In many industries, it is sometimes necessary to build parts or components that unite the plastic and metal materials to make a functional and unified product. You can use insert molding to perform this manufacturing process. The insert molding in manufacturing process offers many advantages for manufacturers and businesses, with many potential applications throughout today’s modern industries.
Table of Contents
- 1 The Benefits of Insert Molding in Manufacturing
- 2 An Additional Injection Molding Step is Unnecessary
- 3 Various Applications of Insert Molding in Manufacturing
- 3.1 Insert molding in manufacturing: Screwdrivers
- 3.2 Insert molding in manufacturing: Knobs
- 3.3 Medical Devices
- 3.4 Electrical Wiring Systems
- 3.5 Insert molding in manufacturing: Insulated Pipes
- 3.6 Surgical Devices
- 3.7 HVAC Systems
- 3.8 Aircraft Control System
- 3.9 Insert molding in manufacturing: GPS Navigation System
- 4 Conclusion
The Benefits of Insert Molding in Manufacturing
Insert molding offers advantages that will make your production process smoother and cheaper. This manufacturing process allows you to integrate a metal insert into an existing plastic part without creating a separate mold. Here are the benefits of insert molding in rapid manufacturing:
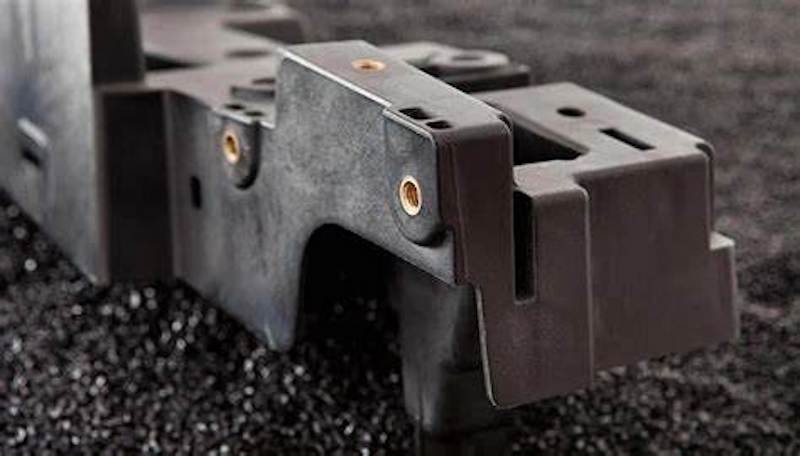
Add More Strength to the Part You Are Building
Insert molding allows you to insert a metal part into the plastic part you produce. This metal part addition will help strengthen the structure of the overall plastic part you are building. It will help add more durability and support for the plastic part, such as when you create a handle using the insert molding process.
Enhance Your Part Design
Adding a metal part to the primary plastic mold can significantly enhance your part design. You can do it without changing the plastic part’s overall mold design. You can also use the metal insert to make your plastic part more feature-rich.
Insert molding in manufacturing: Lower the Overall Part Production Costs
With insert molding, you don’t need to build another mold/ rapid tooling to join two parts together. You just need to insert the metal part into the existing mold and get your plastic part production done fast. In turn, it can lower the production costs for your plastic parts and make the production process run fast. It’s easier to meet your production deadline with insert molding.
An Additional Injection Molding Step is Unnecessary
Inserting the additional metal part is a straightforward process in insert molding. So, you don’t need to perform more injection moulding steps for this production process. It’s a simple process of putting a metal insert into the existing mold before filling the mold with molten plastic materials.
