Comprehending the intricacies of thread design considerations in injection moulding emerges as a pivotal facet within the manufacturing landscape. This intricate procedure revolves around the art of crafting threads for plastic components through injection molding, wielding considerable influence over the functionality and quality of the end product. The significance of this domain resonates profoundly with professionals engaged in the realms of product design, production and rapid manufacturing.
Table of Contents
Fundamentals of Injection Molding
Widely embraced in the fabrication of plastic components, plastic molding stands as a pervasive technique in manufacturing. This method revolves around the injection of molten plastic into a mold, culminating in the creation of a component boasting the desired shape and dimensions after the cooling and ejection phases.
The initial stage involves the preparation of the plastic material, subjecting it to heat until it transforms into a molten state. Following this, the molten plastic undergoes injection into the mold under substantial pressure. This pressure persists until the plastic cools and solidifies, adopting the contours defined by the mold.
Upon completion of the cooling process, the mold unfurls, releasing the formed part, only to promptly close again for the subsequent cycle. Industries spanning automotive, low volume manufacturing services, medical, and consumer electronics favor this method for its adeptness in swiftly and precisely generating intricately shaped components while minimizing material wastage.
Yet, the crux of the injection molding process lies in the mold’s design, with injection molding thread design considerations playing a pivotal role in its success. Crafting threads demands a methodical approach that takes into account the properties of the plastic material, the intended use of the part, and the intricacies of the molding process.
For those immersed in the creation of plastic parts, a grasp of both the fundamentals of injection molding and the subtleties inherent in thread design becomes imperative. This comprehension ensures the realization of optimized outcomes in the multifaceted realm of injection molding.
Optimal Thread Design Configuration in the Context of Injection Molding
The role of thread design within injection molding extends far beyond a mere detail; it serves as a linchpin influencing the very essence of a product’s functionality and quality. These threads, omnipresent in plastic parts from bottle caps to automotive components and medical devices, demand precision in their formation to ensure an optimal fit and function.
Delving into the intricacies, the profile of the thread, encapsulating its shape, pitch, and size, is meticulously tailored to align seamlessly with the part’s intended use and material properties. Coarser threads emerge as facilitators of easier molding, effectively distributing stress, while specific applications call for the subtlety of finer threads tailored to distinct purposes.
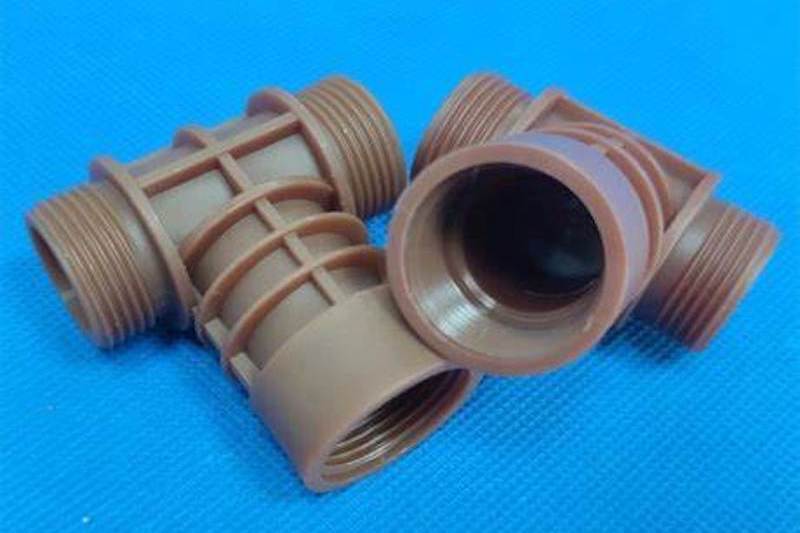
The positioning and alignment of the thread within the part emerge as critical factors influencing both molding ease and structural integrity. Threads situated at the part’s periphery or aligned with the mold’s pull direction may impede removal or compromise specific areas within the part.
Moreover, achieving a seamless integration of mold design intricacies with the threads may involve the incorporation of mechanisms like unscrewing or collapsible cores. These mechanisms play a pivotal role in ensuring the smooth ejection of the part without causing any damage to the meticulously designed threads.
The landscape of thread design in injection molding proves to be multifaceted, demanding meticulous attention across various dimensions. However, mastery of adept design strategies culminates in the production of high-quality, functional threaded parts through the intricate dance of injection molding processes.
