Injection moulding is deeply embedded in the structure of plastic manufacturing and is a key process that allows the production of complex and resilient parts. Threads, intricately interwoven throughout this process. Serving as architects of heightened functionality and strength for these components, constituting a critical juncture in manufacturing. In the following delve, we unravel the profound significance of injection molding threads, spotlighting their integral role in the expansive landscape of plastic manufacturing.
Table of Contents
Deciphering the Nuances of Injection Molding
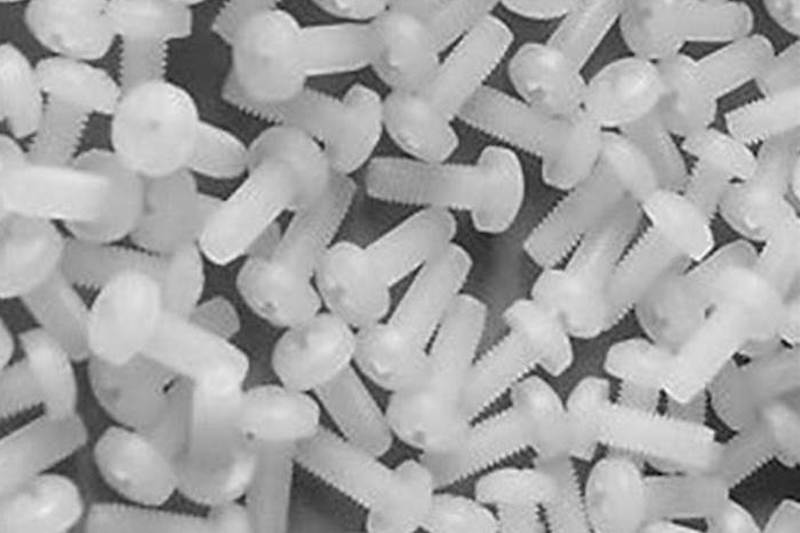
Versatility in Geometries
At the core of plastic part production lies plastic molding, an extensively employed manufacturing process. It operates by injecting molten plastic into a mold, allowing it to cool and take on the desired form. This adaptable technique accommodates intricate geometries and an array of part sizes, ensuring a malleable approach to production.
Economic Advantages
The significance of injection molding in plastic manufacturing is profound, delivering many advantages. Such as elevated production rates and unwavering tolerances. Beyond this, it opens the door to the use of diverse materials, slashes labor costs, and minimizes losses from scrap, fostering an economically sound production process.
Superior Surface Finishes
Beyond its economic prowess, injection molding stands out for its ability to yield top-notch parts with impeccable surface finishes. Rendering it ideal for crafting visible components in sectors like automobiles, electronics, and medical equipment. This prowess is facilitated by the process’s high-pressure injection, ensuring thorough occupation of the mold cavity and allowing for the creation of intricate details.
Automated Efficiency
Adding to its allure is the highly automated nature of injection molding, streamlining production and effectively trimming labor expenses. This characteristic not only enhances cost-effectiveness but also accelerates the manufacturing pace. Positioning it as a financially viable strategy for large-scale plastic part production.
The Dynamic Impact of Injection Molding Threads
In the intricate realm of injection molding, threads emerge as silent architects, wielding substantial influence over the functionality and longevity of molded components. These meticulously crafted ridges or helical projections intricately interlace with other elements. Bestowing a considerable boost to the strength and utility of the final product.
Versatility in Functional Constituents by injection molding threads
Threads assume a versatile role, acting as indispensable functional constituents across a spectrum of plastic components. Their integration into molded parts facilitates steadfast fastening, enabling the assembly of diverse industrial products. From containers and caps to medical devices and automotive elements, threads deliver crucial sealing and interconnecting capabilities, ensuring operational dependability.
Reinforcing Structural Integrity
Beyond functional prowess, threads play a pivotal role in fortifying the structural integrity of molded components. Their intricate design adeptly disperses stress, eliminating weak points and fortifying the overall architecture. This reinforcement proves especially vital in applications demanding heightened durability and load-bearing capacity, such as machinery parts or structural components.
The impact of threads extends into the functionality of consumer products. In applications like bottle closures or fittings, precisely engineered threads ensure efficient sealing and guarding contents against spillage or contamination. Similarly, in medical devices, these threads guarantee secure connections, a critical aspect of maintaining sterile environments and operational safety.
Specialized Functionalities
Moreover, threads contribute to specialized functionalities, exemplified in electrical connectors or plumbing fixtures. These precision-crafted threads facilitate seamless connections, ensuring electrical conductivity or fluid tightness and showcasing their adaptability across diverse applications.
Streamlining Production Processes
Additionally, threads streamline the production processes within injection molding, obviating the need for secondary operations like machining or additional assembly. This operational efficiency not only slashes production costs but also amplifies overall effectiveness by eliminating post-molding modifications.
The intricate product and mold design considerations of threads in injection molding demand meticulous attention to factors such as pitch, depth, and profile. Precisely engineering these features guarantees optimal performance, reliability, and seamless integration within the intended application.
Threads transcend their conventional role as mere structural components in injection molding, emerging as integral elements influencing the robustness, functionality, and adaptability of molded parts. Their nuanced design and strategic integration not only facilitate secure connections but also fortify the structural integrity of diverse components. As foundational elements for secure fastening and elevated functionality, threads stand as stalwarts, propelling precision and innovation in injection molding processes to meet the dynamic demands of both industrial and consumer landscapes.
