to keep them solid and prevent any corrosion that might damage the fixtures. You can often find the blackening application on fixtures used in store shelves.
Conclusion
As a protection method against corrosion, black oxide coating is an affordable and effective method that manufacturers can apply to protect ferrous metals from corrosion, the process is used widely in rapid prototyping services and volume manufacturing. It provides you with a mild corrosion resistance property, which you can improve by using oil or wax on top of the coating.
The black oxide coating is suitable for adding corrosion resistance to ferrous metal objects, which you can apply in large batches, with a quick and easy application process. Want to learn more about the post finish for your upcoming projects? Contact us now!