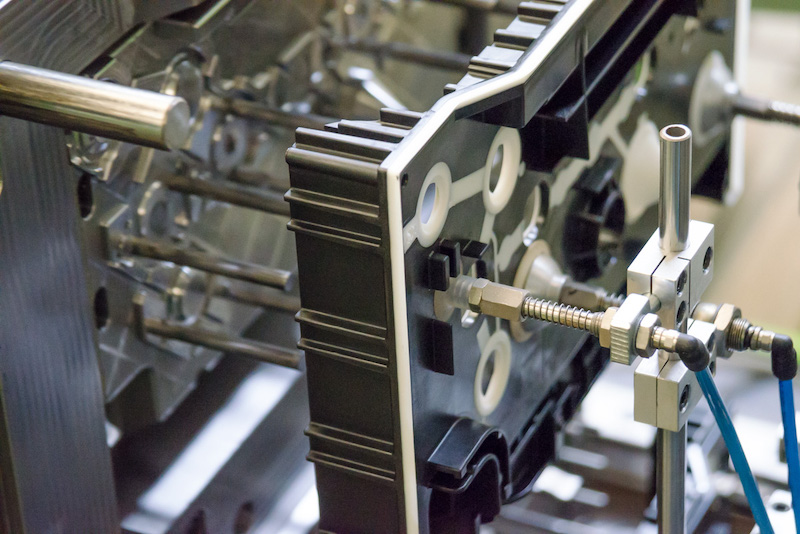
Create a Unique Combination of Metal and Plastic
Insert molding allows you to combine two different materials into one mold. You can join plastic and metal materials in one mold with insert molding. Insert molding can integrate various functions and designs between the two material types depending on your project requirements.
Design Variations
There are various types of metal inserts you can utilize during the insert molding process. Also, you can have a lot of flexibility in designing the plastic part mold. With insert molding, you will have plenty of design variations for the metal inserts and plastic parts for your production. You can offer different product models to your customers using the insert molding process.
Easy to Add New Features to Your Plastic Parts
Sometimes, you might need to add more features to the plastic parts you produce with injection molding. The best way to do it without changing your plastic part’s mold design or building a new mold for your plastic part is to use insert molding. You can add a variety of metal inserts with different functions to add more features to your existing plastic parts.
Various Applications of Insert Molding in Manufacturing
Insert molding has become a regular manufacturing process for many industries in all parts of the world. The applications of this injection molding type include automotive, aerospace, consumer electronics, medical and surgical, and various other industries. The followings are the applications of insert molding in manufacturing:
Insert molding in manufacturing: Screwdrivers
To produce screwdrivers, you will make the handle from plastic materials, while the metal part will get inserted into the handle during the plastic molding process. It is an ordinary application of insert molding for everyday tools and appliances you use around the house.
Insert molding in manufacturing: Knobs
You can create knobs for doors and other furniture with insert molding. The handle will get produced from plastic materials, and the screw part will get inserted into the plastic mold during the injection molding process.
Medical Devices
Many medical devices also combine plastic molded parts with metal parts, meaning that insert molding is essential for these devices’ production. It is also an economical way to produce medical devices for various purposes in low volume manufacturing services and large quantities production.
Electrical Wiring Systems
Electrical wiring systems in your household and consumer electronic products will need to use the insert molding process in their production. You need to create the primary plastic part that houses the electrical wiring system before inserting the wiring and metal parts via the insert molding process.
Insert molding in manufacturing: Insulated Pipes
Creating insulated pipes will require an insert molding process to get it done. You need to design the mold for the primary plastic pipe part and insert the metal insulation part inside the mold. Also, you can combine these pipes and install them around your house or any other building.
Surgical Devices
Performing medical surgeries carries various challenges for surgical doctors. Surgical devices are essential to help these healthcare professionals perform their surgical operations. You can create a variety of surgical devices using the insert molding process by combining plastic and metal parts into the same mold.
HVAC Systems
You can install HVAC systems around your house, school, office, and other buildings. These heating, air conditioning, and ventilation systems consist of an integration of metal and plastic parts. It’s essential to use the insert molding process to combine the metal and plastic parts for the HVAC system installation.
Aircraft Control System
The aircraft control system has plenty of electrical wirings installed around the plastic part enclosure. Insert molding plays a considerable role in building the entire aircraft control system, which is the reason insert molding has become an essential part of the aerospace industry.
Another technological product made using the insert molding process is the GPS. The navigation system becomes an integral part of any vehicle for the aerospace and transportation industries. It is necessary to utilize the insert molding technique to combine the GPS’s metal parts, wiring, and base plastic materials.
Conclusion
Insert molding offers various benefits in the mass production of parts and components in several industries, such as medical, aerospace, home appliances, and other industries. The uncomplicated process of combining metal and plastic parts can give manufacturers better production efficiency and faster production speed. Use insert molding for your next production plan whenever you need to use metal and plastic material together.
Besides from insert molding, TEAM Rapid also offers rapid prototyping, CNC machining, and die casting to meet your projects needs. Contact our team today to request a free quote now!