In the intricate landscape of injection molding, the molding of threads presents a tapestry of challenges, demanding surgical precision and strategic solutions for optimal outcomes. These challenges emanate from a confluence of factors, weaving together intricate design specifications, material intricacies, and the constraints inherent in the rapid manufacturing process.
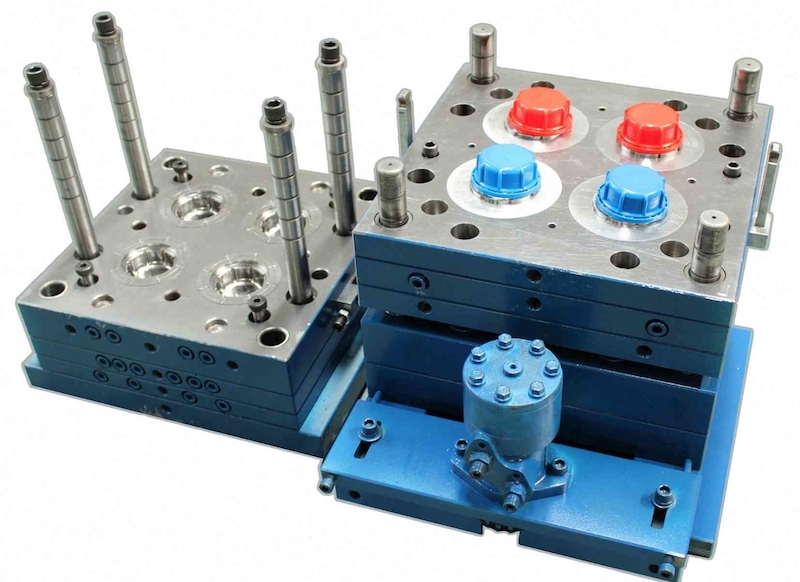
Achieving Exact Thread Geometry
A primary challenge surfaces in the pursuit of achieving exact thread geometry within the mold. The intricate design, entailing variables like pitch, depth, and profile, mandates scrupulous mold design and precise machining to faithfully replicate the intended thread specifications. Any deviation from these exacting dimensions threatens to compromise the functionality and compatibility of the threads.
Material Selection Challenges in injection molding threads
Another formidable challenge arises in the realm of material selection. The choice of plastic material wields a profound impact on the success of thread molding. Some materials gracefully flow, ensuring the mold cavity is uniformly filled, while others pose hurdles in capturing intricate thread details. Ensuring material harmony with the molding process becomes pivotal in navigating potential issues related to flow dynamics, cooling, and shrinkage.
Tackling defects during the molding process stands as a conspicuous hurdle. Issues like air trapping, sink marks, or warping can cast a substantial shadow on thread quality. Air traps within the mold may birth incomplete filling, resulting in voids or weak spots in the threads. Sink marks and warping, offspring of uneven cooling or excessive material shrinkage, can distort thread dimensions and functionality.
Defect Mitigation Strategies
Mitigating these challenges demands a multi-pronged strategy, commencing with meticulous design and analysis. Advanced design software becomes the ally, facilitating the creation and evaluation of precise thread geometry that aligns seamlessly with mold manufacturing capabilities. The adoption of mold flow analysis proves invaluable, offering foresight into material flow behavior, optimizing gate locations, and curtailing air trapping issues.
Material selection emerges as a linchpin in overcoming challenges during thread molding. Rigorous material compatibility studies and the choice of resins with favorable flow properties become guiding principles in achieving intricate thread details while minimizing defects. The infusion of additives or reinforcements becomes a strategic move, elevating material flow and structural integrity, ensuring uniform filling, and reducing defects.
Fine-tuning process parameters during molding becomes paramount. The adjustment of injection pressure, temperature, and cooling rates emerges as a delicate dance to minimize sink marks and warping while ensuring complete mold cavity filling. The incorporation of proper venting systems within molds becomes a savior, expelling trapped air, minimizing voids, and elevating overall part quality.
Moreover, the relentless upkeep and calibration of molding equipment become imperative in the pursuit of precision and consistency in thread molding. Regular inspections and adjustments to molds and machinery serve as the vanguard, warding off deviations that might compromise thread quality and functionality.
Comprehensive Orchestration in Injection Molding Threads
Addressing the labyrinth of challenges in molding threads demands a comprehensive orchestration involving meticulous design, astute material selection, process optimization, and the unwavering maintenance of equipment. The strategic deployment of measures throughout the molding process empowers manufacturers to deftly navigate hurdles, ensuring the low volume manufacturing and production of high-quality molded threads that stand resilient against stringent industry standards and functional requisites.
Conclusion
Navigating the intricacies of molding threads through injection molding demands meticulous precision in design, material selection, and process optimization. The challenges posed by intricate geometry, material intricacies, and potential defects underscore the pivotal importance of overcoming these hurdles. Threads, as a result, assume a critical role in fortifying structural integrity, enabling functional versatility, and catalyzing innovation within plastic manufacturing. Their indispensable significance resonates across diverse industrial applications, underscoring their pivotal role in shaping the landscape of manufacturing.
Besides from injection molding, TEAM Rapid also offer rapid prototyping, CNC machining, and die casting to meet your projects needs. Contact our team today to request a free quote now!