In manufacturing, manufacturers often use rough metals to create various parts and components, and unless these metals get electroplated, they might not work in the best way. Thus, the electroplating process becomes an important part of the manufacturing progress, which helps the manufacturers to improve the metal properties they are working on. This process can help prevent corrosion, improve metal thickness, smoothen the metal surface, and more. In this guide, you can learn about the electroplating process, including its definition, working principle, and application.
Table of Contents
What is the Electroplating Process?
Electroplating means adding an outer coating layer for certain metals by using hydrolysis. The primary purpose of this process is to protect the metals against corrosion. However, by adding a thin protective layer on the metal surface, you can also add various other properties to the metal. The added properties you can apply to the CNC turning or die cast metal by using the electroplating process include improved aesthetics, improved durability, improved metal thickness, and improved protection against radiation.
With the electroplating process, you can also improve the metal’s electric conductivity and surface finish. It will make the metal look shinier than before, with a better surface finish that can improve the functionality of the metal when used in various applications.
The Working Principle of the Electroplating Process
For the electroplating process to work, you will need to use a certain liquid electrolytic solution along with some electric currents. Then, you will need to prepare the metal you would like to electroplate. In this example, you will use copper as the metal you would like to plate, and you will use the tin as the plating material.
To electroplate the copper metal, you will need to immerse both the copper metal and tin plating inside the electrolytic liquid solution. You will need to connect the tin plating to the anode and connect the copper material to the cathode. Then, you can deliver the DC electric currents to the electroplating equipment to start the electroplating process.
In this example, the tin plate will dissolve, and then the dissolved tin plate will coat the surface of the copper material during the hydrolysis process. As a result, you will get the copper material coated with tin after the process is complete.
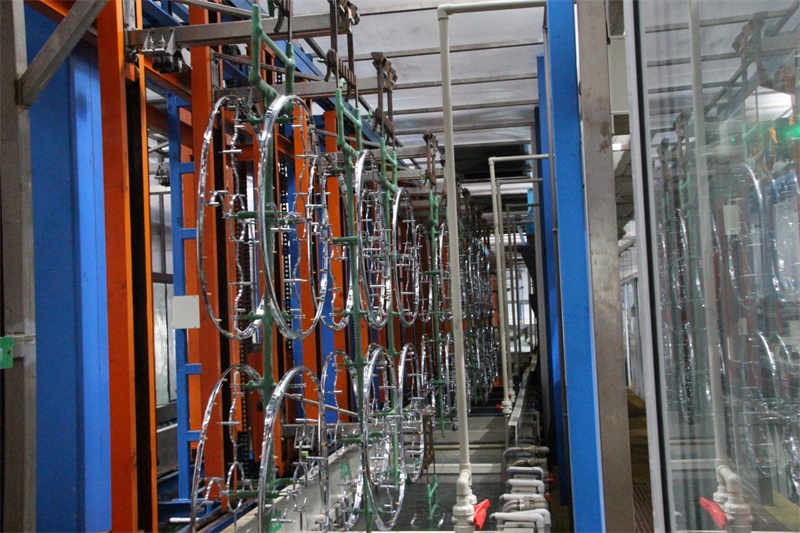
Electroplating Process Benefits
In rapid manufacturing, electroplating offers many benefits, which include creating a new outer layer on certain metals to add a corrosion-resistant property to them. By doing that, you can also enhance or improve the metal’s appearance, making it shinier looking. There is a wide range of benefits you can get from electroplating, and manufacturers use this process to improve the metal they are working on.
1. Putting on an anti-corrosion coating.
The primary benefit of electroplating that manufacturers want to get is to provide an anti-corrosion coating to the rapid sheet metal they are working on. This anti-corrosion coating makes it easier for the manufacturers to use the metal for the long term, without worrying about it getting rusted or corroded.
2. Improving the overall look of the metal by the Electroplating process.
Electroplating can add a more beautiful and luxurious look to the metal object, which is the reason manufacturers use this process in jewelry production. Gold and silver are common metals that can get electroplated to enhance their aesthetics.
3. Improving the thickness of the metal.
You can also add thickness to the sheet metal prototype or other sheet metal with electroplating. The improved metal thickness can add more durability to the metal. The metal will last longer, as it has more strength to withstand various damages.
4. Protecting from friction and regular wear by the electroplating process.
For some metals, such as gold and silver, it’s important for you to protect them from regular wear and friction. It gets even more important for the metals used for jewelry, as you will need to maintain their high value by protecting them from regular wear and tear. Electroplating can also be an excellent solution that will help you protect the metals from scratches because of friction and regular wear.
5. Boosting the metal’s electrical conductivity.
Some metals are great for conducting electricity, such as copper and gold, which is the reason manufacturers use them as electrical components. By using the electroplating process, you can improve the metal’s electrical conductivity to make it much better at delivering electric currents to various electronic devices.
Applications of Electroplating
Electroplating is a common manufacturing process used for various applications across a wide range of industries, ranging from automotive to jewelry. This method of adding a coating layer to the metal surface can also provide various enhanced metal properties, making the metals work much better in their applications. Here are some common applications of electroplating:
1. Consumer electronics.
Electroplating can help increase the electrical conductivity of various metals, and manufacturers are using this process in plenty of consumer electronic products after CNC milling services. You can electroplate the electrical components in various electronic products, along with their wiring system. PCB (Printed Circuit Board) is also a common electronic component where electroplating gets applied.
2. Jewelry.
Electroplating is a process that can help protect jewelry, such as gold and silver, from getting scratched. Manufacturers use the electroplating process to add more value to the jewelry they are selling to the customers. With this process, you can also make the jewelry look shinier and much more luxurious.
3. Metal purification.
The electroplating process is also important for metal purification, allowing metal such as copper to get purified so that the manufacturers can use it better in the electrical wiring system and other applications. Without the purification process, copper metal might not have its maximum capability to conduct electricity in various electrical applications.
4. Automotive industry.
Various car parts also need electroplating to help increase their thickness and durability. Most car parts have rough surfaces, and the electroplating process can help smoothen out the metal surfaces, making them more appealing to look at and more functional.
5. Radiation prevention.
Electroplating can also protect the metals from various radiation, which can cause certain damage to the metal surface. This way, any radiation caused by natural occurrences, along with abrasion, can’t damage the metals.
Conclusion
Electroplating is an important process in manufacturing and rapid prototyping services, which can help manufacturers enhance the properties of certain metals. The primary purpose of electroplating is to protect the metal against corrosion, but there are other purposes of this process that can benefit the manufacturing industry.
The electroplating process is suitable for various industrial applications, such as jewelry production, automotive, consumer electronics, and more. Looking for value-add services for your insert molding and other CNC machining parts? Contact TEAM Rapid for helps now!