Considerations for Thread Design
The creation of threads for injection molding demands a meticulous examination across various domains. Here’s an intricate breakdown of the key considerations:
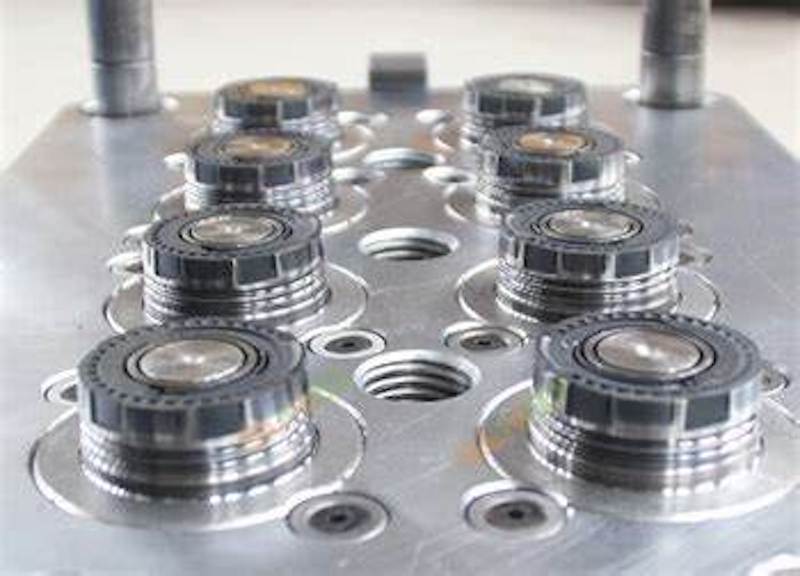
Material Selection
Choosing the right material stands as a foundational decision impacting thread design. Material characteristics, including distinct shrinkage rates, wield a direct influence on thread precision. The interplay of strength and flexibility further dictates the performance and longevity of the threads.
Thread Geometry
The pivotal embrace of the thread’s shape, pitch, and size is central to effective design. Coarser threads, simplifying the molding process and enhancing stress distribution, contrast with finer threads tailored for specific applications. The nuances of shape extend their influence, impacting both strength and utility.
Thread Location and Orientation
Strategic thread positioning becomes imperative, as placing threads at edges or aligning them with mold pull directions may impede part removal or compromise specific sections. Thoughtful consideration in this realm ensures optimal outcomes.
Mold Design
Crafting molds that seamlessly accommodate threads involves the integration of mechanisms such as unscrewing or collapsible cores. This careful planning ensures the preservation of thread integrity during the crucial part of the ejection phase.
Molding Conditions
The trifecta of injection speed, packing pressure, and cooling duration directly shapes the quality of threads. Precise optimization of these factors becomes paramount for achieving the desired thread formation and minimizing defects. Mold flow analysis is need if available.
Post-Molding Operations
Certain designs may necessitate post-molding actions like reaming or tapping to achieve the desired accuracy or finish. These considerations become integral aspects during the initial design phase, contributing to the overall success of the thread design.
Thread design in the realm of injection molding emerges as a multifaceted process intricately woven with material properties, molding nuances, and end-use requisites. A thorough contemplation of these aspects lays the groundwork for the creation of threads that not only prove functional and enduring but are also economically viable in the broader landscape of manufacturing.
Challenges and Innovations in Thread Design
The intricate realm of thread design within injection molding unfurls several challenges, demanding meticulous consideration for triumphant outcomes. Frequent hurdles include inadequate material flow, culminating in air traps or incomplete fills, posing potential threats to thread integrity. The intricacies of thread design also complicate the demolding process, introducing difficulties in achieving the desired form.
Nevertheless, a repertoire of effective solutions stands ready to counter these challenges. Strategic enhancements in mold design, coupled with the optimization of material flow paths, serve to assuage filling issues, fostering a more uniform and complete thread formation. The integration of mechanisms such as unscrewing or collapsible cores emerges as a potent strategy, facilitating seamless demolding without compromising the delicate intricacies of the threads.
Moreover, pivotal adjustments in molding conditions, including injection speeds and packing pressures, emerge as instrumental in addressing concerns related to incomplete packing, resulting in a more refined and well-formed thread.
The implementation of these innovative solutions, complemented by a thorough analysis and refinement during the design phase, stands as a crucial linchpin in surmounting the challenges entwined with thread design in injection molding. This holistic approach ensures the production of threaded parts that not only meet but exceed industry standards in both quality and precision.
Conclusion of thread Design Considerations
The bedrock of robust and functional parts in injection molding lies in the comprehensive design of threads, encompassing material selection, geometric precision, and meticulous mold considerations. Examining successful case studies underscores the pivotal role played by careful design and seamless technological integration. These insights serve as a robust testament to the overarching significance of thorough thread design, contributing to the elevation of standards within the injection molding sector.
Besides from injection molding, TEAM Rapid also offers rapid prototyping, CNC machining, and die casting to meet your projects needs. Contact our team today to request a free quote now!